Tóm tắt
Để nâng cao hiệu quả và khả năng cạnh tranh, các nhà máy lọc dầu phải tiến hành tối ưu hóa, nhằm tiết giảm chi phí sản xuất thông qua lựa chọn, pha trộn dầu thô, xác định cơ cấu sản phẩm, tiết kiệm năng lượng… Quá trình tối ưu hóa có thể tiến hành từ cấp phân xưởng đến toàn bộ nhà máy và được hỗ trợ bởi các phần mềm mô phỏng. Tuy nhiên, các mô hình sử dụng thường là các “gói” đã được lập trình sẵn trong phần mềm hoặc xây dựng bởi tư vấn, gần như không thể can thiệp trực tiếp vào cơ chế nhiệt động học của quá trình.
Phân xưởng Reforming xúc tác (CCR Platforming) của Nhà máy Lọc dầu Dung Quất đang sử dụng CCR model (Refsim) là gói được xây dựng sẵn bởi KBC dựa trên phần mềm PetroSim. Tuy nhiên, mô hình này không cho phép các kỹ sư tại nhà máy can thiệp về mặt động học để tiến hành tối ưu hóa. Trong nghiên cứu này, mô hình mô phỏng phân xưởng CCR Platforming Nhà máy Lọc dầu Dung Quất được xây dựng dựa trên cơ sở mở rộng các cấu tử isoparaffin và điều chỉnh mô hình động học của Krane có xét đến ảnh hưởng của nhiệt độ, áp suất. Sau khi kiểm chứng với kết quả vận hành thực tế, mô hình mô phỏng sẽ được sử dụng để tính toán các thông số của quá trình, đánh giá khả năng tối ưu hóa các điều kiện vận hành của phân xưởng CCR Platforming Nhà máy Lọc dầu Dung Quất.
Từ khóa: Reforming xúc tác, mô hình động học, tối ưu hóa, Nhà máy Lọc dầu Dung Quất.
1. Giới thiệu
Reforming xúc tác là quá trình chuyển hóa phân đoạn naphtha nặng có trị số octane hấp thành xăng reformate có trị số octane cao và cung cấp nguồn khí H2 cho các phân xưởng xử lý bằng H2. Ngoài ra, sản phẩm reforming xúc tác chứa các hydrocarbon thơm (BTX: benzene, toluene, xylene), được sử dụng làm nguyên liệu cho công nghiệp hóa dầu [1].
Reforming xúc tác là quá trình rất phức tạp với lượng lớn các phản ứng xảy ra từ nhiều cấu tử khác nhau (n-paraffin, iso-paraffin, naphthene và aromatic) như dehydro hóa và dehydroisome hóa các naphthene thành aromatic, dehydro hóa paraffin thành olefin, dehydro hóa đóng vòng các paraffin và olefin thành aromatics, isomer hóa hoặc hydroisomer hóa thành các isoparaffin, isomer hóa alkylcyclopentane và các aromatics, hydrocracking các paraffin và naphthene thành các hydrocarbon nhẹ hơn. Việc mô phỏng mô hình động học chi tiết cho từng cấu tử rất phức tạp, nên nhóm tác giả thực hiện mô phỏng mô hình động học theo các nhóm cấu tử với quy mô trung bình. Phương pháp gói (lumping), được sử dụng, đảm bảo việcchia gói đủ chi tiết, số lượng các gói đủ để đại diện cho các cấu tử mong muốn trong dòng vật chất và đủ để đảm bảo mối quan hệ giữa các biến quá trình và tốc độ phản ứng.
Trên cơ sở đó, mô hình động học của Krane [2] đã được nhóm tác giả sử dụng, tiến hành mở rộng và điều chỉnh để thỏa mãn được sự đơn giản của mô hình gói nhưng vẫn đảm bảo độ chính xác cần thiết. Kết quả mô phỏng với số liệu đầu vào từ Nhà máy Lọc dầu Dung Quất được so sánh với kết quả vận hành thực tế.
2. Xây dựng mô hình động học
2.1. Các mô hình đã được nghiên cứu
Năm 1959, Smith RB [3] lần đầu tiên đề xuất chia phân đoạn naphtha thành 4 gói cấu tử gồm: paraffin, naphthene, aromatic và hydrocarbon nhẹ (< C5). Do tính đơn giản, mô hình này vẫn đang được sử dụng cho các nghiên cứu chỉ dừng lại ở mức tính toán đơn giản, không đòi hỏi độ chính xác cao. Năm 1970, công trình đầu tiên quan tâm đến sự khác nhau trong quá trình phản ứng của các naphthene vòng C5 và C6 được thực hiện bởi Henningsen và Bundgaard-Nielson [4]. Năm 1973, Kmak phát triển mô hình gồm 22 gói cấu tử, sau đó Froment phát triển lên thành 28 gói cấu tử. Các tác giả đã xác định giá trị chính xác cho nhiệt phản ứng và năng lượng hoạt hóa của các phản ứng trong mô hình. Các phản ứng trong một số mô hình được thể hiện trong Hình 1.
|
Hình 1. Một số mô hình động học đã công bố [6] |
Năm 1987, Ramage [5] đã phát triển mô hình động học chi tiết dựa trên số liệu nghiên cứu pilot quy mô công nghiệp. Mô hình này bao gồm 13 gói cấu tử có thêm gói hấp phụ trên bề mặt xúc tác đã mô phỏng chính xác thiết bị phản ứng thương mại và được Mobil áp dụng cho các nhà máy lọc dầu.
2.2. Mô hình động học của Krane
Mô hình do Krane [2, 6] xây dựng dựa trên nhóm các cấu tử thành cấu tử giả là hỗn hợp isomer của các cấu tử có cùng bản chất (các paraffin, naphthene và aromatic có cùng số carbon). Những gói này gồm: các gói paraffin có số C từ 1 - 10 và các gói naphthene, aromatic có số C từ 6 - 10. Mô hình ban đầu gồm 53 gói phản ứng được tổng kết trong Bảng 1 [2, 6]. Ở đây chỉ có các phản ứng isomer hóa, dehydro vòng hóa, hydrodealkyl hóa, dehydro hóa và hydrocracking là các phản ứng giảm mạch C hoặc không làm thay đổi số C nên nếu trong nguyên liệu không có các cấu tử C11 thì sẽ không xuất hiện các cấu tử C11 trong sản phẩm.
Để tính toán chính xác hơn thành phần của phân đoạn naphtha và kết quả mô phỏng, các điều chỉnh dưới đây được áp dụng:
2.2.1. Điều chỉnh cơ chế phản ứng tạo benzene
Mô hình ban đầu chỉ có phản ứng: P6 ↔ N6 ↔ A6 không quan tâm đến phản ứng isomer hóa tạo thành cyclohexane (N6) từ methylcyclopentane (MCP) MCP ↔ N6 và không đề cập đến phản ứng tạo thành MCP từ P6, do vậy kết quả mô phỏng thành phần benzene trong reformate không thật chính xác. Hàm lượng benzene trong xăng bị giới hạn do ảnh hưởng xấu đến môi trường và cần được mô phỏng chính xác. Vì vậy, cần bổ sung các phản ứng có mặt benzene với số liệu động học chính xác. Chuỗi phản ứng đầy đủ hơn của benzene được thể hiện trong Hình 2 với giả thuyết benzene được hình thành thông qua phản ứng dehydro hóa của cyclohexane, do có cùng số nguyên tử C(6C) trong khi MCP chỉ có vòng 5 cạnh nên không tham gia phản ứng tạo benzene, MCP sẽ tồn tại trong trạng thái cân bằng với cyclohexane.
