Nghiên cứu này giới thiệu thiết kế ban đầu bộ giảm xóc khoan, được thực hiện trên cơ sở xây dựng mô hình số có kiểm chứng trên vỏ bộ giảm xóc có vết cắt và sử dụng các thuật toán để giải quyết các vấn đề được sử dụng có tính đến ma sát ở các bề mặt tiếp xúc. Nhóm tác giả đã phân tích tổng thể trạng thái ứng suất - biến dạng của các phần tử đàn hồi trong bộ giảm xóc khoan; sử dụng các tiêu chuẩn năng lượng để ước tính độ bền kết cấu; các vòng từ trễ được xây dựng và phân tích đối với nhiều chu kỳ tải của các phần tử đàn hồi. Kết quả nghiên cứu cho phép đánh giá tác động của các đặc tính đàn hồi của vật liệu vỏ và chất độn, các thông số hình học và các tính chất ma sát trên các thông số vận hành. Điều này cho phép sử dụng hiệu quả hơn thiết bị khoan, cải thiện thiết kế vỏ bộ đàn hồi tuân thủ tối đa tiêu chí và mức độ yêu cầu của giảm xóc để tạo tiền đề phát triển các phương pháp kỹ thuật và thiết kế mới cho hệ thống chống xóc trong khoan.
Từ khóa: Vật thể đàn hồi, vỏ, bộ khoan giảm xóc, bộ phận giảm xóc, chống rung.
1. Giới thiệu
Quá trình khoan giếng dầu và khí đốt gắn liền với sự xuất hiện đáng kể sự rung động của các công cụ khoan, làm giảm các thông số kỹ thuật - kinh tế khoan, ảnh hưởng xấu đến hiệu suất làm việc của choòng khoan, bộ cần khoan, động cơ ngoài và thiết bị mặt đất... [1 - 5]. Khi khoan giếng trong điều kiện cường độ rung cao làm giảm các chỉ tiêu kinh tế - kỹ thuật của choòng khoan chóp xoay và choòng kim cương, làm giảm công suất có ích của động cơ, làm xấu đi quá trình phá hủy đá, tăng chi phí năng lượng riêng để khoan, tăng tai nạn. Trong khi khoan ở chiều sâu nông, thông thường, bằng trực quan có thể quan sát được các dao động cần khoan. Với sự gia tăng chiều sâu giếng, cột cần khoan có thể không biểu hiện rõ ràng rung động trên bề mặt. Dao động tải trong quá trình khoan đá cứng có tác động đáng kể đến sự biến dạng quỹ đạo giếng khoan [4, 5]. Do đó, nghiên cứu cách thức để giảm tác hại của sự rung động trong lĩnh vực khoan là nhiệm vụ cấp bách.
Một trong những giải pháp có triển vọng và cơ bản nhất cho giảm tác hại của sự rung động là dựa trên việc sử dụng các thiết bị chống rung đặc biệt như: khớp nối đàn hồi, bộ giảm xóc, giảm chấn khoan, trục đàn hồi động cơ, giảm động năng... [6 - 9]. Hiện nay, trên thị trường thế giới có nhiều nhà sản xuất và nhà cung cấp các thiết bị khoan nổi tiếng trong đó có bộ giảm xóc [10 - 13], chứng tỏ bảo vệ thiết bị giảm xóc là một phần không thể thiếu của phức hợp thiết bị kỹ thuật cần thiết để tiến hành các hoạt động khoan, nhất là trong điều kiện phức tạp. Nguyên tắc của thiết bị đề xuất để triệt tiêu rung cột cần khoan của các nhà sản xuất là khác nhau. Đặc biệt, Toro Downhole Tools (Mỹ) sản xuất vật liệu hấp thụ thủy lực khoan giảm xóc Shock Subs SH và JA Oilfield Manufacturing Inc. cung cấp Shock Sub System [10, 13]. Nhà sản xuất Thụy Sĩ Weatherford International Ltd. cung cấp giảm xóc cao su - kim loại Dailey R-A-M. Được công nhận là công ty chuyên sản xuất và bảo dưỡng động cơ hàng đầu thế giới, BICO Drilling Tools sản xuất bộ giảm xóc Shock-EZE. Các công ty Trung Quốc Secoroc Rock Drilling Tools và Jereh Drilltech cung cấp bộ giảm xóc đơn và đôi hoạt động trên cơ sở các thành phần dầu hoặc cao su đàn hồi [11]. Nhà sản xuất Nga ВНИИБТ - Буровой инструмент sản xuất bộ giảm xóc kiểu hấp thụ xóc gần AN1 trên cơ sở các phần tử kim loại đàn hồi [12]. Sự đa dạng của các giải pháp kỹ thuật cho thấy việc sử dụng các phần tử giảm xóc với cơ chế đàn hồi truyền thống trong khoan không phải luôn đáp ứng được yêu cầu trong điều kiện giàn khoan hoạt động khó khăn (tải trọng tĩnh và động cao trong khi hạn chế về đường kính của bộ dụng cụ khoan). Rõ ràng, việc lựa chọn tối ưu và hợp lý các phần tử đàn hồi trong thiết kế bộ dụng cụ khoan nhằm triệt tiêu rung không phải là giải pháp cuối cùng.
