Tóm tắt
Phương án tiềm năng được đề xuất trong nghiên cứu này là thu hồi kim loại từ xúc tác thải từ các nhà máy đạm để tổng hợp xúc tác xử lý khí thải. Các thông số công nghệ của quá trình hòa tách để thu hồi kim loại Ni từ xúc tác thải của nhà máy đạm theo phương pháp hòa tách bằng dung dịch HNO3 đã được khảo sát với các thông số gồm: điều kiện đốt cốc, kích thước hạt xúc tác thải, nồng độ acid sử dụng, tỷ lệ rắn/lỏng, nhiệt độ, thời gian hòa tách, tốc độ khuấy trộn. Kết quả cho thấy quy trình thu hồi cho độ thu hồi hơn 90% Ni với độ tinh khiết sản phẩm trên 90% trong 1 giờ. Muối Ni được thu hồi từ quá trình trên được sử dụng làm tiền chất cho quá trình tổng hợp xúc tác xử lý CO, C3H6 theo con đường oxy hóa hoàn toàn. Xúc tác được tổng hợp từ Ni thu hồi có hình thái và hoạt tính tương đồng với xúc tác được tổng hợp từ muối Ni thương mại. Nhiệt độ chuyển hóa trên 90% đối với CO, C3H6 của hai xúc tác khoảng 268oC ở GHSV > 100.000 h-1.
Từ khóa: Xử lý CO, C3H6, xúc tác thải, nhà máy đạm, Ni, light-off.
1. Mở đầu
Hiện nay, tại các nhà máy đạm Phú Mỹ, đạm Cà Mau đang sử dụng khoảng 16 loại xúc tác với tổng khối lượng hơn 1000 tấn. Tùy vào mỗi loại xúc tác mà thời gian sử dụng có thể thay đổi từ 2 đến 10 năm. Đối với các nhà máy này lượng xúc tác chứa kim loại Ni chiếm từ 20% đến 30% trên tổng khối lượng xúc tác sử dụng.
Các loại xúc tác này hoạt động ở nhiệt độ cao với sự hiện diện của nhiều tác nhân gây ngộ độc và cốc nên không thể tránh khỏi việc xúc tác bị đầu độc và mất dần hoạt tính do các tâm hoạt tính bị che lấp hoặc quá trình kết khối của pha hoạt tính. Xúc tác mất dần hoạt tính sau đó được tái hoạt hóa và sử dụng lại. Nhưng trong thực tế, quá trình tái hoạt hóa không giúp xúc tác có được hoạt tính như ban đầu do các quá trình mất hoạt tính thường là bất thuận nghịch (ví dụ quá trình kết khối).
Kết quả sau một thời gian (2 - 3 năm), xúc tác mất hoạt tính và phải được thải loại. Lúc này xúc tác thải được xếp vào hạng mục chất thải rắn công nghiệp nguy hại do có hàm lượng kim loại cao.
Có nhiều hướng nghiên cứu được phát triển nhằm thu hồi Ni từ xúc tác thải như: hòa tách [1 - 3], nung chảy [4, 5], điện phân [6 - 7], trao đổi ion [8]. Trong đó, phương pháp hòa tách được nghiên cứu rộng rãi nhất do sự đơn giản, rẻ tiền và hiệu suất thu hồi Ni cao. H2SO4 được nghiên cứu phổ biến để hòa tách Ni do acid này có giá thành thấp và khả năng hòa tách Ni tốt. Sản phẩm thu được trực tiếp là muối NiSO4 [9]. Hiệu suất thu hồi có thể đạt được 85% [3].
Quy trình thu hồi hoàn toàn Ni bằng H2SO4 được xây dựng bởi Lee và cộng sự [2]. Nồng độ acid thường được nghiên cứu trong khoảng từ 10 - 50%, kích thước hạt nhỏ hơn 500mm, tỷ lệ rắn/lỏng (xúc tác thải/acid) dao động trong khoảng 1/1 xuống 1/12 [10]. Tuy vậy, việc sử dụng H2SO4 có nhiều nhược điểm, nhất là vấn đề ăn mòn cao.
Khí thải phát sinh trong quá trình vận hành các động cơ, lò đốt sử dụng nhiên liệu xăng, diesel... như CO, các hydrocarbon mạch ngắn (HC) và NOx… là nguyên nhân chính gây ô nhiễm môi trường không khí. Nếu NOx phải được khử về N2 thì CO, HC cần được oxy hóa hoàn toàn thành CO2 và H2O. Kết quả nghiên cứu [11] trên hệ xúc tác 2 kim loại là Pd và Ni cho thấy Ni là tác nhân có khả năng xúc tác cho quá trình oxy hóa hoàn toàn CO và HC. Tiền chất Ni được sử dụng cho quá trình tổng hợp là Ni(NO3)2.6H2O, tuy nhiên các tác giả vẫn chưa cho thấy hiệu quả xử lý CO, HC trên hệ Ni riêng lẻ [11]. Ngoài ra, Ni cũng được sử dụng rất nhiều trong các hệ xúc tác xử lý khí thải như thành phần phụ gia [12].
Trên các cơ sở này, nhóm tác giả thực hiện giải pháp mang tính toàn diện cho việc xử lý môi trường là thu hồi Ni từ xúc tác thải của các nhà máy đạm để làm tiền chất tổng hợp xúc tác xử lý khí thải. Với định hướng sử dụng Ni làm tiền chất tổng hợp xúc tác thì tiền chất muối nitrate được sử dụng rộng rãi nhất do muối này dễ phân hủy trong quá trình tổng hợp [11]. Vì vậy, quá trình thu hồi Ni từ xúc tác thải cần phải tiến hành với tác nhân là HNO3 chứ không phải các acid khác thường được sử dụng để thu hồi Ni (như HCl, H2SO4). Ngoài ra, trong quá trình tổng hợp, Ni thực tế ở dạng Ni2+, do đó chất lượng quan trọng của Ni để tổng hợp chính là độ tinh khiết của dung dịch Ni2+.
Kết quả nghiên cứu của Oza và cộng sự về quá trình hòa tách thu hồi Ni bằng dung dịch HNO3 từ xúc tác thải Ni/Al2O3 cho thấy quá trình hòa tách bao gồm khá nhiều bước như: nghiền, rây phân loại hạt xúc tác, đốt cốc sau đó mới cho xúc tác tiếp xúc với acid để tách Ni [13]. Tuy nhiên, trong nghiên cứu này có một số điểm cần làm rõ như ảnh hưởng của điều kiện đốt cốc, nghiền, khuấy trộn và các thông số trong quá trình hòa tách đến hiệu quả của quá trình hòa tách. Trong nghiên cứu [13], Oza đã lựa chọn ngẫu nhiên các thông số này. Điều kiện tiến hành thí nghiệm ảnh hưởng rất lớn đến hiệu quả của quá trình hòa tách [14], do đó cần khảo sát để tìm ra thông số phù hợp nhằm tiết kiệm thời gian, chi phí và năng lượng.