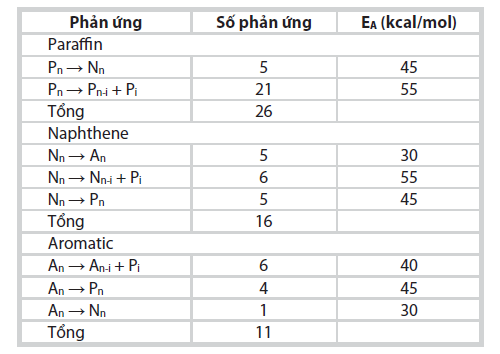 |
Bảng 1. Số phản ứng và năng lượng hoạt hóa trong mô hình Krane |
Ghi chú: n - số nguyên tử C, 1 ≤ i ≤ 6
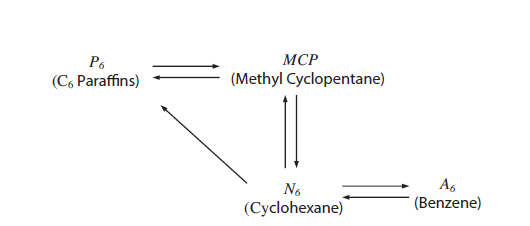 |
Hình 2. Chuỗi phản ứng của benzene |
2.2.2. Phản ứng isomer hóa của các paraffin
Phản ứng isomer hóa n-paraffin thành i-paraffin là phản ứng được mong đợi vì i-paraffin tạo thành góp phần tăng chỉ số octane của reformate. Phản ứng isomer hóa diễn ra với tốc độ nhanh nhờ các tâm xúc tác acid và đạt cân bằng trong điều kiện phản ứng reforming (500oC) [7, 9]. Vì vậy, sự phân bố của paraffin có thể được mô phỏng bằng phản ứng cân bằng.
Phản ứng isomer hóa có dạng như sau: nPi → iPi với hằng số cân bằng (Ke) tính theo công thức: (1)
(1)
Phương trình liên hệ giữa hằng số cân bằng của phản ứng theo nhiệt độ:
(2)
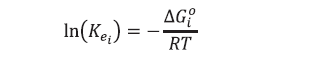
Trong đó, ∆Go là năng lượng tự do Gibbs ở điều kiệntiêu chuẩn, được xác định bằng công thức:
(3)

Để xác định ΔGo, cần xác định sự phụ thuộc của nhiệt dung riêng theo nhiệt độ theo phương trình:
(4)

Thay phương trình (4) vào (3) tính được các tích phân:
(5)
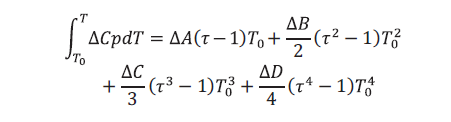
(6)
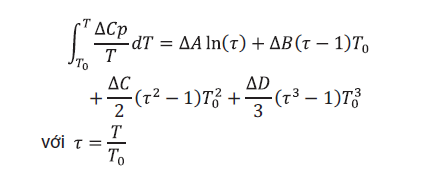
Giá trị của các tham số cần thiết cho việc xác định ∆Go và Ke được lấy từ nghiên cứu của Krane và Miguel A.Rodríguez [2, 6]. Khi xác định được các giá trị Ke của các paraffin có cùng số C, cần xác định liên hệ giữa phần mol của n-paraffin với tổng phần mol của các i-paraffin có cùng số C bằng phương trình:
(7)
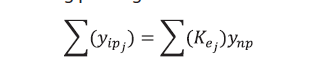
Chia các cấu tử paraffin có cùng số C thành 2 cấu tử giả đại diện cho n-paraffin và i-paraffin, mở rộng số cấu tử giả paraffin cho mô hình và có thể tích hợp thêm các phản ứng isomer hóa.
Phần mol của cấu tử i-paraffin sẽ được xác định như sau:
(8)

Hằng số cân bằng chung của phản ứng nPi → iPi sẽ được xác định bằng phương trình:
(9)

2.2.3. Ảnh hưởng của nhiệt độ và áp suất đến các thông số động học
Trong mô hình ban đầu, Krane không nhắc đến ảnh hưởng của nhiệt độ và áp suất đến các thông số động học. Để khắc phục vấn đề này, phương trình dạng Arrhenius được sử dụng để tìm mối liên hệ giữa hằng số tốc độ với nhiệt độ và áp suất (thông qua thông số ảnh hưởng αk) cho từng phản ứng riêng lẻ. Kết hợp lại có phương trình sau:
(10)
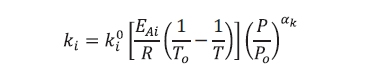
Trong đó, năng lượng hoạt hóa EAi tại Bảng 1, hằng số αk trong Bảng 2. Krane công bố các số liệu động học trong khoảng nhiệt độ 471 - 515oC, áp suất 10,5 kg/cm2 với số liệu hằng số tốc độ duy nhất trong khoảng nhiệt độ này, do đó có thể lấy nhiệt độ gốc cho phương trình (10) là nhiệt độ trung bình của khoảng nhiệt độ To = 493oC.
2.2.4. Đề xuất mô hình động học mở rộng
|
Bảng 2. Thông số ảnh hưởng của áp suất đến tốc độ phản ứng
|
Mô hình động học mới được xây dựng dựa trên mô hình động học của Krane gồm: 10 gói cấu tử cho n-paraffin (C1 - C10), 5 gói cấu tử cho naphthene (C6 - C10), 5 gói cấu tử cho aromatic (C6 - C10), MCP, H2 và 10 gói cấu tử mới được thêm vào đại diện cho i-paraffin. Chuỗi các phản ứng đề xuất được thể hiện trong Hình 3. Các phản ứng được giả thuyết có phương trình tốc độ bậc nhất theo hydrocarbon chính tham gia phản ứng.
Phương trình tốc độ cho dưới dạng [6]:
(11)
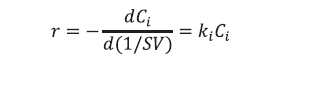
Trong đó:
Ci: Nồng độ phần mol của cấu tử hydrocarbon Ci;
ki: Hằng số tốc độ phản ứng (mol.h-1.(g xúc tác)-1);
SV: Tốc độ không gian nạp liệu (mol.h-1.(g xúc tác)-1).
Phương trình động học này không tính đến ảnh hưởng của các yếu tố nhiệt độ, áp suất, nguyên liệu và ảnh hưởng của xúc tác. Ảnh hưởng của nhiệt độ và áp suất được thể hiện trong công thức (10). Giá trị hằng số tốc độ của 57 phản ứng tại nhiệt độ To = 493oC được công bố trong nghiên cứu của Miguel A. Rodríguez [6].
3. Xây dựng mô phỏng phân xưởng CCR Nhà máy Lọc dầu Dung Quất
3.1. Xây dựng các gói cấu tử
Trong các cấu tử cần cho mô phỏng, có thể sử dụng các cấu tử thật có sẵn trong UniSim là:
- Hydrogen, các n-paraffin: methane, ethane, propane, n-butane, i-butane, n-pentane, n-hexane, n-heptane, n-octane, n-nonane, n-decane
- Naphthene: methylcyclopentane (MCP) - Aromatic: benzene (A6) và toluene (A7).