Trong nghiên cứu này, nhóm tác giả tập trung đánh giá hiệu quả thiết kế các phần tử đàn hồi trong giảm xóc khoan, có thể làm việc trong điều kiện giếng khoan phức tạp; đề xuất một phương pháp đánh giá các đặc tính kỹ thuật cơ bản (độ cứng, sức bền và các thuộc tính giảm xóc) của các phần tử đàn hồi.
2. Bộ giảm xóc khoan được thiết kế dựa trên cơ sở các thành phần hệ vỏ đàn hồi
Yêu cầu cơ bản của hệ thống chống rung hiện đại bao gồm kích thước và trọng lượng tối thiểu, sự ổn định của tính chống rung, công nghệ sản xuất, độ tin cậy khi hoạt động và chi phí thấp. Ngoài ra, thiết kế các phần tử đàn hồi thực sự của bộ giảm xóc khoan cần phải chịu được tải cực cao, để kết hợp tải trọng thiết kế cao với độ cứng tương đối thấp và mức độ giảm xóc cần thiết đủ để chống rung hiệu quả. Để giải quyết các vấn đề đặt ra, nhóm tác giả đề xuất ý tưởng sử dụng một vỏ hình trụ với vết cắt dọc theo đường sinh như thanh dẫn chính truyền tải và điều hành từ các phần tử đàn hồi. Hoạt động này theo kết cấu thanh dẫn truyền tải dị hướng (cứng theo hướng trục và dẻo theo hướng tiếp tuyến) đã tạo ra điều kiện sử dụng các đường cong vỏ trong điều kiện gần mặt biến dạng, cho phép các khâu thiết kế thi công thay đổi các thuộc tính độ cứng và độ bền của các phần tử đàn hồi trong phạm vi rộng.
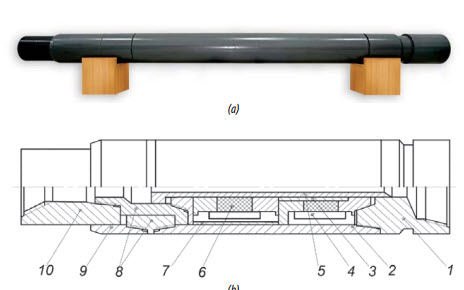 |
1.Bộ chuyển đổi; 2. Giá đỡ; 3. Ống lót ổ trục; 4. Phần tử đàn hồi bậc một; 5. Thân trụ; 6. Phần tử đàn hồi bậc hai; 7. Ống lót bao gồm các phần tử đàn hồi bậc một; 8. Cặp biên dạng truyền moment xoắn; 9. Ống nối; 10. Đầu nối chuyển tiếp ren. |
Hình 1. Bộ giảm xóc khoan được thiết kế dựa trên vỏ vật liệu đàn hồi: Mô hình chung (a); Sơ đồ cơ bản của vỏ bộ giảm xóc (b)
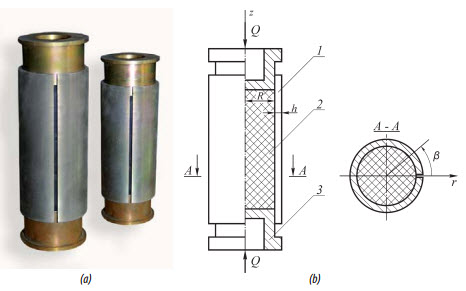 |
1. Vỏ hình trụ với vết cắt; 2. Chất độn đàn hồi của vỏ; 3. Piston truyền tải |
Hình 2. Vỏ vật liệu đàn hồi với vết cắt dọc theo đường sinh. Mô hình thực tế (a); Sơ đồ cơ bản (b)