Như vậy, việc thu hồi Ni từ xúc tác thải của các nhà máy lọc hóa dầu thông qua việc hòa tách Ni bằng acid là khả thi. Đồng thời, hướng sử dụng Ni thu hồi để tổng hợp xúc tác xử lý khí thải về khía cạnh môi trường và kinh tế là có tiềm năng do sử dụng nguyên liệu là chất thải rắn để tạo ra các sản phẩm có giá trị cao. Trong nghiên cứu này, nhóm tác giả đã khảo sát tìm thông số phù hợp cho quá trình hòa tách thu hồi Ni từ xúc tác thải của nhà máy đạm bằng dung dịch acid HNO3: điều kiện đốt cốc, nghiền, khuấy trộn, nồng độ acid sử dụng, tỷ lệ rắn/lỏng, nhiệt độ, thời gian hòa tách. Sau đó, đánh giá khả năng sử dụng Ni thu hồi so với việc sử dụng Ni tinh khiết trong tổng hợp xúc tác xử lý CO và C3H6.
2. Thực nghiệm
Xúc tác thải dùng để thu hồi Ni có tên thương mại là RKS-2-7H của Nhà máy Đạm Phú Mỹ. Thành phần xúc tác như sau: Ni 8,51% khối lượng, Mg 8,61% khối lượng, Al 23,15% khối lượng, O 59,73% khối lượng. Acid dùng để hòa tách: HNO3 đậm đặc (Trung Quốc).
Quá trình hòa tách được thực hiện như sau: Cân lượng xác định xúc tác thải (có thể trải qua quá trình đốt cốc ở nhiệt độ 540oC hoặc không) cho vào dung dịch HNO3 nồng độ từ 1 - 2,5M theo tỷ lệ rắn/lỏng từ 1/30g/ml - 1/5g/ ml trong bể hòa tách bằng thủy tinh. Nhiệt độ hòa tách từ 80 - 106oC. Tốc độ khuấy trộn được điều chỉnh trong khoảng từ 0 - 600 (vòng/phút). Quá trình hòa tách được thực hiện trong 30 phút đến 2 giờ. Phần hơi acid bốc lên được dẫn qua bể NaOH hấp thụ trước khi thải ra ngoài.
Sau khi hòa tách, tách riêng phần lỏng và rắn. Phần rắn được rửa bằng nước cất 3 lần, thu lấy dung dịch rửa và hòa trộn với phần lỏng được sản phẩm lỏng chứa muối Ni thu hồi. Hàm lượng các nguyên tố Ni2+, Al3+ và Mg2+ được xác định bằng phương pháp ICP (Inductivity Coupled Plasma). Phần rắn được thải bỏ theo các quy định về quản lý chất thải rắn. Các thí nghiệm lặp lại 3 lần, lấy giá trị trung bình. Sai số của phép tính hiệu suất thu hồi được tính theo phương pháp thống kê với độ tin cậy của kết quả là 95% (Zp = 1,96). Sai số của phép tính hiệu suất thu hồi Ni bằng ± 0,93%.
Hòa muối Ni(NO3)2 thu hồi được ở trên với muối Mn(NO3)2 (hóa chất tinh khiết Merck) trong môi trường nước, sau đó hỗn hợp được khuấy trộn với γ-Al2O3 (hóa chất tinh khiết Merck) để tổng hợp chất xúc tác xử lý CO và hydrocarbon theo phương pháp đồng kết tủa. Khối lượng các muối nitrate của Mn (II), Ni (II) được tính toán sao cho tỷ lệ khối lượng của mỗi oxide tương ứng trong mẫu xúc tác là 20% khối lượng. Tổng khối lượng của hỗn hợp xúc tác là 100% khối lượng. Dung dịch dùng để điều chỉnh pH là NH3. Hỗn hợp sau đó được cô cạn ở nhiệt độ 90oC, sấy ở nhiệt độ 110oC trong 12 giờ và nung ở nhiệt độ 550oC trong 4 giờ trong môi trường khử (30%H2 : 70%N2).
Xúc tác thu được được ký hiệu là NiMn/Al-TH. Bên cạnh đó, nhóm tác giả cũng tổng hợp 1 mẫu so sánh với quy trình và thành phần tương tự, chỉ khác ở tiền chất sử dụng là muối Ni(NO3)2 tinh khiết (hóa chất tinh khiết Merck).Mẫu này được ký hiệu là NiMn/Al-TK.
Các tính chất hóa lý của xúc tác sau tổng hợp gồm: thành phần pha (thiết bị Bruker D8 Advance), hình thái của xúc tác như diện tích bề mặt, thể tích lỗ xốp cùng phân bố kích thước lỗ xốp (thiết bị Micromeritics). Phương pháp huỳnh quang tia X được áp dụng trong nghiên cứu này với mục đích xác định hàm lượng Ni trong xúc tác thải trước khi thu hồi. Thí nghiệm được thực hiện trên thiết bị S4 Pioneer (Bruker).
Hoạt tính xúc tác trên phản ứng oxy hóa CO, C3H6 thành CO2, H2O được khảo sát nhờ một hệ thống xúc tác tầng cố định. Phản ứng được tiến hành với tỷ lệ hỗn hợp khí CO:C3H6:O2:N2 = 0,8:0,05:20:79 với áp suất khí quyển.
Tổng lưu lượng hỗn hợp khí là 10 lít/giờ với khối lượng xúc tác sử dụng là 0,1g tương ứng với giá trị lưu lượng thể tích GHSV là 110.000 giờ-1. Trước khi phản ứng, xúc tác được làm sạch bề mặt ở nhiệt độ 400oC trong 2 giờ trong dòng khí N2. Sau khi làm nguội đến nhiệt độ phòng, quá trình khảo sát hoạt tính xúc tác được thực hiện qua quá trình light-off CO từ nhiệt độ 50 - 500oC với tốc độ gia nhiệt là 5oC/phút. Quá trình light-off CO chính là khảo sát độ chuyển hóa CO thành CO2 theo từng nhiệt độ. Nồng độ các khí trong sản phẩm bao gồm CO, CO2 đều được ghi nhận với tần suất 22s/1 điểm nhờ thiết bị phân tích online Ultramat 6E của Siemens (Đức). Trên cơ sở đó, đường light-off có thể được thiết lập. Các mẫu đều được khảo sát hoạt tính ít nhất 4 lần. Sau mỗi lần khảo sát đường light- off CO từ nhiệt độ 50 - 500oC, xúc tác được đưa về nhiệt độ phòng trong môi trường N2 và tiếp tục tiến hành khảo sát light-off lần tiếp theo.