Ngoài ra, cần phải xây dựng 3 nhóm cấu tử giả sau:
- Các iso-paraffin: IP5, IP6, IP7, IP8, IP9, IP10;
- Các naphthene: N6, N7, N8, N9,N10;
- Các aromatic: A8, A9, A10, A11.
Để tạo cấu tử giả, cần xác định các thông số: nhiệt độ sôi thường (normal boiling point - NBP), khối lượng phân tử (molecular weight - MW) và khối lượng riêng ở điều kiện tiêu chuẩn (Ideal liquid density) [10, 11, 14].
Để có được các thông số trên, cần biết thành phần mol của các cấu tử thật trong một cấu tử giả ở trạng thái cân bằng, tạo một dòng vật chất với thành phần là các cấu tử thật với phần mol tương ứng sẽ xác định được các thông số cho cấu tử giả.
|
Hình 3. Mô hình các phản ứng quá trình reforming naphtha nặng |
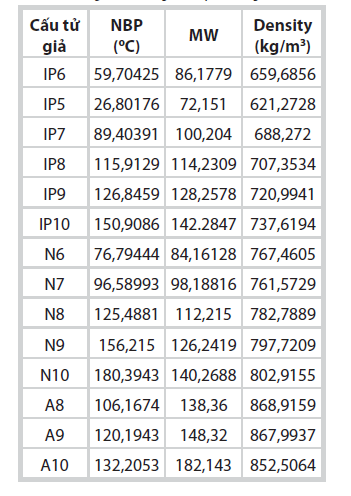 |
Bảng 3. Các thông số để tạo cấu tử giả |
3.2. Xác định giá trị octane number
Để xác định giá trị RON của reformate phải tạo thêm một dòng vật chất rồi sử dụng cơ sở dữ liệu để tính RON. Giá trị RON của các cấu tử được tham khảo từ nghiên cứu trước đó [6, 12] và đường cong octane curve của gói reformer. Với các cấu tử còn lại, giá trị RON được tính dựa theo công thức phụ thuộc cấu trúc phân tử [13]. Sau đó, RON của reformate có thể được xác định một cách gần đúng bằng trung bình cộng theo phần mol của RON các cấu tử thành phần theo công thức:
(12)

3.3. Thiết lập các phản ứng
Phân xưởng có 4 thiết bị phản ứng chính xếp chồng lên nhau với các phản ứng giống nhau, nhưng xảy ra tại các áp suất khác nhau. Do động học của mô hình phụ thuộc vào áp suất, cần phải xây dựng 4 tổ hợp thông số động học phản ứng riêng, áp suất tương ứng cho từng thiết bị phản ứng.
Do trong mô hình động học chỉ có một số liệu động học cho các phản ứng của paraffin không phân biệt n-paraffin và i-paraffin, giả thuyết rằng i-paraffin sẽ phản ứng giống n-paraffin, đây là cơ chế phản ứng ban đầu của Krane. Dòng nguyên liệu trước tiên sẽ được đưa vào thiết bị chuyển hóa toàn bộ i-paraffin thành n-paraffin.
UniSim không thể mô phỏng các phản ứng động học (có đầy đủ các thông số động học) và các phản ứng cân bằng (chỉ có hằng số cân bằng) trong cùng một thiết bị đẩy lý tưởng. Do vậy, chia thành 2 thiết bị phản ứng chính, thiết bị đẩy lý tưởng là nơi diễn ra các phản ứng động học⁄ (trừ phản ứng isomer hóa). Sau đó, dòng sản phẩm được đưa vào thiết bị phản ứng isomer hóa, tại đây các phản ứng cân bằng sẽ đảm bảo cân bằng giữa các n-paraffin và i-paraffin có cùng số C.
Trên cơ sở đó, thiết lập 3 nhóm các phản ứng, chọn đơn vị của cấu tử gốc là phần mol và pha phản ứng là pha hơi, do ở nhiệt độ phản ứng của các cấu tử đều ở dạng hơi.
3.3.1. Các phản ứng chuyển hóa
Thiết lập 7 phản ứng chuyển hóa (cho C4 - C10) với độ chuyển hóa Co = 100% để chuyển hoàn toàn i-paraffin thành n-paraffin.
3.3.2. Các phản ứng động học
Thực hiện theo mô hình động học ban đầu của Krane là chỉ mô phỏng phản ứng của n-paraffin, naphthene,aromatic. Phương trình động học được phần mềm UniSim sử dụng có dạng như sau:
(13)
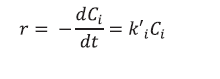
Trong đó:
Ci : Nồng độ phần mol của hydrocarbon Ci;
k’i: Hằng số tốc độ phản ứng (kmol.m-3.s-1).
Hai phương trình (11) và (13) sử dụng 2 hằng số tốc độ khác nhau, vì vậy cần chuyển đổi theo công thức: (14)
Trong đó, ρxt là khối lượng của xúc tác (kg/m3). Với xúc tác R-234 được sử dụng trong Nhà máy Lọc dầu Dung Quất có ρxt = 561kg/m3. Công thức (14) cho giá trị hằng số tốc độ tại nhiệt độ To = 493oC và áp suất Po = 10,5kg/cm2.
Tuy vậy, đây không phải áp suất thực hiện của Nhà máy, cần áp dụng công thức (10) để tính hằng số tốc độ tại áp suất trung bình của thiết bị. Cụ thể, áp suất tại các thiết bị phản ứng như sau:
- Áp suất của thiết bị phản ứng thứ 1: P1 = 4,9kg/cm2
- Áp suất của thiết bị phản ứng thứ 2: P2 = 4,35kg/ cm2.
- Áp suất của thiết bị phản ứng thứ 3: P3 = 3,9kg/cm2.
- Áp suất của thiết bị phản ứng thứ 4: P4 = 3,4kg/cm2.
Khi biết được hằng số tốc độ phản ứng tại nhiệt độ To và năng lượng hoạt hóa EA, có thể tính được tham số A của
phản ứng động học theo phương trình: (15)
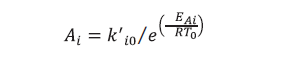
Từ đó, tính toán được các tham số A, EA- kJ/mol cho phương trình động học của các phản ứng cho cả 4 lò phản ứng ở các áp suất tương ứng.
3.3.3. Các phản ứng cân bằng
Các phản ứng cân bằng mô phỏng cho phản ứng isomer hóa của paraffin. Vì ở đây, hằng số cân bằng được tính bằng tổng hằng số cân bằng của nhiều phản ứng nên không thể sử dụng phương pháp nhập một phương trình tính Ke theo nhiệt độ. Ta sử dụng phương pháp nhập bảng quan hệ K - T, chọn khoảng nhiệt độ chứa cả 4 vùng
nhiệt độ làm việc của cả 4 thiết bị phản ứng (400 - 560oC). UniSim sử dụng phương pháp bình phương nhỏ nhất để ước lượng các tham số A, B, C, D cho phương trình liên hệ giữa Ke và T dạng:
(16)
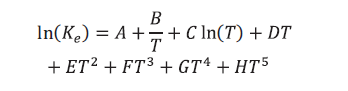
3.4. Xây dựng dòng nguyên liệu tại điều kiện vận hành
Phân xưởng CCR Platforming của Nhà máy Lọc dầu Dung Quất sử dụng dòng đầu vào ở áp suất 10,1kg/cm2, nhiệt độ 118oC lưu lượng 139,8m3/giờ, tỷ lệ mol H2/HC = 3,15, được gia nhiệt lên nhiệt độ 549oC trước khi vào các thiết bị phản ứng. Theo số liệu GC đo từ nguyên liệu Nhà máy Lọc dầu Dung Quất ngày 15/8/2014, từ thành phần khối lượng của các cấu tử tính được thành phần phần mol của các cấu tử theo công thức:
(17)

Thành phần nguyên liệu, có và không có H2 được thể hiện trong Bảng 5.