Hình 1 miêu tả mô hình chung và sơ đồ cơ bản mô hình ban đầu của bộ giảm xóc khoan được trang bị bằng các phần tử đàn hồi. Thanh chịu tải chính các phần tử đàn hồi của bộ giảm xóc này là một vỏ hình trụ với vết cắt dọc theo đường sinh. Các tính năng được trình bày trong mô hình với các thanh đàn hồi giảm xóc hoạt động song song (trong hình vẽ cho thấy chỉ có 2 mức độ phần tử đàn hồi). Nguyên lý hoạt động của bộ giảm xóc: Dưới tác động của áp lực bên ngoài trục bộ phận chuyển động của bộ giảm xóc đi vào phạm vi giá đỡ. Trong giai đoạn này các phần tử đàn hồi bậc 1 và bậc 2 tích lũy năng lượng đàn hồi. Khi áp lực bên ngoài giảm, các phần tử đàn hồi với năng lượng đã được tích lũy chuyển hóa thành phần chuyển động của bộ giảm xóc về vị trí ban đầu. Nhờ sự góp mặt của các ống lót thân trụ và ống lót của các phần tử đàn hồi bậc một của bộ phận đàn hồi bao gồm trong các hoạt động song song, mỗi phần mang một phần của áp lực bên ngoài, tỷ lệ thuận với độ cứng riêng của nó. Nếu cần thiết, nó có thể thiết lập một số lượng lớn các công đoạn đó cùng một lúc hoặc liên tục (với sự gia tăng áp lực bên ngoài) bao gồm trong các hoạt động song song.
Trên cơ sở đó, nhóm tác giả thiết kế bộ giảm xóc, xem xét chi tiết hơn về các tính năng của liên kết đàn hồi. Hình 2 thể hiện mô hình chung và sơ đồ của các bộ phận vỏ đàn hồi. Các tính năng đặc biệt của mô hình này là sự hiện diện của vết cắt trên vỏ dọc theo đường sinh, giúp làm giảm độ cứng của vỏ đàn hồi mà không ảnh hưởng đến đặc tính chống rung. Các thiết kế của vỏ đàn hồi (Hình 2b). Dưới tác dụng của tải dọc trục, piston truyền tải và nén các chất độn đàn hồi của vỏ. Khi giảm tải dọc trục, dưới tác động đàn hồi, hệ thống trả về vị trí ban đầu. Đóng góp chính vào độ dẻo của hệ thống làm thay đổi hình dạng chất độn bằng cách uốn cong biến dạng vết cắt vỏ.
Dưới chu kỳ tải của vỏ đàn hồi, ma sát ảnh hưởng qua lại, chất độn và vỏ, năng lượng cung cấp cho hệ thống tiêu biến, chủ yếu là do cấu trúc hiện tượng trễ [14, 15].
3. Mô hình phần tử hữu hạn của vỏ vật liệu đàn hồi
Trong điều kiện cơ học, đề xuất vật liệu đàn hồi cho hệ thống vỏ biến dạng có ma sát khô. Mô hình hoạt động cơ - toán học của vỏ đàn hồi trong điều kiện tải đơn điệu, xây dựng bài toán phi tuyến không bảo toàn tiếp xúc hỗn hợp về tương tác ma sát vỏ mỏng với chất độn đàn hồi. Để giải quyết vấn đề này, nhóm tác giả sử dụng phương pháp số phần tử hữu hạn, kiểm chứng tương tác tiếp xúc vết cắt vỏ với thân đàn hồi bằng cách so sánh số lượng kết quả thu được từ phương pháp số với kết quả nghiên cứu thực nghiệm các mẫu vật [16, 17].