3. Kết quả và thảo luận
3.1. Ảnh hưởng của một số điều kiện thực nghiệm đến hiệu suất của quá trình thu hồi Ni
Nhóm tác giả tập trung khảo sát các thông số liên quan đến điều kiện tiền xử lý xúc tác thải và điều kiện khuấy trộn, tỷ lệ rắn/lỏng trước để làm cơ sở xác định các biến độc lập trước khi tiến hành quy hoạch thực nghiệm cho quá trình thu hồi Ni.
3.1.1. Kích thước hạt
Trong nghiên cứu của Oza [13], điều kiện kích cỡ hạt xúc tác được lựa chọn ngẫu nhiên trong khoảng 1 - 2mm. Tuy nhiên, quá trình nghiền xúc tác liên quan đến năng lượng tiêu hao nên cần có khảo sát để lựa chọn kích thước phù hợp.
Ảnh hưởng của kích thước hạt xúc tác đến hiệu suất thu hồi sản phẩm muối Ni trong 1 giờ hòa tách được thể hiện ở Hình 1. Kết quả cho thấy kích thước hạt d < 200μm làm giảm hiệu suất hòa tách Ni (< 86%), việc nghiền quá nhỏ hạt xúc tác có thể làm giảm hiệu quả quá trình hòa tách tẩm Ni lên bề mặt pha nền nên quá trình nghiền đã làm các phần pha nền bên trong không chứa Ni bị vỡ và tiếp xúc với acid, làm giảm hiệu quả hòa tách Ni. Qua khảo sát này cho thấy việc nghiền xúc tác là không cần thiết do sự khác biệt giữa hiệu suất hòa tách ở các kích thước khác nhau không lớn và việc giữ nguyên kích thước ban đầu giúp tiết kiệm chi phí.
3.1.2. Điều kiện đốt cốc
Theo nghiên cứu của Oza [13], quá trình đốt cốc được mặc định thực hiện ở nhiệt độ 600°C trong 5 giờ. Đây cũng là một bước tiêu hao năng lượng, do đó nhóm tác giả tiến hành khảo sát hiệu quả của quá trình thu hồi ở 2 trường hợp đốt cốc và không đốt cốc trong 1 giờ hòa tách.
Ảnh hưởng của quá trình đốt cốc đến hiệu suất thu hồi Ni ở các nồng độ acid khác nhau được thể hiện trong Hình 2. Điểm đặc biệt là quá trình đốt cốc gây bất lợi cho quá trình hòa tách. Khi thực hiện quá trình đốt cốc trong không khí ở nhiệt độ 550°C thì hiệu suất thu hồi Ni lại giảm từ 7 - 9%. Kết quả này có thể do đốt cốc là một quá trình phát nhiệt và dẫn đến các quá trình kết khối trên bề mặt xúc tác, gây khó khăn cho quá trình phản ứng giữa kim loại và acid. Do đó, quá trình hòa tách sẽ được nhóm tác giả tiến hành trực tiếp trên xúc tác thải mà không cần thực hiện quá trình đốt cốc.
3.1.3. Tốc độ khuấy
Trong nghiên cứu, Oza đã khảo sát tốc độ khuấy trong khoảng 300 - 800 vòng/phút [13]. Kết quả cho thấy tốc độ khuấy không ảnh hưởng đến hiệu quả của quá trình thu hồi. Với đối tượng là xúc tác thải từ Nhà máy Đạm Phú Mỹ, nhóm tác giả đã khảo sát ảnh hưởng của tốc độ khuấy đến hiệu suất thu hồi và độ tinh khiết muối Ni với khoảng khảo sát từ 0 - 600 vòng/phút, thời gian hòa tách 1 giờ (Hình 3).
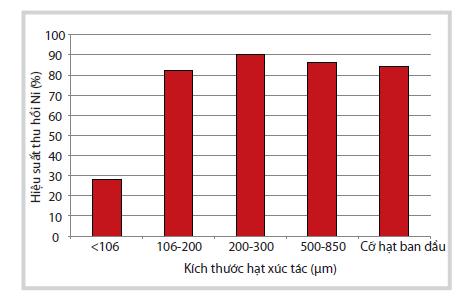 |
Hình 1. Kết quả ảnh hưởng của kích thước
hạt xúc tác đến hiệu suất thu hồi sản phẩm muối Ni. (Điều kiện hòa tách:
xúc tác không đốt cốc, nồng độ acid sử dụng: 2M, tốc độ khuấy 200
vòng/phút, tỷ lệ rắn/lỏng: 1/10, nhiệt độ hòa tách: 100oC trong 1 giờ) |
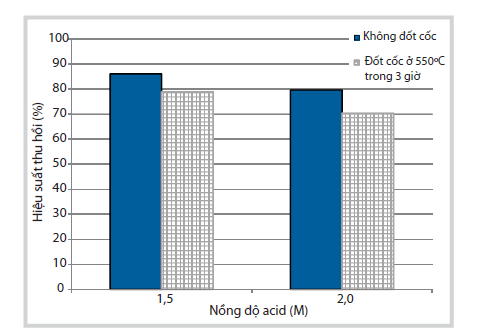 |
Hình 2. Ảnh hưởng của quá trình đốt cốc
(ở 550oC, 3 giờ) đến hiệu suất thu hồi Ni (Điều kiện hòa tách: xúc tác
không nghiền, nồng độ acid sử dụng: 1,5M và 2M, tốc độ khuấy 200
vòng/phút, tỷ lệ rắn/lỏng: 1/10, nhiệt độ hòa tách 100oC trong 1 giờ) |
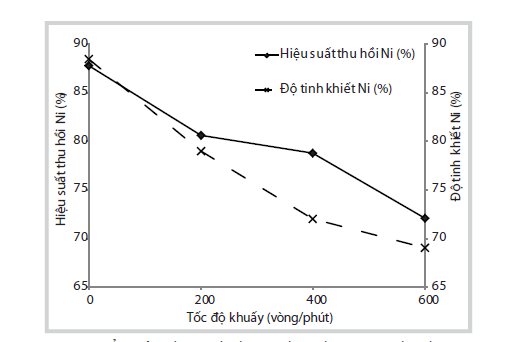 |
Hình 3. Ảnh hưởng tốc độ khuấy đến hiệu suất thu hồi và độ tinh khiết
muối Ni. (Điều kiện hòa tách: xúc tác không đốt cốc, không nghiền, nồng
độ acid sử dụng: 1,5M, tỷlệ rắn/lỏng: 1/20, nhiệt độ hòa tách: 100oC
trong 1 giờ.)