Nguyên liệu là naphtha nặng đã xử lý tại Phân xưởng xử lý naphtha bằng H2 (NHT) có thành phần chủ yếu là paraffin (53,63% khối lượng) và naphthene (36,11% khối lượng), cùng một lượng nhỏ aromatic, chỉ có các cấu tử C6 - C10, không có các cấu tử C11. Trong mô hình động học không có phản ứng cộng tạo hydrocarbon mạch dài hơn nên để đơn giản, nghiên cứu này loại bỏ các phản ứng lien quan đến cấu tử C11.
3.5. Thiết lập các thiết bị phản ứng
Thực tế thiết bị phản ứng là xuyên tâm, nhưng vì UniSim chỉ cho phép mô phỏng thiết bị phản ứng đẩy lý tưởng với các ống phản ứng. Để gần hơn với thiết kế, nhóm tác giả chọn số ống phản ứng là 1 ống. Kích thước để mô phỏng 4 thiết bị PFR được cho trong Bảng 6.
Để mô phỏng quá trình các phản ứng isomer hóa paraffin, cần thêm thiết bị phản ứng cân bằng. Như vậy, trong mỗi cụm phản ứng có 3 công cụ phản ứng được đặt trong 1 template tương ứng với 3 gói phản ứng đã đề cập trong phần trên. Hình 4 thể hiện sơ đồ các công cụ trong thiết bị phản ứng thứ 1.
3.6. Thiết lập Debutanizer và cụm Recovery Plus System
Debutanizer (T-1301) có chức năng tách phần nhẹ C4 nhằm ổn định chất lượng reformate, các thông số để mô phỏng tháp ổn định lấy theo thiết kế tại Phân xưởng CCR Nhà máy Lọc dầu Dung Quất.
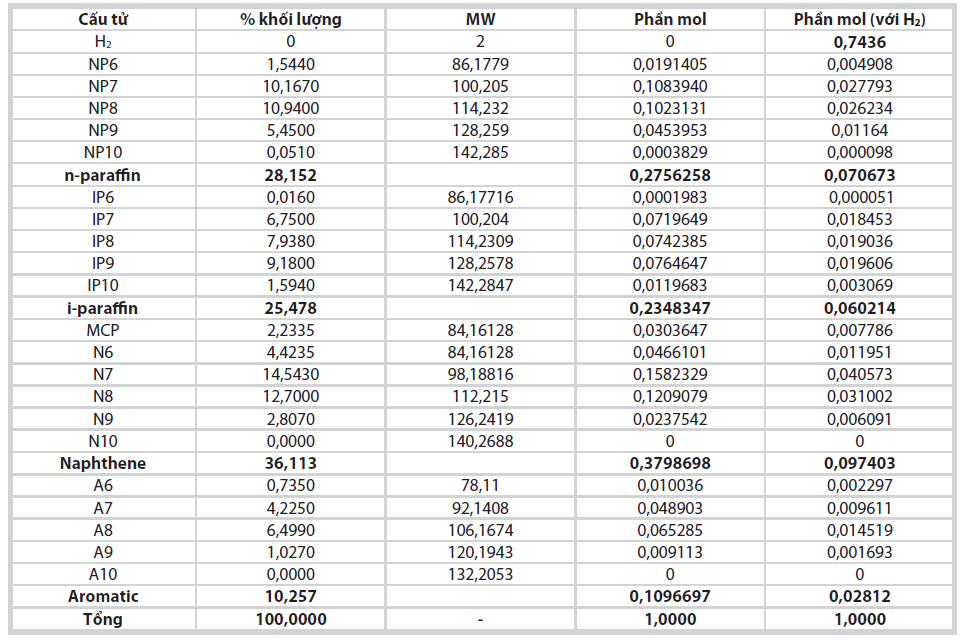 |
Bảng 5. Thành phần cấu tử của dòng nguyên liệu |
 |
Bảng 6. Kích thước sử dụng mô phỏng các thiết bị phản ứng PFR |
Cụm thiết bị Recovery Plus System có tác dụng thu hồi các cấu tử hydrocarbon nặng có ích trong dòng khí đồng thời tăng độ tinh khiết của H2. Quá trình được mô phỏng sử dụng tác nhân lạnh và chu trình lạnh propane. Cụm thiết bị được mô phỏng trong 1 template tại Hình 5.
Sơ đồ mô phỏng của quá trình CCR được thể hiện trong Hình 6.
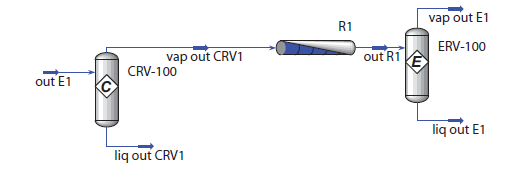 |
Hình 4. Các công cụ phản ứng trong cụm thiết bị phản ứng thứ 1 |
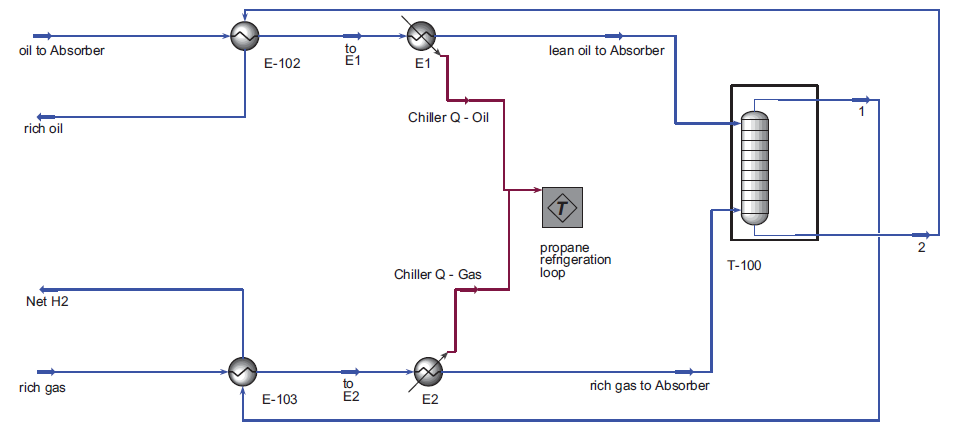 |
Hình 5. Sơ đồ mô phỏng cụm thiết bị Recovery Plus System |
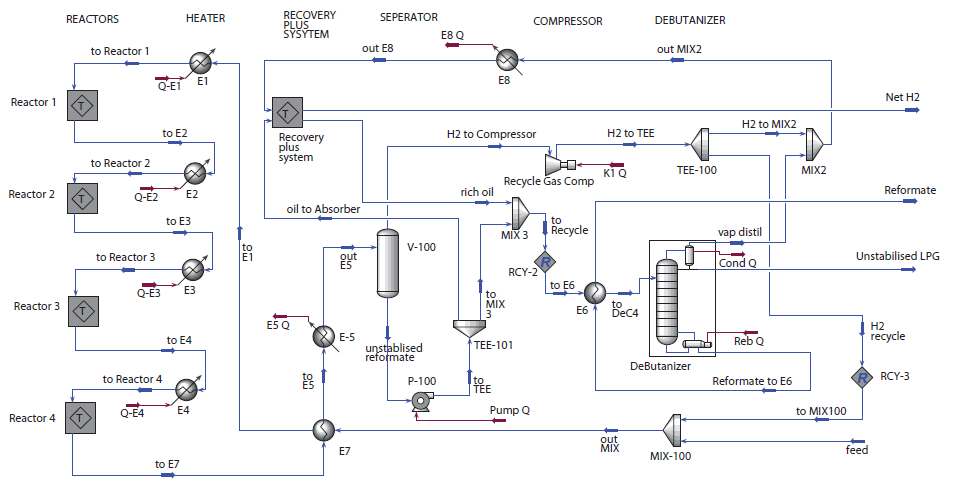 |
Hình 6. Sơ đồ mô phỏng công nghệ CCR |
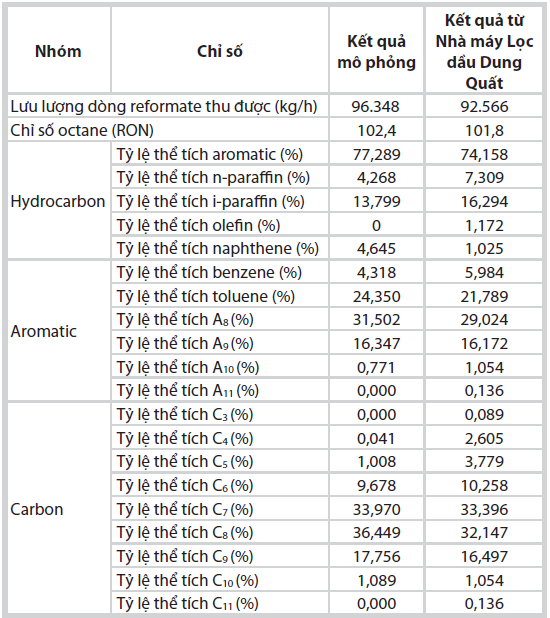 |
Bảng 7. Kết quả reformate từ mô phỏng và Nhà máy Lọc dầu Dung Quất |
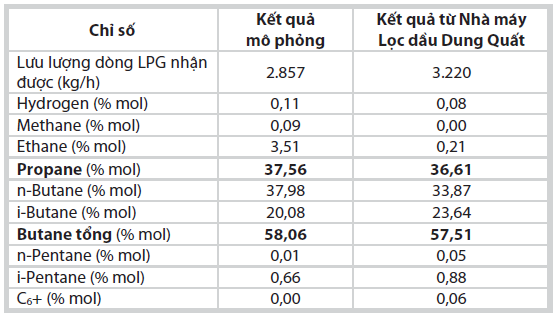 |
Bảng 8. Kết quả dòng LPG từ mô phỏng và Nhà máy Lọc dầu Dung Quất |
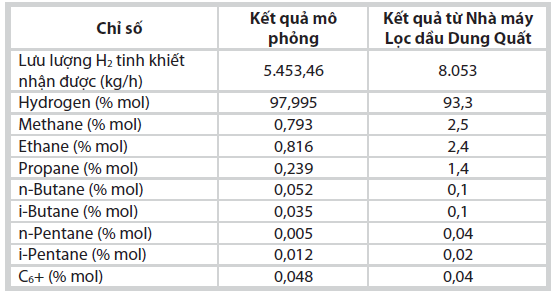 |