Bước quan trọng của xây dựng mô hình phần tử hữu hạn là lựa chọn loại phần tử hữu hạn và thiết kế quy trình phân chia các phần tử. Trong nghiên cứu này nhóm tác giả sử dụng phần tử lục giác và bát giác với hàm tuyến tính. Sự tiếp xúc vật thể (vỏ và chất độn) được trình bày như các mảng riêng biệt các phần tử hữu hạn với số lượng xác định trong phạm vi tiếp xúc. Từ đó, mô hình tiếp xúc được thực hiện theo tỷ lệ sau:
(1)
Phương trình đầu tiên của hệ phương trình (1) mô tả ma sát theo định luật Coulomb. Bất phương trình thứ hai là điều kiện tiếp xúc hình học giữa 2 vật thể (ký hiệu là A và B). Trong đó:
F , F : Lực tiếp tuyến và lực pháp tuyến;
μ: Hệ số ma sát giữa vỏ và chất độn.
u: Phạm vi dịch chuyển vật thể A;
n: Vector giới hạn trung bình vật thể B;
d, d : Số điểm tiếp xúc và hệ số kỹ thuật tiếp xúc.
Cụ thể ở phương trình đầu tiên các thành phần trong tải tiếp xúc khi
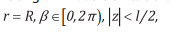
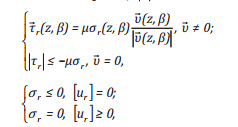
Trong đó
σ , τ : Thành phần pháp tuyến và tiếp tuyến áp lực tiếp xúc;
υ: Vector vận tốc tương tác trượt giữa chất độn và vỏ;
[ur] = ur (R + 0) - ur (R - 0): Độ dịch chuyển trên miền biên giữa chất độn và vỏ;
l: Độ dài chất độn.
Đánh giá trạng thái ứng suất - biến dạng vết cắt vỏ tiếp xúc với vật thể đàn hồi (chất độn) làm giảm để giải hệ phương trình tuyến tính [18, 19]
K × a = f (2)
Trong đó:
K: Ma trận độ cứng;
a: Vector dịch chuyển các phần tử tại nút thiết kế;
f: Vector lực đặt tại nút.
Để giải hệ phương trình (2) áp dụng quy trình tải từng bước với các đặc điểm kỹ thuật điều kiện biên (1) phương pháp lặp đi lặp lại tại mỗi bước. Làm tăng tải nhỏ có lựa chọn để duy trì mối quan hệ giữa dịch chuyển và biến dạng tại biên trong mỗi giai đoạn tải.
Sử dụng tính đối xứng của vỏ đàn hồi dọc theo trục x để tiết kiệm một nửa thời gian xem xét thiết kế ước tính. Hình 3 trình bày mô hình phần tử hữu hạn phân chia vỏ và chất độn.
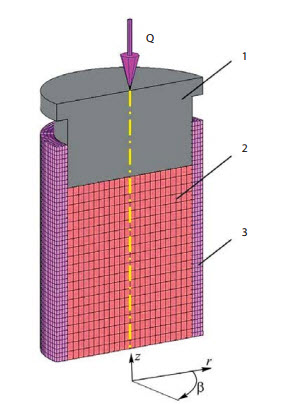 |
1.Piston cứng hoàn toàn; 2. Chất độn đàn hồi; 3. Vỏ hình trụ với vết cắt dọc theo đường sinh
|
Hình 3: Mô hình phân tử hữu hạn của vỏ vật liệu đàn hồi
Để lựa chọn mô hình mật độ phân chia các phần tử, nhóm tác giả đã xây dựng mạng lưới các phần tử bằng việc cung cấp đầy đủ với kết quả chính xác cao, giúp thu được kết quả nhanh chóng.
4. Phân tích kết quả thu được
Để minh họa cho một số kết quả đặc trưng bằng đồ thị, xem xét một hệ thống với các thông số sau: vật liệu vỏ thép hợp kim 40ХНМА (cường độ giới hạn σy = 950MPa, module Young = 2,1 x 1011Pa, module cắt = 8 x 1010Pa, hệ số Poisson = 0,31); chất độn - cao su thô hàm lượng cao kháng xăng 7-3826С (module Young = 2 x 107Pa, module cắt = 7 x 106Pa, hệ số Poisson = 0,4995); bán kính nội tiếp ống R = 0,08m; độ dài ống 0,5m; độ dài chất độn 0,4m; độ dày của ống h = 0,015m; hệ số ma sát giữa vỏ ống và chất độn μ = 0,5.