|
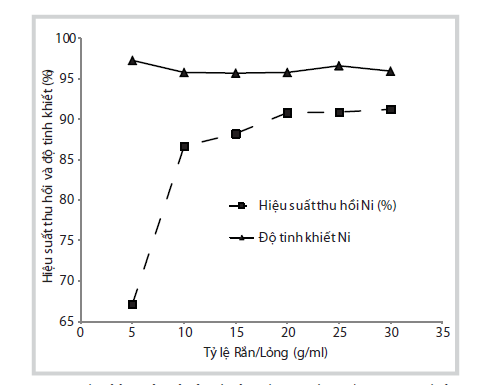 |
Hình 4. Kết quả ảnh hưởng của tỷ lệ
rắn/lỏng đến hiệu suất thu hồi và độ tinh khiết của sản phẩm muối Ni.
(Điều kiện hòa tách: xúc tác không đốt cốc, không nghiền, không khuấy,
nồng độ acid 1,5M, nhiệt độ hòa tách 100oC trong 1 giờ)
|
Theo đó, tốc độ khuấy làm giảm mạnh hiệu suất hòa tách và độ tinh khiết của sản phẩm. Việc tăng tốc độ khuấy làm vỡ các hạt xúc tác và tăng sự hòa tan phần Al trong pha nền. Điều này gây bất lợi đối với quá trình hòa tan của Ni và làm cho sản phẩm có độ tinh khiết thấp hơn.
Kết quả nhóm tác giả thu được là trong điều kiện không khuấy vẫn có thể giúp quá trình hòa tách đạt hiệu suất thu hồi và độ tinh khiết khá cao (khoảng 90%).
3.1.4. Tỷ lệ xúc tác/dung dịch acid (tỷ lệ rắn/lỏng)
Tỷ lệ xúc tác/dung dịch acid phù hợp là một thông số quan trọng ảnh hưởng đến tính hiệu quả của việc sử dụng acid cho quá trình thu hồi. Trong thí nghiệm này, nhóm tác giả cố định điều kiện hòa tách như mô tả ở Hình 4 nhằm đánh giá và lựa chọn tỷ lệ rắn/lỏng phù hợp. Sự thay đổi hiệu suất thu hồi và độ tinh khiết muối Ni theo sự giảm dần tỷ lệ rắn/lỏng trong 1 giờ (Hình 4). Với tỷ lệ rắn/lỏng = 1/5g/ml giảm xuống 1/20g/ml, thì hiệu suất thu hồi Ni tăng từ 67% lên gần 90%. Khi tiếp tục tăng lượng acid với tỷ lệ rắn/lỏng dưới 1/20g/ml thì hiệu suất thu hồi gần như không thay đổi (khoảng 90%). Xét về độ tinh khiết của sản phẩm, các kết quả có giá trị tương đối cao, trên 95%. Vì lý do tỷ lệ rắn/lỏng thấp (dưới 1/20) thì thể tích của thiết bị phản ứng phải lớn và vấn đề xử lý acid dư. Do đó, tỷ lệ rắn/lỏng 1/20g/ml được lựa chọn là điều kiện phù hợp nhất.
3.2. Tối ưu hóa điều kiện thực nghiệm thu hồi Ni
Từ kết quả thí nghiệm khảo sát ảnh hưởng các yếu tố công nghệ đến quá trình hòa tách có thể thấy xúc tác để nguyên hạt ban đầu không cần nghiền và quá trình hòa tách không khuấy trộn cho hiệu suất thu hồi tốt hơn. Bên cạnh đó, tỷ lệ rắn/lỏng trong khoảng 1/30g/ml - 1/10g/ml không ảnh hưởng nhiều đến hiệu quả của quá trình hòa tách, do đó có thể xem các thông số như kích cỡ hạt, tốc độ khuấy, tỷ lệ rắn lỏng là các biến độc lập.
Như vậy, bài toán đặt ra là tìm điều kiện hòa tách phù hợp (nồng độ acid (Z1, M), nhiệt độ (Z2, oC) và thời gian hòa tách (Z3, phút)) để có hiệu suất thu hồi Ni (Hàm mục tiêu - Yhs) và độ tinh khiết sản phẩm muối Ni (Hàm mục tiêu - Ytk) đạt giá trị lớn nhất.
Phương pháp thực hiện là giải bài toán tối ưu theo phương pháp Tiêu chuẩn toàn cục (Global criterion) [15].
Bước 1: Giải bài toán tối ưu cho từng mục tiêu Y*hs (giá trị hiệu suất cực đại) và Y*tk (giá trị độ tinh khiết cực đại) và xác định các tập giá trị tương ứng (Z1, Z2, Z3)*hs và (Z1, Z2, Z3)*tk. Bước 2: Giải bài toán đa mục tiêu dựa trên nguyên tắc tìm giá trị Yopths và Yopttk sao cho các giá trị này gần với giá trị Y*hs và Y*tk nhất thông qua việc tìm giá trị min Z(Yhs,Ytk).
Trong đó, p = 1 hoặc p = 2 (phụ thuộc vào phương án lựa chọn kết quả tối ưu).
Sau đó, tiến hành kiểm tra mức độ đạt được so với giá trị Y*hs và Y*tk thông qua giá trị % giữa Yopths/Y*hs, Yopttk/Y*tk.
Bước 1: Giải bài toán tối ưu cho từng mục tiêu
Nhóm tác giả tiến hành thí nghiệm theo phương pháp leo dốc đứng với 3 yếu tố được khảo sát: nồng độ acid (Z1, M), nhiệt độ (Z2, oC) và thời gian hòa tách (Z3, phút) để tìm để tìm Y*hs và Y*tk.
Phương trình hồi quy có dạng:
Yhs = bo + b1Z1 + b2Z2 + b3Z3 + b12Z1Z2 + b13Z1Z3 + b23Z2Z3 + b11(Z12 - λ) + b22(Z22 - λ) + b33(Z32 - λ)
Với bo, b1, b2,…, b33: Các hệ số của phương trình hồi quy.