Bảng 9. Kết quả H2 tinh khiết từ mô phỏng và Nhà máy Lọc dầu Dung Quất |
4. Kết quả mô phỏng và thảo luận
Quá trình CCR cho 3 dòng sản phẩm chính: xăng reformate, LPG chưa ổn định và dòng khí H2 kỹ thuật có độ tinh khiết cao. Ta sẽ so sánh kết quả mô phỏng với kết quả thực tế tại Nhà máy Lọc dầu Dung Quất.
4.1. Kết quả dòng xăng reformate
Cùng một công suất đầu vào bằng công suất thiết kế là 139,8m3/giờ, dòng reformate thu được do mô phỏng đạt 96.348kg/h và thực tế thu được từ Nhà máy Lọc dầu Dung Quất là 92.566kg/h (thiết kế là 92.224kg/h). Bảng 7 so sánh các thông số giữa dòng xăng reformate thu được do mô phỏng và thực tế tại Nhà máy Lọc dầu Dung Quất.
Kết quả mô phỏng reformate phù hợp với số liệu thực tế thành phần các hydrocarbon thơm tương đối chính xác, chỉ số octane của reformate mô phỏng là 102,43 so với thực tế là 101,8.
4.2. Kết quả dòng LPG chưa ổn định
Kết quả dòng LPG chưa ổn định từ kết quả mô phỏng sát với dữ liệu thực tế sản xuất tại Nhà máy Lọc dầu Dung Quất (Bảng 8), đặc biệt hàm lượng tổng của 2 thành phần chính của LPG là propane và butane, giá trị sai lệch dưới 0,1%.
4.3. Kết quả dòng H2 kỹ thuật
Kết quả dòng H2 nhận được từ mô phỏng với dữ liệu từ Nhà máy Lọc dầu Dung Quất (Bảng 9). Dòng H2 đạt yêu cầu về hàm lượng H2 và hydrocarbon nhẹ, lượng C6+ sai lệch không đáng kể.
4.4. Cân bằng vật chất và cân bằng nănglượng
Số liệu cân bằng vật chất giữa dòng vào và dòng ra với sai số %ΔG = 0,38% (Bảng 10) ở mức chấp nhận được.
Theo Bảng 11, cân bằng năng lượng với sai số tính được là -0,02% ở mức chấp nhận được.
4.5. Khảo sát các thông số theo lưu trình các thiết bị
4.5.1. Khảo sát sự thay đổi nhiệt độ
Tỷ lệ phân bố xúc tác của phân xưởng CCR Platforming Nhà máy Lọc dầu Dung Quất được thể hiện trong Bảng 12.
Trong Hình 7, mức độ giảm nhiệt độ giảm dần qua các thiết bị phản ứng. Thiết bị phản ứng thứ 1 xảy ra các phản ứng thu nhiệt mạnh và nhanh (phản ứng dehydro naphthene thành aromatic) nên nhiệt độ giảm mạnh ∆T1 = 83,7oC. Tại thiết bị phản ứng thứ 2 tiếp tục diễn ra các phản ứng thu nhiệt (dehydro hóa naphthene và dehydro hóa đóng vòng paraffin), độ giảm nhiệt độ nhỏ hơn ∆T2 = 32,2oC. Tại thiết bị phản ứng thứ 3 và thứ 4, nồng độ naphthene giảm, phản ứng thu nhiệt xảy ra chậm hơn, các phản ứng hydrocracking tỏa nhiệt nên độ giảm nhiệt độ thấp hơn ∆T3 = 23,3oC và ∆T4 = 11,9oC.