Hình 4. Phân bố dịch chuyển xuyên tâm vỏ trụ chịu tải với tải trọng trên phần tử đàn hồi Q = 100κN
Hình 5. Phân bố tải trọng vòng trên bề mặt nội tiếp của vỏ trụ chịu tải với vết cắt có tải trọng trên phần tử đàn hồi Q = 100κN
Hình 6. Biểu đồ chu kỳ tải trọng vỏ với các phần tử đàn hồi
Hình 7. Đánh giá cường độ vỏ đàn hồi với vết cắt khi tải trọng ngoại tiếp trên piston bằng 100кН
Điều kiện tại các đầu chất độn σz(r; β; 0,2) = − Q πR τz (r; β; 0, 2) = 0 r [0, R], β [0,360 ] và phạm vi thay đổi áp suất trên piston Q = 0...100kH. Mặt cắt ống tự do với áp suất Hình 4 mô tả sự phân bố dịch chuyển xuyên tâm vết cắt ống dọc theo đường sinh với các giá trị đặc trưng độ phương vị β. Nhìn chung, đồ thị hoàn toàn biến dạng không đối xứng đáng kể thanh mang tải ống đàn hồi và những đường cong riêng biệt thông báo đặc điểm số lượng dịch chuyển xuyên tâm. Dịch chuyển xuyên tâm nhỏ nhất xảy ra ở phạm vi vết cắt ống và lớn nhất ở góc phương vị β = 90o. Thay đổi hình dạng chất độn theo độ biến dạng vết cắt ống cung cấp độ dẻo của ống đàn hồi. Kết quả tương tác tiếp xúc chất độn với ống dịch chuyển xuyên tâm đường sinh ống phân bố không đều. Phân tích sau đó cho thấy sự gia tăng hệ số ma sát giữa chất độn và vỏ ống tăng lên không đồng đều. Khi độ phương vị cố định β đạt giá trị tối đa dịch chuyển xuyên tâm của thanh mang tải xảy ra tại các khu vực gần các mặt phẳng đầu piston. Khoảng cách từ đầu piston dịch chuyển xuyên tâm giảm. Điều này cho thấy việc tăng chiều dài vỏ chịu lực và chất độn không kèm theo sự gia tăng lâu dài đàn hồi phù hợp (nhóm tác giả đã chứng minh điều này bằng cách thay đổi độ dài của mô hình). Rõ ràng, có đầy đủ cơ sở để thiết lập vấn đề tối ưu hóa các tính toán của chiều dài vỏ cắt trong các điều kiện để đảm bảo các yếu tố đàn hồi phù hợp tối đa. Sự dịch chuyển dọc theo trục vỏ trụ so với xuyên tâm là rất nhỏ và ảnh hưởng không đáng kể đến hiệu suất, tính năng của các phần tử đàn hồi do không hiển thị sự thay đổi của giá trị.
Hình 5 cho thấy sự phân bố của các vòng tải trọng σβ trên bề mặt nội tiếp của vỏ trụ với vết cắt dọc theo đường sinh ở những giá trị góc phương vị β khác nhau. Phân tích trạng thái ứng suất của vật liệu lớp vỏ cho thấy áp suất này rất quan trọng trong việc đánh giá sức bền của thanh mang tải. Sự biến dạng vỏ với vết cắt trong điều kiện tương tác tiếp xúc với chất độn dẫn đến thay đổi trong giá trị của tải trọng vòng theo độ dày vỏ. Cụ thể trên bề mặt nội tiếp xuất hiện các vòng tải trọng kéo lớn nhất (bề mặt ngoại tiếp - căng), nguy hiểm nhất trong các mặt cắt dọc với góc phương vị β = 180o. Sự thay đổi giá trị tải trọng vòng dọc theo mặt đường sinh về bản chất tương tự như sự thay đổi của các dịch chuyển xuyên tâm. Áp lực lớn nhất nằm ở các mặt cắt ngang nằm gần các đầu piston.