Xúc tác thải không đốt cốc và để nguyên cỡ hạt ban đầu cho vào dung dịch HNO3 nồng độ từ 1 - 2,5M theo tỷ lệ rắn/lỏng 1/20g/ml trong bể hòa tách bằng thủy tinh. Nhiệt độ hòa tách từ 80oC - 106oC và không khuấy trộn. Quá trình hòa tách được thực hiện trong khoảng 30 – 75 phút. Phần lỏng sau khi hòa tách được phân tích xác định hàm lượng Ni2+ bằng phương pháp ICP, sau đó tính hiệu suất thu hồi dựa vào thành phần Ni ban đầu trong xúc tác.
Lập ma trận quy hoạch thực nghiệm và xác định các hệ số của phương trình hồi quy với mục tiêu khảo sát 3 yếu tố ảnh hưởng, số thí nghiệm cần phải tiến hành N = 15 [16].Từ đó, xác định được phương trình hồi quy mô tả thực nghiệm.
Nhóm tác giả tiến hành thêm 3 thí nghiệm ở tâm. Sự có nghĩa của các hệ số phương trình hồi quy được kiểm định theo phân bố Student với mức ý nghĩa p = 0,05 và bậc tự do f = 2. Sau đó, sự tương thích của phương trình hồi quy được kiểm tra theo tiêu chuẩn Fisher. Kết quả thực nghiệm của hiệu suất thu hồi Ni (Yhs) và độ tinh khiết (Ytk) được bố trí trên bảng ma trận mở rộng (Bảng 2).
Với x1, x2, x3 lần lượt là biến mã hóa của biến thực Z1, Z2, Z3.
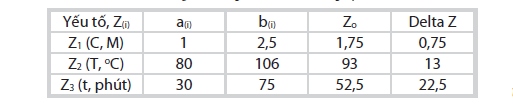 |
Bảng 1. Khoảng biến thiên của thí nghiệm |
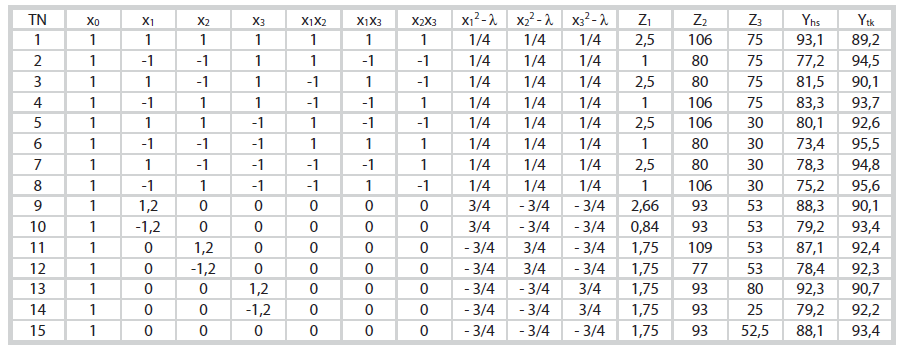 |
Bảng 2. Kết quả quy hoạch thực nghiệm hiệu suất (Yhs) và độ tinh khiết (Ytk) của quá trình hòa tách thu hồi Ni từ xúc tác thải |
Vậy, qua quá trình khảo sát, đã xác định được phương trình hồi quy của Yhs có dạng:
Yhs = 82,3 + 3,2Z1 + 2,9Z2 + 4Z3 + 1,8Z2Z3 - 2,8(Z12 - 0,75) - 3,5(Z22 - 0,75) (3)
Điều này cho thấy nồng độ acid, nhiệt độ hòa tách và thời gian hòa tách đều tỷ lệ thuận với hiệu suất thu hồi Ni.
Tính toán tương tự phương trình hồi quy của Ytk có dạng:
Ytk = 92,7 - 1,5Z1 - 1,2Z3 (4)
Điều này cho thấy nồng độ acid và thời gian hòa tách đều tỷ lệ nghịch với độ tinh khiết sản phẩm muối Ni. Nhiệt độ không ảnh hưởng đáng kể đến độ tinh khiết.
Từ các mối quan hệ giữa điều kiện hòa tách (nồng độ acid (Z1, M), nhiệt độ (Z2, oC), thời gian hòa tách (Z3, phút)) và hàm mục tiêu hiệu suất thu hồi Ni (Yhs) max, độ tinh khiết sản phẩm muối Ni (Ytk) max như phương trình (I) và (II). Giá trị Y*hs và Y*tk được giải nhờ sự hỗ trợ của phần mềm Exce - Solver trong vùng giới hạn nghiên cứu (Bảng 1) như sau:
Y*hs = 94,4% với:
Z1*hs = 2,2M
Z2*hs = 102oC
Z3*hs = 79,5 phút
Y*tk = 95,9% với:
Z1*tk = 0,9M
Z2*tk = 77oC
Z3*tk = 26 phút
Bước 2: Giải bài toán tối ưu đa mục tiêu thông qua việc tìm giá trị minZ(Yhs,Ytk)
Xét p = 1. Lúc đó minZ có dạng
Kết quả tối ưu được giải nhờ sự hỗ trợ của phần mềm Excel - Solver như sau:
Z1opt = 2M; Z2opt = 102oC; Z3opt = 80 phút;
Yopths = 94,2% (mức độ đạt được 94,2/94,4 = 99,8%);
Yopttk = 90,8% (mức độ đạt được 90,8/95,9 = 94,7%);
Tương tự, xét p = 2. Lúc đó minZ có dạng
Kết quả tối ưu được giải nhờ sự hỗ trợ của phần mềm Excel - Solver như sau:
Z1opt = 1,6 M; Z2opt = 102oC; Z3opt = 80 phút;
Yopths = 92,9% (mức độ đạt được 92,9/94,4 = 98,4%);
Như vậy, thông qua việc giải bài toán tối ưu đa mục tiêu ta thu được kết quả sau:
- Nếu chọn hiệu suất là thông số ưu tiên thì điều kiện hòa tách như sau: nồng độ acid 2M; nhiệt độ hòa tách 102oC và thời gian 80 phút. Tương ứng với điều kiện này, hiệu suất tối ưu đạt 94,2% và độ tinh khiết muối Ni 90,8%.
- Nếu chọn độ tinh khiết là thông số ưu tiên thì điều kiện hòa tách như sau: nồng độ acid 1,6M; nhiệt độ hòa tách 102oC và thời gian 80 phút. Tương ứng với điều kiện này, độ tinh khiết muối Ni 91,6% và hiệu suất tối ưu đạt 92,9%.