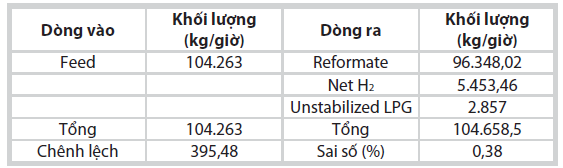 |
Bảng 10. Cân bằng vật chất |
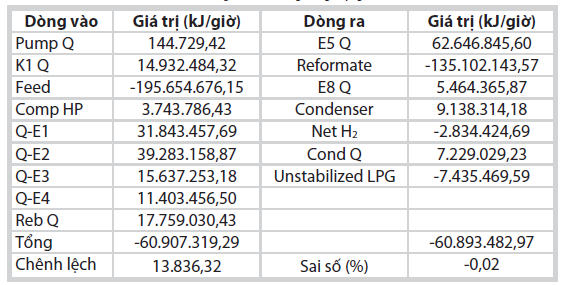 |
Bảng 11. Cân bằng năng lượng |
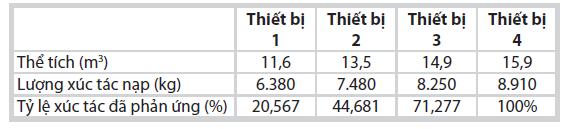 |
Bảng 12. Phân bố xúc tác tại các thiết bị phản ứng |
4.5.2. Khảo sát sự thay đổi thành phần các cấu tử
Hình 8 thể hiện sự thay đổi nồng độ các thành phần paraffin - naphthene – aromatic trong hỗn hợp theo khối lượng xúc tác đi qua.
Ở 2 thiết bị phản ứng thứ 1 và 2, phản ứngdehydro hóa mạnh nên nồng độ naphthene giảm mạnh từ 34,754% xuống 7,628%, nồng độ aromatic tăng nhanh từ 8,721% lên 45,66%. Sang thiết bị phản ứng thứ 3, nồng độ naphthene thấp nên tốc độ phản ứng dehydro hóa giảm, nồng độ aromatictăng chậm trong thiết bị phản ứng thứ 3 và 4. Tại thiết bị phản ứng thứ 4, phản ứng hydrocracking xảy ra tăng, làm tăng số mol paraffin tạo thành, do đó thành phần paraffin chỉ giảm nhẹ.
Hình 9 cho thấy theo lượng xúc tác tăng thành phần H2 tăng do các phản ứng chính sinh H2. Trong khi phần mol hydrocarbon nặng giảm và phần mol hydrocarbon nhẹ tăng nhẹ.
4.6. Khảo sát ảnh hưởng của các thông số đến quá trình công nghệ
4.6.1. Ảnh hưởng của nhiệt độ đến quá trình công nghệ
Khi nhiệt độ tăng thúc đẩy các phản ứng hydrocracking làm lượng reformate giảm, % Khối lượng xúc tác Hình 7. Sự thay đổi nhiệt độ trong thiết bị phản ứng trong khi lượng H2 tinh khiết và LPG tăng.
Khi nhiệt độ phản ứng tăng hàm lượng aromatic và RON tăng, làm tăng chất lượng của reformate (Hình 11). Từ nhiệt độ khoảng 540oC thì reformate đạt chỉ tiêu RON ≥ 102 theo thiết kế.
Khi nhiệt độ tăng, phản ứng hydrocracking tỏa nhiệt xảy ra mạnh hơn làm giảm độ giảm nhiệt độ, hàm lượng aromatic trong reformate tăng khi nhiệt độ tăng. Khi nhiệt độ phản ứng tăng cao hơn 550oC thì độ giảm nhiệt độ và độ tăng hàm lượng aromatic có xu hướng chậm lại.
 |
Hình 8. Sự thay đổi thành phần các hydrocarbon trong thiết bị phản ứng |
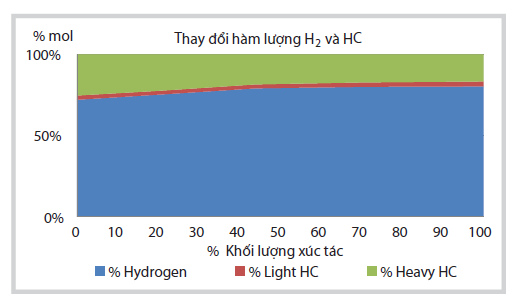 |
Hình 9. Sự thay đổi thành phần H2 và hydrocarbon trong thiết bị phản ứng |
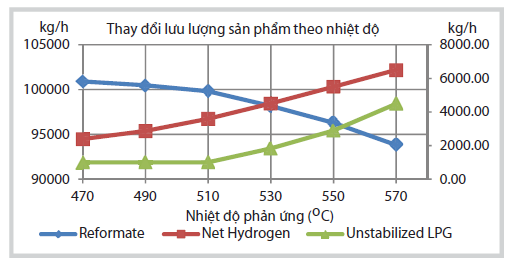 |
Hình 10. Sự thay đổi lưu lượng sản phẩm theo nhiệt độ đầu vào |
Nhìn chung, chất lượng và sản lượng reformate thay đổi ngược chiều nhau, vì vậy cần chọn nhiệt độ vận hành thích hợp đảm bảo chỉ số octane đáp ứng yêu cầu, song tránh việc tạo cốc khi tăng nhiệt độ. Dựa vào các phân tích trên thì nhiệt độ tối ưu dao động trong khoảng 540 - 555oC.
4.6.2. Ảnh hưởng của áp suất đến quá trình công nghệ
Các phản ứng chính của reforming xúc tác là các phản ứng tăng thể tích (dehydro hóa naphthene, dehydro hóa đóng vòng paraffin thành aromatic). Vì vậy, theo quan điểm nhiệt động học áp suất tăng sẽ cản trở quá trình tăng thể tích, có nghĩa là cản trở các phản ứng chính tạo aromatic của reforming xúc tác.
Do đó, làm giảm chất lượng của sản phẩm, điều này phù hợp khi tiến hành kiểm tra mô hình mô phỏng trên Hình 13, khi tăng áp suất hàm lượng aromatic giảm nên chỉ số RON giảm.
Khi tăng áp suất, độ giảm nhiệt độ của các thiết bị phản ứng ít đi, thể hiện các phản ứng thu nhiệt có ích xảy ra chậm hơn khi tăng áp suất, hàm lượng paraffin tăng và aromatic giảm (do phản ứng dehydro hóa naphthene bị cản trở). Vì vậy, nên lựa chọn áp suất trong khoảng 5 - 6kg/cm2 (phù hợp với nhận xét trên và áp suất thiết kế hệ thống).