Khi phân tích trạng thái ứng suất - biến dạng và xây dựng các đồ thị trình bày trong Hình 4 và 5, nhóm tác giả đã chứng minh áp lực ngoại tiếp bền vững hoặc đơn điệu tăng. Tiếp theo là phân tích các hiện tượng trễ xảy ra trong hệ thống vỏ cắt - chất độn đàn hồi ảnh hưởng đến áp lực đơn điệu ngoại tiếp. Trong các nghiên cứu trước áp lực ngoại tiếp đã được xây dựng biểu đồ biến dạng với các phần tử đàn hồi, có thể dự đoán trạng thái của các phần tử đàn hồi trong bất kỳ thời điểm nào và đồng thời ước tính được độ lớn năng lượng phân tán.
Xem xét vỏ đàn hồi với vết cắt (Hình 2b), lực piston thay đổi theo chu kỳ thời gian có hệ số bất đối xứng s = Qmin/Qmax ≥ 0. Hình 6 trình bày các tính chất đặc trưng nhất của các vòng trễ giảm xóc khoan với các phần tử đàn hồi tại các hệ số ma sát tương tác giữa vỏ và chất độn μ khác nhau. Trong quá trình xây dựng sơ đồ này, nhóm tác giả đã phân tích bản chất sự thay đổi tương tác tải giữa chất độn và vỏ. Trong Hình 6, thanh OA (đường liền) hướng lên mô tả giai đoạn tải trọng hữu công ban đầu từ 0 đến 100кN. Ở giai đoạn này, tải trọng trên toàn bộ bề mặt tiếp xúc trượt tương đối chất độn và vỏ theo hướng dịch chuyển của piston. Điều này thể hiện thành phần tải trọng tiếp tuyến τrz cùng một hướng trên toàn bộ bề mặt tiếp xúc. Độ co của piston δ trong giai đoạn này phụ thuộc vào tải trọng. Thanh phi tuyến OA đặc trưng cho quá trình giảm tải trọng các phần tử đàn hồi với tải trọng ngoại tiếp từ tối đa đến O. Các bề mặt tiếp xúc chất độn với vỏ cắt có 2 khu vực với thành phần dấu hiệu khác nhau tải trọng tiếp tuyến τrz, chứng tỏ khu vực tiếp xúc được chia thành vùng trượt ngược và vùng kẹp chặt. Trong quá trình giảm tải trọng, kích thước của các khu vực này thay đổi liên tục. Nếu vỏ đàn hồi giảm tải nhẹ, bắt đầu nạp tải trở lại, sau đó quá trình này lặp lại tải trọng hoạt động mô tả thanh tăng (phi tuyến) BA.
Đối với tải trọng đơn điệu các phần tử vỏ đàn hồi với vết cắt, do ma sát tương tác giữa chất độn với vỏ, phần năng lượng cung cấp cho hệ thống sẽ tiêu biến. Giá trị tiêu hao cho mỗi chu kỳ ψ tại bất kỳ thời điểm nào, tải trọng có thể tính toán như diện tích của vòng trễ được xây dựng (Hình 6):

Các biểu đồ thể hiện hiệu quả dự kiến tăng theo các phần tử đàn hồi trong khi giảm hệ số ma sát giữa chất độn và vỏ. Bên cạnh đó, sự gia tăng hệ số ma sát giữa chất độn và vỏ làm cho lượng năng lượng tiêu hao cho mỗi chu kỳ tải giảm (ví dụ, diện tích vòng giảm chấn khi μ = 0,8 nhỏ hơn khi μ = 0,3). Mô tả hiệu quả nhờ sự gia tăng hệ số ma sát tiếp xúc chỉ sự hao hụt riêng năng lượng khi vỏ giảm xóc hoạt động luôn luôn tăng. Bên cạnh đó, sự gia tăng hệ số μ với các điều kiện tương tự khác nhau, làm giảm chuyển động trong hệ thống, dẫn đến giảm lượng năng lượng tiêu hao. Điều quan trọng là trong vỏ đàn hồi với vết cắt phân chia các lực ma sát phụ thuộc vào sự biến dạng tiếp xúc các phần tử (chất độn và vỏ), tuy nhiên giá trị biến dạng phụ thuộc vào lực ma sát. Mối quan hệ chặt chẽ này xác định cụ thể, thường xuyên, bằng trực quan không thể dự đoán được đặc điểm tính năng của hệ thống đang được xét.