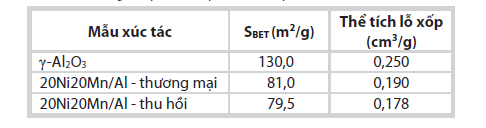 |
Bảng 3. Diện tích bề mặt, thể tích lỗ xốp của các mẫu xúc tác |
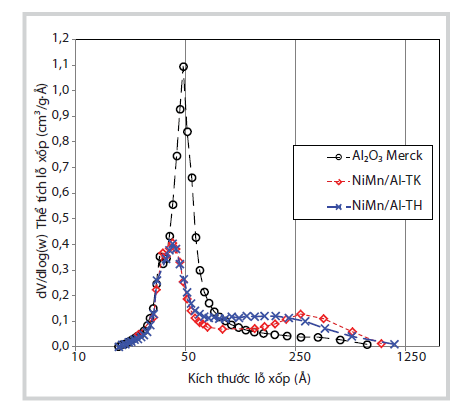 |
Hình 5. Kết quả phân bố kích thước lỗ xốp của các mẫu xúc tác 3.3. Ứng dụng muối Ni thu hồi để tổng hợp xúc tác xử lý CO và C3H6
|
3.3.1. Tính chất hóa lý của xúc tác
Trong một nghiên cứu khác của nhóm tác giả, hệ xúc tác có thành phần 20% khối lượng Ni, 20% khối lượng Mn trên nền γ-Al2O3 đã được phát triển và cho thấy hiệu quả rất tốt cho quá trình xử lý CO theo con đường oxy hóa hoàn toàn thành CO2 [17]. Do đó, để thấy được đầy đủ tính chất và khả năng ứng dụng của muối Ni thu hồi, nhóm tác giả tiến hành tổng hợp xúc tác theo thành phần này.
Bảng 3 thể hiện kết quả diện tích bề mặt (SBET) và thể tích lỗ xốp của các mẫu xúc tác. Trong bảng này, nhóm tác giả trình bày các kết quả của chất mang γ-Al2O3 và 2 loại xúc tác có thành phần 20% khối lượng Ni, 20% khối lượng Mn trên nền γ-Al2O3, trong đó kim loại Ni đi từ 2 nguồn muối Ni thu hồi (ký hiệu xúc tác 20Ni20Mn/Al – thu hồi) và muối Ni thương mại (ký hiệu xúc tác 20Ni20Mn/Al - thương mại). Kết quả cho thấy diện tích bề mặt, thể tích lỗ xốp của 2 hệ xúc tác 20Ni20Mn/Al tinh khiết, 20Ni20Mn/ Al - thu hồi chênh lệch không đáng kể.
Các kết quả phân tích phân bố kích thước lỗ xốp ở Hình 8 cho thấy sự có mặt Ni đã làm giảm dần thể tích và kích thước lỗ xốp đặc trưng của Al2O3. Kim loại Ni đã được kết tủa trong các lỗ xốp kích thước 5nm đặc trưng của Al2O3. Do đó làm giảm thể tích lỗ xốp từ 0,25cm3/g xuống còn 0,18cm3/g. Sự giảm thể tích lỗ xốp này diễn ra tương tự ở mẫu xúc tác tổng hợp từ Ni tinh khiết và Ni thu hồi.
3.3.2. Hoạt tính của xúc tác xử lý CO, C3H6 tổng hợp từ Ni thu hồi
Năng lượng hoạt hóa biểu kiến (E) của các quá trình xử lý CO, C3H6 trên các hệ xúc tác điều chế từ muối thu hồi và từ muối thương mại được suy ra từ phương trình biễu diễn mối quan hệ tốc độ phản ứng - nồng độ tác chất và phương trình Arrhenius cùng giả thiết ở độ chuyển hóa thấp, hệ khảo sát xem như thiết bị phản ứng dạng vi phân (differential reactor). Phương pháp tính toán năng lượng hoạt hóa biểu kiến đã được nhóm tác giả trình bày trong nghiên cứu [18].
Năng lượng hoạt hóa biểu kiến (E) được tính toán thông qua phương trình sau:
(7)
Trong đó:
X: Độ chuyển hóa của tác chất ở nhiệt độ T;
a: Bậc phản ứng;
Theo kết quả nghiên cứu của Berlowitz [19] ở nhiệt độ thấp, bậc của CO sẽ có giá trị khoảng gần -1 (do CO hấp phụ rất mạnh lên các tâm kim loại và ngăn cản việc hấp phụ của O2). Khi nhiệt độ đủ cao, CO mới được giải hấp và giải phóng một phần các tâm phục vụ cho việc hấp phụ O2. Theo Berlowitz, bậc CO có thể thay đổi trong khoảng -0,5 đến -1,2 ở các nhiệt độ và tâm kim loại khác nhau.
Trong đó, giá trị bậc -1 của CO chỉ đúng trong khoảng nhiệt độ thấp, cụ thể là 425 - 550oK (tương ứng với nhiệt độ 152 - 277oC) [19]. Nhóm tác giả cũng tiến hành xác định năng lượng hoạt hóa với giá trị bậc phản ứng CO là -1 trong khoảng nhiệt độ 106 - 123oC, tương ứng với độ chuyển hóa < 10%.
Như vậy, phương trình (7) áp dụng cho CO có dạng:
Theo kết quả nghiên cứu của Morooka [20, 21], thông thường bậc của C3H6 dao động từ 0 đến 1 (do giai đoạn chậm nhất quyết định tốc độ phản ứng là giai đoạn hấp phụ propylene). Nghiên cứu của Morooka tiến hành với khoảng nồng độ C3H6 từ 0,2 - 3,5% và độ chuyển hóa dưới 15%. Để tính năng lượng hoạt hóa cho phản ứng oxy hóa propylene, nhóm tác giả tiến hànhkhảo sát trong khoảng nhiệt độ 183 - 228oC tương ứngvới độ chuyển hóa < 15%, bậc phản ứng C3H6 được chọn là 0.
Như vậy, phương trình (7) áp dụng cho C3H6 có dạng:
Dựa trên phương trình 8 và 9, nhóm tác giả xây dựng các đồ thị biểu diễn ln[(1-(1-X)2)/2] theo (1/To - 1/T) và ln(X) theo (1/To - 1/T). Hệ số góc của đồ thị chính là giá trị năng lượng hoạt hóa biểu kiến của quá trình chuyển hóa CO, C3H6 thành CO2 tính ở vùng độ chuyển hóa thấp hơn 10% và 15%.