4.6.3. Ảnh hưởng của tốc độ nạp liệu thể tích (LHSV) đến quá trình công nghệ
Để khảo sát ảnh hưởng của tốc độ nạp liệu thể tích, cần cố định nhiệt độ và áp suất phản ứng. Khi tăng tốc độ nạp liệu sẽ làm giảm thời gian tiếp xúc của nguyên liệu với xúc tác hay nói cách khác làm giảm thời gian phản ứng.
 |
Hình 11. Sự thay đổi chất lượng reformate theo nhiệt độ phản ứng |
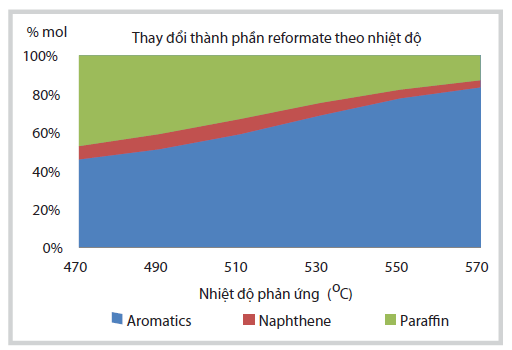 |
Hình 12. Thành phần hydrocarbon sau phản ứng khi nhiệt độ thay đổi |
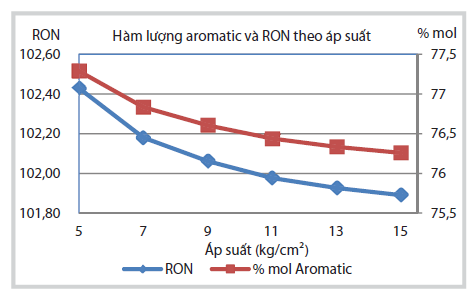 |
Hình 13. Sự thay đổi chất lượng reformate khi áp suất thay đổi |
|
Hình 14. Sự thay đổi lượng sản phẩm theo tốc độ nạp liệu thể tích |
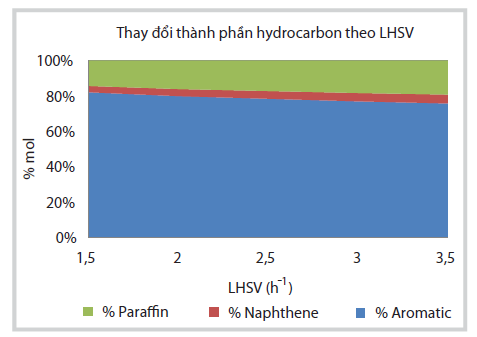 |
Hình 15. Sự thay đổi thành phần hydrocabon theo tốc độ nạp liệu thể tích
|
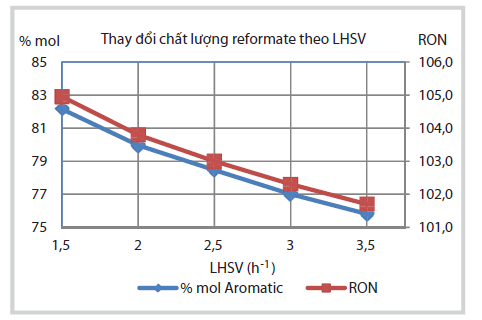 |
Hình 16. Sự thay đổi chất lượng reformate theo tốc độ nạp liệu thể tích |
|
Hình 17. Sự thay đổi độ giảm nhiệt độ theo tốc độ nạp liệu thể tích |
Khi tốc độ nạp liệu thể tích tăng thì lưu lượng các dòng sản phẩm đều tăng lên, do công suất tăng (nguyên liệu đầu vào tăng lên thì sản phẩm đầu ra cũng tăng theo), nhưng đồng thời giảm chất lượng của xăng (Hình 15). Khi tốc độ nạp liệu thể tích tăng, hàm lượng aromatic giảm, naphthene tăng nhẹ và paraffin tăng. Nguyên nhân do thời gian phản ứng giảm dẫn đến quá trình chuyển hóa thành sản phẩm chính aromatic giảm (nguyên liệu chưa được chuyển hóa triệt để) vì vậy hàm lượng paraffin tăng còn aromatic sẽ giảm xuống.
Hình 16 cho thấy RON giảm mạnh từ 105 xuống còn 101,7 khi tốc độ nạp liệu tăng từ 1,5 lên 3,5. Khi tăng tốc độ nạp liệu thể tích > 3,0h-1 thì RON của dòng xăng reformate giảm xuống không đạt được giá trị >102 theo yêu cầu. Vì vậy, tại áp suất và nhiệt độ khảo sát cần duy trì tốc độ nạp liệu thể tích ≤ 3,0h-1.
Trong Hình 17, khi tăng giá trị của tốc độ nạp liệu thể tích thì độ giảm nhiệt độ của các thiết bị phản ứng tăng lên, dẫn đến tổng ΔT trong cả 4 thiết bị phản ứng tăng theo. Điều này chứng tỏ các phản ứng có lợi vẫn tiếp tục xảy ra trong các thiết bị phản ứng sau vì chưa phản ứng hết ở các thiết bị đầu do tốc độ nạp liệu cao. Tuy nhiên, cần duy trì tốc độ nạp liệu thể tích để reformate có RON ≥ 102. Vì vậy, giá trị tốc độ nạp liệu thể tích cần nằm trong khoảng 2,5 - 3,0h-1 và càng gần 3,0h-1 càng tốt (vì khi đó sản phẩm vẫn đạt RON mà sản lượng là cao nhất).
4.6.4. Ảnh hưởng tỷ lệ H2/HC đến quá trình công nghệ
Để xét sự ảnh hưởng của tỷ lệ H2/HC cố định giá trị tốc độ nạp liệu thể tích = 2,891h-1 theo đúng thông số thiết kế của phân xưởng CCR Platforming Nhà máy Lọc dầu Dung Quất để tiến hành khảo sát.
Khi tăng tỷ lệ H2/HC (Hình 18), hàm lượng của paraffin trong reformate tăng, hàm lượng naphthene không thay đổi nhiều và hàm lượng aromatic giảm. Khi tăng tỷ lệ H2/ HC làm tăng phản ứng hydrocracking tạo nhiều paraffin hơn. H2/HC tăng gây ức chế phản ứng tạo aromatic do đó hàm lượng của aromatic trong reformate giảm.Khi tỷ lệ H2/HC tăng lưu lượng dòng reformate tăng nhẹ (Hình 19) nhưng chất lượng dòng reformate giảm xuống rõ rệt (Hình 20). Để đảm bảo RON ≥ 102, cần lựa chọn tỷ lệ H2/HC trong khoảng từ 3,0 - 3,5 sẽ đảm bảo cả về lượng và chất của dòng reformate.
4.7. Tối ưu hóa các thông số công nghệ
4.7.1. Tối ưu hóa công nghệ để tăng sản lượng xăng reformate
Hình 15. Sự thay đổi thành phần hydrocarbon theo tốc độ nạp liệu thể tích
Nghiên cứu đã mô phỏng thành công phân xưởng CCR Platforming của Nhà máy Lọc dầu Dung Quất tại 100% công suất thiết kế. Kết quả cho thấy tại công suất đầu vào bằng công suất thiết kế là 139,8m3/h, với dòng nguyên liệu đầu vào có khối lượng 104.262,8kg/h, tốc độ nạp liệu thể tích LHSV = 2,891h-1; tỷ lệ H2/HC = 3,15, dòng reformate đầu ra thu được 96.348kg/h có RON = 102. Dòng reformate thu được từ Nhà máy Lọc dầu Dung Quất là 92.566kg/h có RON = 101,8 trong khi thiết kế là 92.224kg/h và RON = 102.
Để tối ưu lượng reformate mà vẫn đạt RON ≥ 102 như yêu cầu thiết kế, sử dụng công cụ Optimiser để tìm điều kiện tối ưu sao cho lượng reformate thu được là lớn nhất.