Sử dụng các vỏ mang tải với phần lớn chất liệu là các phần tử đàn hồi ở trạng thái tải trọng khó khăn. Để đánh giá cường độ cuối cùng, nhóm tác giả sử dụng tiêu chí năng lượng Huber-Mises. Theo tiêu chí này, cường độ của vỏ với vết cắt sẽ được cung cấp nếu thỏa mãn bất bình đẳng:
Trong đó:
σ1, σ2, σ3: Ứng suất chính vật liệu vỏ cắt;
[σ]: Ứng suất cho phép đối với các vật liệu làm vỏ.
Hình 7 thể hiện sự phân bố các hệ số độ cứng an toàn k = σy/σtd tại giao điểm theo chiều dọc nguy hiểm nhất vỏ mang tải với vết cắt (bề mặt bên trong vỏ với góc phương vị β = 180o). Biểu hiện phân bố với hệ số ma sát giữa chất độn và vỏ cắt khác nhau μ = 0,3…0,8. Phân tích sự phụ thuộc này cho thấy trạng thái giới hạn của vỏ cắt đạt được lần đầu tiên trên bề mặt nội tiếp ở các đầu piston. Với sự giảm hệ số ma sát giữa chất độn và vỏ biên độ độ cứng thiết kế giảm. Ví dụ, khi hệ số ma sát μ = 0,8, hệ số biên độ độ cứng thiết kế = 4,1 và khi μ = 0,3 hệ số biên độ cứng thiết kế giảm xuống còn 2,2. Xét các đồ họa tương thích trong Hình 6 và 7, biến đổi các giai đoạn thiết kế hình học và thông số ma sát dọc vỏ đàn hồi đối với mỗi mô hình cụ thể giảm xóc khoan cần thiết để đảm bảo cung cấp đầy đủ và cân bằng cường độ theo yêu cầu của giảm chấn.
5. Kết luận
Bài báo giới thiệu thiết kế ban đầu bộ giảm xóc khoan dựa trên các phần tử vỏ trụ đàn hồi hoạt động song song. Sử dụng vỏ hình trụ với vết cắt như các bộ phận hoạt động chính của thiết bị cho phép kết hợp tải trọng thiết kế cao với độ cứng tương đối thấp và giảm xóc ở mức độ cần thiết đủ để giảm xóc hiệu quả.
Nghiên cứu trạng thái ứng suất - biến dạng và thu nhận đặc tính hoạt động của vỏ vật liệu đàn hồi với vết cắt sử dụng mô hình phần tử hữu hạn của tương tác tiếp xúc vỏ cắt và chất phụ đàn hồi. Sử dụng các thuật toán lặp đi lặp lại để giải quyết các vấn đề được sử dụng có tính đến ma sát ở các bề mặt tiếp xúc.
Phân tích tổng thể trạng thái ứng suất - biến dạng của các phần tử đàn hồi trong thiết bị giảm xóc. Lưu ý chính đối với thiết kế biến dạng bất đối xứng. Sử dụng các tiêu chuẩn năng lượng để ước tính độ bền kết cấu. Xây dựng và phân tích các vòng từ trễ đối với nhiều chu kỳ tải của các phần tử đàn hồi. Sử dụng các phương pháp tính toán đề xuất cho phép sử dụng hiệu quả hơn thiết bị giảm xóc, cải thiện thiết kế vỏ bộ hấp thụ rung tuân thủ tối đa tiêu chí và mức độ yêu cầu của giảm xóc để tạo tiền đề phát triển các phương pháp kỹ thuật và thiết kế mới cho hệ thống triệt tiêu rung.
Các giai đoạn nghiên cứu của nhóm tác giả cho thấy sự phát triển của lý thuyết tương tác tiếp xúc khối vỏ cắt để sử dụng hiệu quả thiết bị giảm xóc khoan.
Tài liệu tham khảo
1.V.I.Gulyayev, S.M.Hudoliy, O.V.Glushakova. Simulation of torsion relaxation auto-oscillations of drill string bit with viscous and coulombic friction moment models. Journal of Multi-body Dynamics. 2011; 225: p. 139 - 152.
2. П.І.Огородніков, В.М.Світлицький, Ю.З.Щербатюк. Захистбурильноїколонивідвібраційних навантажень. К.: Інтерпрес ЛТД. 2012.