Ví dụ việc xác định năng lượng hoạt hóa biểu kiến của quá trình khảo sát light-off C3H6 trên xúc tác 20Ni20Mn/ Al - thu hồi được thực hiện như sau:
- Bước 1: Chọn các giá trị nhiệt độ, độ chuyển hóa cho giai đoạn bắt đầu có quá trình oxy hóa C3H6 thành CO2 đến độ chuyển hóa là 15%;
- Bước 2: Tiến hành vẽ đồ thị ln(X) theo (1/To - 1/T) như Hình 6. Giá trị hệ số góc tương ứng với E/R, từ đó tính được năng lượng hoạt hóa (biểu kiến). Hình 9 cũng thể hiện giá trị hệ số xác định bội R2.
Kết quả so sánh hoạt tính xử lý CO và C3H6 của xúc tác 20Ni20Mn/Al - thu hồi và xúc tác 20Ni20Mn/Al – thương mại được trình bày trong Hình 7. Các giá trị năng lượng hoạt hóa biểu kiến của phản ứng oxy hóa CO và C3H6 được thể hiện trong Bảng 4.
|
Hình 6. Ví dụ về đồ thị biểu diễn ln(X)
theo (1/To - 1/T) để xác định năng lượng hoạt hóa quá trình. Hệ số góc
của phương trình hồi quy tương ứng với E/R |
|
Hình 7. Kết quả khảo sát light-off CO,
C3H6 trên 2 mẫu xúc tác sử dụng tiền chất Ni thu hồi(NiMn/Al-TH) và và
sử dụng tiền chất Ni tinh khiết (NiMn/Al-TK). |
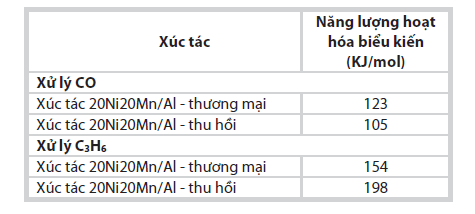
|
Bảng 4. Các giá trị năng lượng hoạt hóa
biểu kiến của 2 mẫu xúc tác 20Ni20Mn/Al -thương mại và xúc tác
20Ni20Mn/Al - thu hồi trong phản ứng oxy hóa CO và C3H6 |
Hình 7 cho thấy khả năng xử lý CO của mẫu xúc tác NiMn/Al-TH điều chế từ muối Ni thu hồi tốt hơn so với xúc tác NiMn/Al-TK điều chế từ muối Ni tinh khiết. Tuy nhiên đối với C3H6, khả năng xử lý của mẫu điều chế từ muối Ni tinh khiết lại tốt hơn so với mẫu điều chế từ muối Ni thu hồi. Tuy nhiên, sự khác biệt giữa 2 mẫu là không lớn. Xét về khả năng chuyển hóa hoàn toàn CO và C3H6, cả hai loại xúc tác đều chuyển hóa trên 90% CO ở nhiệt độ 212oC và trên 90% C3H6 ở nhiệt độ 268oC.
Kết quả tính toán năng lượng hoạt hóa biểu kiến của quá trình oxy hóa hoàn toàn CO, C3H6 thành CO2 tương ứng với mỗi loại xúc tác được trình bày trong Bảng 4.
Năng lượng hoạt hóa biểu kiến trong phản ứng oxy hóa CO của xúc tác điều chế từ muối Ni thu hồi (105KJ/mol) thấp hơn năng lượng hoạt hóa biểu kiến của xúc tác điều chế từ muối Ni tinh khiết (123KJ/mol). Đối với phản ứng oxy hóa C3H6, giá trị năng lượng hoạt hóa có xu hướng ngược lại, năng lượng hoạt hóa biểu kiến của xúc tác điều chế từ muối Ni thu hồi (198KJ/mol) cao hơn năng lượng hoạt hóa biểu kiến của xúc tác điều chế từ muối Ni tinh khiết (154KJ/mol). Đối với cả hai loại xúc tác thì năng lượng hoạt hóa biểu kiến khi oxy hóa CO đều thấp hơn năng lượng hoạt hóa biểu kiến khi xử lý C3H6.
4. Kết luận
Nhóm tác giả đã lựa chọn được các thông số công nghệ phù hợp cho quá trình hòa tách thu hồi kim loại Ni từ xúc tác thải của nhà máy đạm như sau: không đốt cốc, giữ nguyên kích thước hạt ban đầu, không khuấy trộn, nhiệt độ hòa tách 100oC trong 1 giờ, nồng độ acid 1,5M, tỷ lệ xúc tác/acid = 1/20g/ml. Quá trình hòa tách vẫn cho độ thu hồi hơn 90% Ni với độ tinh khiết sản phẩm trên 90% nhưng đơn giản, phù hợp với các đối tượng là xúc tác thải tại Việt Nam hơn so với các quy trình hiện có trên thế giới. Kết quả phân tích hình thái của xúc tác cho thấy xúc tác tổng hợp từ Ni thu hồi có tính chất tương đương với xúc tác tổng hợp từ Ni thương mại. Về hiệu quả xử lý, xúc tác tổng hợp từ muối thu hồi và muối thương mại đều có hoạt tính tốt, nhiệt độ chuyển hóa trên 90% đối với CO, C3H6 ở nhiệt độ 268oC. Năng lượng hoạt hóa biểu kiến trong phản ứng oxy hóa CO của xúc tác điều chế từ muối Ni thu hồi (105KJ/ mol) thấp hơn năng lượng hoạt hóa biểu kiến của xúc tác điều chế từ muối Ni tinh khiết (123KJ/mol). Tuy nhiên, đối với phản ứng oxy hóa C3H6, giá trị năng lượng hoạt hóa có xu hướng ngược lại, năng lượng hoạt hóa biểu kiến của xúc tác điều chế từ muối Ni thu hồi (198KJ/mol) cao hơn năng lượng hoạt hóa biểu kiến của xúc tác điều chế từ muối Ni tinh khiết (154KJ/mol).
Như vậy, việc thu hồi Ni từ xúc tác thải để làm tiền chất tổng hợp xúc tác xử lý khí thải là hướng đi rất tiềm năng nhằm giảm ô nhiễm môi trường đồng thời làm tăng giá trị sử dụng của xúc tác. Điều kiện tiến hành thí nghiệm ảnh hưởng rất lớn đến hiệu quả của quá trình hòa tách, do đó cần lựa chọn các thông số phù hợp nhằm tiết kiệm thời gian, chi phí và năng lượng.
Tài liệu tham khảo
1. Q.Z.Yang, G.J.Qi, H.C.Low, B.Song. Sustainable recovery of nickel from spent hydrogenation catalyst: economics, emissions and wastes assessment. Journal of Cleaner Production. 2011; 19(4): p. 365 - 375.