Nhập 3 biến công nghệ có thể thay đổi là: tốc độ nạp liệu thể tích, nhiệt độ đầu vào (trong khoảng 540 - 555oC) và tỷ lệ H2/HC. Sử dụng 2 chỉ tiêu chất lượng của sản phẩm cần khống chế là RON của reformate ≥ 102, hàm lượng H2 trong dòng net H2 ≥ 0,933.
Kết quả tối ưu cho thấy khi thay đổi tốc độ nạp liệu thể tích, nhiệt độ, tỷ lệ H2/HC để thu được dòng reformate tối ưu có lưu lượng 107.399kg/h tại RON = 102 với LHSV = 3,217 (h-1) và H2/HC = 2,771 tại nhiệt độ phản ứng là T = 547,2oC.
4.7.2. Tối ưu hóa năng lượng của phân xưởng
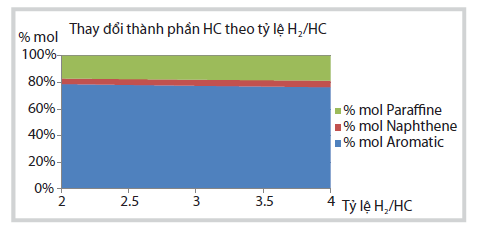 |
Hình 18. Sự thay đổi thành phần reformate theo tỷ lệ H2/HC
|
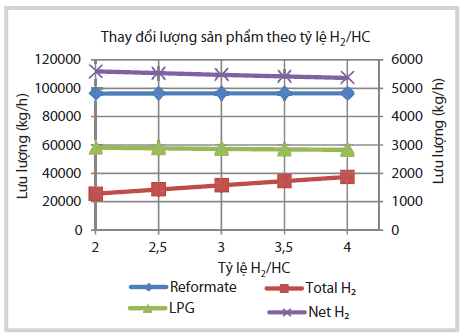 |
Hình 19. Sự thay đổi lưu lượng sản phẩm theo tỷ lệ H2/HC |
|
Hình 20. Sự thay đổi chất lượng reformate theo tỷ lệ H2/HC |
Tối ưu hóa năng lượng là mục tiêu rất quan trọng trong quá trình vận hành, góp phần trực tiếp giảm năng lượng tiêu thụ, tiết giảm chi phí sản xuất, tăng lợi nhuận. Để tiến hành tối ưu hóa năng lượng của phân xưởng, nhóm tác giả xem xét khả năng tối ưu hóa năng lượng các lò gia nhiệt. Sử dụng dòng optimizer stream để tính toán năng lượng, thông số nhiệt (heat flow) theo công thức:

Trong đó, QE1, QE2, QE3, QE4 là dòng năng lượng cung cấp từ 4 lò gia nhiệt cho 4 dòng nguyên liệu vào 4 thiết bị phản ứng (kJ/giờ).
Khi nhà máy dư thừa RON trong xăng thương phẩm thì có thể tiến hành giảm công suất xuống LHSV = 1,734h-1 để tiết kiệm chi phí vận hành thông qua tiết kiệm năng lượng.
|
Bảng 13. Tối ưu sản lượng xăng reformate |
 |
Bảng 14. Tối ưu hóa tiêu thụ năng lượng |
5. Kết luận
Nghiên cứu đã mô phỏng thành công các thiết bịchính của phân xưởng CCR Platforming dựa trên mô hình động học được phát triển một cách logic và khoa học.
Kết quả mô phỏng phù hợp với dữ liệu thu được từ phân xưởng CCR Platforming Nhà máy Lọc dầu Dung Quất. Đây là cơ sở để tiến hành mô phỏng hóa toàn bộ phân xưởng CCR Platforming bao gồm cả phần tái sinh xúc tác, từ đó tiến hành tối ưu hoạt động của phân xưởng này và góp phần nâng cao hiệu quả sản xuất cho Nhà máy Lọc dầu Dung Quất.
Tài liệu tham khảo
1. Phạm Thanh Huyền, Nguyễn Hồng Liên. Công nghệ tổng hợp hữu cơ - Hóa dầu. Nhà xuất bản Khoa học và Kỹ thuật. 2006.
2. H.G.Krane, A.B.Groh, B.L.Schulman, J.H.Sinfelt. Reactions in catalytic reforming of naphthas. 5th World Petroleum Congress, New York, USA. 30 May - 5 June 1959.
3. RB.Smith. Kinetic analysis of naphtha reforming with platinum catalyst. Chemical Engineering Progress. 1959; 55(6): p. 76 - 80.
4. J.Henningsen, M.Bundgaard-Nielson. Catalytic reforming. British Chemical Engineering. 1970; 15: p. 1433 - 1436.
5. Michael P.Ramage, Kenneth R.Graziani, F.J.Krambeck. Development of mobil’s kinetic reforming model. Chemical Engineering Science. 1980; 15(1 - 2): p. 41 - 48.
6. Miguel A.Rodríguez, Jorge Ancheyta. Detailed description of kinetic and reactor modeling for naphtha catalytic reforming. Fuel. 2011; 90(12): p. 3492 - 3508.
7. Vietnam Oil and Gas Group. Dung Quat Refinery operating manual – continuous catalytic reformer unit. Technip. 2007.
8. Univesal Oil Products. CCR Platforming – General operating manual. UOP LLC. 2002.
9. George J.Antos, Abdullah M.Aitani. Catalytic naphtha reforming. CRC Press. 2004.
10. Nguyễn Thị Minh Hiền. Mô phỏng các quá trình cơ bản trong công nghệ hóa học. Nhà xuất bản Bách khoa – Hà Nội. 2014.
11. D.S.Jones. Elements petroleum processing. Wiley and Sons. 1995; 9: p. 181 - 186.
12. Anton Perdih, Franc Perdih. Chemical interpretation of octane number. Acta Chim. Slov. 2006; 53: p. 306 - 315.
13. Tareq A.Albahri. Structural group contribution method for predicting the octane number of pure hydrocarbon liquids. Industrial & Engineering Chemistry Research. 2003; 42(3): p. 657 - 662.
14. Yongyou Hu, Hongye Su, Jian Chu. Modeling, simulation and optimization of commercial naphtha catalytic reforming process. Proceedings of the 42nd IEEE Conference on Decision and Control, Hawaii, US. 2003: p. 6206 - 6211.
Model simulation and optimisation for CCR platforming unit of Dung Quat refinery
Nguyen Duy Thang - VietNam Oil and Gas Group
Nguyen Thi Minh Hien; Nguyen Phu Huy - Hanoi University of Science anh Technology
Summary
To improve efficiency and competitiveness, refineries need to optimise their operations to reduce production costs through crude oil selection and blending, definition of product structure, and energy saving, etc. The optimisa- tion process can be conducted from unit level to the entire plant and supported by the simulation softwares. However, normally these models are "packages" which are software’s built-in or modelling by consultants and almost impos- sible to intervene directly in the thermodynamic mechanism of the process.
The CCR model (Refsim) currently used for the CCR Platforming unit of Dung Quat Refinery is built by KBC based on PetroSim software. This model, however, does not allow the engineers to conduct kinetic adjustment for optimisa- tion. In this study, model simulation for the CCR Platforming unit in Dung Quat refinery has been built based on the expansion and adjustment of Krane kinetic model. After verification with real operation results, the simulation model will be used to predict the parameters of the process and evaluate the potential to optimise the operating conditions of the CCR Platforming unit in Dung Quat refinery.
Key words: Catalytic reforming, kinetic model, optimisation, Dung Quat Refinery.