3. V.I.Gulyayev, L.V.Shevchuk. Nonholonomic dynamics of drill string bit whirling in a deep bore-hole. Journal of Multi-body Dynamics. 2013; 227(3): p. 234 - 244.
4. A.P.Christoforou, A.S.Yigit. Fully coupled vibrations of actively controlled drillstrings. Journal of Sound and Vibration. 2003; 267(5): p. 1029 - 1045.
5. M.Karkoub, Y.Abdel-Magid, B.Balachandran. Drill- String torsional vibration suppression using GA optimized controllers. Journal of Canadian Petroleum Technology. 2009; 48(12): p. 32 - 38.
6. А.С.Величкович, В.М.Шопа. Бурові амортизатори як засіб підвищення техніко- економічних показників буріння свердловин. Нафтова і газова промисловість. 2000; 3: c. 16 - 18.
7. А.С.Величкович. Буровой амортизатор на базе новой оболочечной пружины. Хим. и нефтегазовое машиностроение. 2005; 7: c. 9 - 11.
8. A.S.Velichkovich. Design features of shell springs for drilling dampers. Chemical and Petroleum Engineering. 2007; 43(7 - 8): p. 458 - 461.
9. А.С.Величкович, В.М. Шопа. Комплекс засобів віброзахисту та регулювання динамічного режиму бурильноїколони. Івано-Франківськ: Сіверсія ЛТД. 2000.
10. Toro Downhole Tools. Drilling tools catalog. Tomball, Texas USA. 2012.
11. Secoroc Rock Drilling Tools. Product catalogue - Rotary products. Atlas Copco Secoroc AB. 2009.
12. VNIIBT - Drilling Tools. Product catalogue. Perm, Russia. 2012.
13. Shock Sub. Impact and vibration reduction sub. Schlumberger. 2011.
14. В.М.Шопа, А.С.Величкович та ін. Оболонкові пружини. Івано-Франківськ: Факел. 2002.
15. А.С.Величкович. Некоторые конструктивные особенности оболочечных пружин для буровых амортизаторов. Хим. и нефтегазовое машиностроение. 2007; 8: c. 26 - 29.
16. A.S.Velichkovich, I.I.Popadyuk, V.M.Shopa. Experimental study of shell flexible component for drilling vibration damping devices. Chemical and Petroleum Engineering. New York: Springer. 2011; 46(9 - 10): p. 518- 524.
17. А.С.Величкович, Т.М.Даляк. Експериментальна верифікація скінченно-елементної моделі контактної взаємодії розрізаної оболонки з пружним тілом. А науковий вісник ІФНТУНГ. 2012; 1(31): c. 80 - 86.
18. O.C.Zienkiewicz, Robert Leroy Taylor. The Finite element method: Solid mechanics. Bristol: Butterworth- Heinemann. 2000.
19. Mats G.Larson, Fredrik Bengzon. The finite element method: Theory, implementation and applications. Berlin Heidelberg: Springer-Verlag. 2013.
Summary
Shell elastic element with cut for drilling shock absorber
A.S.Velychkovych; Vo Duc Anh - Ivano-Frankivsk National Technical University of Oil and Gas,
T.M.Dalyak. - Podstrigach Institute of Applied Problems of Mechanics and Mathematics, NAS of Ukraine, Ivano-Frankivsk, Ukraine
Email: voducanh94@gmail.com
The study presents an initial design of the drilling shock absorber, developed on the basis of building a verified digital model of shell damper with the cut and using the algorithms of solution of the contact problems taking into account friction on contact surfaces. The overall picture of the stress-strain state of the elastic element of shell shock absorber is analysed. Structural strength is estimated using energy criteria. The hysteresis loops are constructed and analysed for a number of cyclic loading of the elastic element. The study results therefore allow assessment of the effect of the elastic properties of materials and the shell filler, their geometric parameters and tribo- logical properties on the operating parameters. This enables more efficient use of the drilling facilities and improvement of the design of shell shock guards for maximum compliance with the criteria and the required level of damping, thus creating the preconditions for development of new technical solutions and design for systems of vibration protection.
Key words: Elastic body, shell, drilling shock absorber, damping, vibroprotection.