2. Jin Young Lee, S.Venkateswara Rao, B.Nagaphani Kumar, Dong Jun Kang, B.Ramachandra Reddy. Nickel recovery from spent Raneynickel catalyst through dilute sulfuric acid leaching and soda ash precipitation. Journal of Hazardous Materials. 2010; 176(1 - 3): p. 1122 - 1125.
3. Juferi Idris, Mohibah Musa, Chun-Yang Yin, Ku Halim Ku Hamid. Recovery of nickel from spent catalyst from palm oil hydrogenation process using acidic solutions.Journal of Industrial and Engineering Chemistry. 2010; 16(2): p. 251 - 255.
4. Roberto Giovanini Busnardo, Natalia Giovanini Busnardo, Gustavo Nascimento Salvato, Julio Carlos Afonso. Processing of spent NiMo and CoMo/Al2O3 catalysts via fusion with KHSO4. Journal of Hazardous Materials. 2007; 139(2): p. 391 - 398.
5. Yun Chen, Qiming Feng, Yanhai Shao, Guofan Zhang, Leming Ou, Yiping Lu. Research on the recycling of valuable metals in spent Al2O3-based catalyst. Minerals Engineering. 2006; 19(1): p. 94 - 97.
6. Yi-Chieh Lai, Wen-Jhy Lee, Kuo-Lin Huang, Chung- Mou Wu. Metal recovery from spent hydrodesulfurization catalysts using a combined acid-leaching and electrolysis process. Journal of Hazardous Materials. 2008; 154(1 - 3): p. 588 - 594.
7. Archana Agrawal, D.Bagchi, S.Kumari, V.Kumar, B.D.Pandey. Recovery of nickel powder from copper bleed electrolyte of an Indian copper smelter by electrolysis. Powder Technology. 2007; 177(3): p. 133 - 139.
8. K.Dzulkefly, M.J.Haron, Wen Huei Lim, Chin Chan Woon. Recovery of Nickel from spent hydrogenation catalyst using chelating resin. Journal of Oleo Science. 2002; 51(12): p. 749 - 751.
9. M.Marafi, A.Stanislaus. Spent hydroprocessing catalyst management: A review: Part II. Advances in metal recovery and safe disposal methods. Resources, Conservation and Recycling. 2008; 53(1 - 2): p. 1 - 26.
10. N.M.Al-Mansi, N.M.Abdel Monem. Recovery of nickel oxide from spent catalyst. Waste Management. 2002; 22(1): p. 85 - 90.
11. Yulia Hilli, Niko M.Kinnunen, Mika Suvanto, Auli Savimaki, Kauko Kallinen, Tapani A.Pakkanen. Preparation and characterization of Pd-Ni bimetallic catalysts for CO and C3H6 oxidation under stoichiometric conditions. Applied Catalysis A: General. 2005; 497: p. 85 - 95.
12. C.L.Thomas. Catalytic processes and proven catalysts. Academic Press. 1970: p. 26 - 35.
13. Rachit Oza, Nikhil Shah, Sanjay Patel. Nickel recovery from spent Ni/Al2O3 catalysts using nitric acid solution. Asian Journal of Water, Environment and Pollution. 2011; 8(3): p. 51 - 58.
14. B.Singh. Treatment of spent catalyst from the nitrogenous fertilizer industry - a review of the available methods of regeneration, recovery and disposal. Journal of Hazardous Materials. 2009; 167(1 - 3): p. 24 - 37.
15. Z.Goldstein. Notes on multi-objective decision making. ISDS 440.
16. Nguyễn Cảnh. Quy hoạch thực nghiệm. Nhà xuất bản Đại học Bách khoa Tp. Hồ Chí Minh. 1993.
17. Lê Phúc Nguyên, Bùi Vĩnh Tường, Phạm Tôn Việt Bách, Lương Ngọc Thủy, Nguyễn Thị Minh Hiếu, Nguyễn Quốc Thiết. Nghiên cứu biến tính hệ xúc tác Ni/Al2O3 bằng Mn ứng dụng cho quá trình oxy hóa CO thành CO2. Tạp chí Xúc tác và Hấp phụ. 2013; 2 (2): trang 150 - 156.
18. Lê Phúc Nguyên, Bùi Vĩnh Tường, Nguyễn Hoài Thu, Nguyễn Sura, Lương Ngọc Thủy. Thu hồi Ni trong xúc tác thải để tổng hợp xúc tác xử lý môi trường: Nghiên cứu ảnh hưởng của điều kiện tiền xử lý và ảnh hưởng của hàm lượng Ni trong xúc tác Ni/γ- Al2O3 đến khả năng xử lý CO. Tạp chí Dầu khí. 2015; 1: trang 42 - 51.
19. Paul J.Berlowitz, Charles H.F.Peden, D.Wayne Goodman. Kinetics of CO oxidation on single-crystal Pd, Pt, and Ir. The Journal of Physical Chemistry. 1988; 92(18): p. 5213 - 5221.
20. Yoshihiko Morooka, Atsumu.Ozaki. Regularities in catalytic properties of metal oxides in propylene oxidation. Journal of Catalysis. 1966; 5(1): p. 116 - 124.
21. Yoshihiko Morooka, Atsumu Ozaki. Application of the power rate law to the compensation effect observed in propylene oxidation over metal oxides. Journal of Catalysis.1968; 10(1): p. 84 - 86.
Nickel recovery from spent catalyst of Phu My Fertilizer Plant to prepare environmental catalyst for treatment of CO-C3H6
Le Phuc Nguyen, Nguyen Thi Anh Thu, Luong Ngoc Thuy; Nguyen Van Hieu, Nguyen Hoai Thu, Nguyen Sura - Vietnam Petroleum Institute
Summary
In this study, a very promising way was proposed to recover nickel from spent catalysts of fertilizer plants to synthesise material for exhaust-gas treatment. This method, which was essentially Ni extraction using HNO3 acid, was analysed by investigating the following process parameters: decoking, acid concentration, temperature time of digestion, solid/liquid ratio, particle size and stirring rate. Results showed that under the suitable conditions of leaching, it was possible to achieve a nickel recovery of over 90% with a purity of over 90% in 1 hour. The recovered Ni was then used as a precursor for synthesising the catalysts for treatment of CO-HC. Compared with the catalyst prepared from commercially available nickel nitrate, this material exhibits similar physical properties and perfor- mances. It is feasible to achieve over 90% conversion of CO, C3H6 at 268oC, GHSV > 100.000 h-1.
Key words: CO treatment, spent catalysts, fertilizer plant, Ni, light-off CO.