Tóm tắt
Để thu hồi tối đa năng lượng, phương pháp thiết kế thiết bị khí hóa tầng sôi cho quá trình khí hóa than phụ phẩm đã được thiết lập dựa trên số liệu về động học của phản ứng khí hóa than phụ phẩm thu được từ thực nghiệm kết hợp với mô hình tính toán chiều cao lớp sôi theo thời gian lưu. Các thông số cơ bản của thiết bị tầng sôi cho phản ứng khí hóa than phụ phẩm thu được từ các nghiên cứu trước và các kết quả thu được khi sử dụng phương pháp đề xuất trong nghiên cứu ở lưu lượng dòng đầu vào bằng nhau là khá tương đồng. Tuy nhiên, phương pháp này không thích hợp để tính toán, thiết kế các thiết bị tầng sôi có đường kính trong nhỏ hơn 0,2m. Đối với các thiết bị khí hóa ở quy mô pilot hay quy mô thực tế (có đường kính thiết bị lớn hơn 0,2m) thì phương pháp này có thể tính toán, thiết kế các thông số cơ bản của thiết bị một cách dễ dàng và nhanh chóng hơn so với các phương pháp trước đây trong khi độ chính xác của các thông số là tương đương. Thiết bị khí hóa đã được thiết kế với đường kính trong 1,22m và tổng chiều cao 5,2m. Năng lượng có ích thu được đạt 3.359,52kW (gần 74,83%) với lưu lượng dòng than phụ phẩm đi vào thiết bị khí hóa là 500kg/giờ trong điều kiện vận hành của thiết bị khí hóa ở 850oC và áp suất khí quyển. Giá trị năng lượng thu được có thể sử dụng để phát điện, mở ra hướng mới trong việc tận dụng nguồn phụ phẩm thu được từ quá trình khí hóa sinh khối.
Từ khóa: Thiết kế, than phụ phẩm, khí hóa, tầng sôi, sinh khối, Refgas.
1. Giới thiệu
Nguồn năng lượng sinh khối từ phụ phẩm nông, lâm nghiệp (rơm, trấu, phôi bào, gỗ, xơ dừa, vỏ cà phê, bã mía, thân và lõi ngô, lạc…) được nghiên cứu sử dụng làm nguyên liệu cho quá trình khí hóa. Đây là quá trình sử dụng các tác nhân khí hóa (như không khí, hơi nước hoặc hydro) phản ứng với sinh khối ở nhiệt độ cao để chuyển nhiên liệu từ dạng rắn sang dạng nhiên liệu khí. Nhiên liệu này được gọi chung là khí sinh khối với thành phần chủ yếu là CO, H2, CH4 được dùng làm nhiên liệu khí trong dân dụng, trong công nghiệp hoặc sử dụng làm nguyên liệu cho tổng hợp NH3, CH3OH. Khí sinh khối cũng có thể được sử dụng để phát điện. Sản phẩm của quá trình khí hóa sinh khối gồm chủ yếu là khí tổng hợp (CO + H2) và sản phẩm phụ là tro cùng với than (than phụ phẩm). Các sản phẩm phụ này có thể được sử dụng làm chất độn cho đất để tăng hiệu quả canh tác hoặc sử dụng làm các chất hấp phụ. Để thu được tối đa lượng khí sinh khối để sản xuất điện, có thể sử dụng các sản phẩm phụ này (đặc biệt là
than phụ phẩm với hàm lượng carbon cao) làm nguyên liệu cho quá trình khí hóa thứ cấp. Có nhiều nghiên cứu đã chứng minh công nghệ tầng sôi là công nghệ thích hợp nhất cho quá trình khí hóa sinh khối và than phụ phẩm [1 - 3]. Tuy nhiên, việc tính toán, thiết kế thiết bị tầng sôi rất phức tạp và phụ thuộc vào yêu cầu cụ thể với nguồn nguyên liệu, điều kiện hoạt động và công suất. Do đó, cần xây dựng quy trình tính toán phù hợp với từng trường hợp cụ thể trong thực tế.
2. Phương pháp thiết kế
Quá trình thiết kế thiết bị khí hóa sử dụng số liệu thu được từ quá trình nghiên cứu động học trong tài liệu [4]. Các thông số cần tính toán cho thiết bị khí hóa bao gồm: chiều cao lớp sôi, chiều cao tới hạn thu hồi chất rắn, đường kính thiết bị, tấm phân phối khí và cyclone. Cân bằng vật chất và cân bằng năng lượng cũng được thiết lập để xác định lưu lượng các dòng vào, dòng ra và năng lượng hữu ích thu được từ quá trình khí hóa. Các số liệu ban đầu cho quá trình khí hóa than phụ phẩm được thể hiện trong Bảng 1.
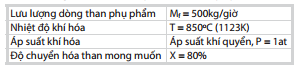 |
Bảng 1. Số liệu ban đầu cho quá trình khí hóa than phụ phẩm |
2.1. Nguyên liệu cho quá trình khí hóa
Nguyên liệu được sử dụng cho quá trình khí hóa thu được từ quá trình khí hóa viên nén rác thải hữu cơ tại Nhà máy Refgas - Vương quốc Anh [5]. Sự phân bố kích thước hạt và dữ liệu về động học của phản ứng khí hóa các phụ phẩm than này được nhóm tác giả tham khảo từ tài liệu [4]. Các tính chất và hình ảnh của than phụ phẩm được thể hiện trong Bảng 2 và Hình 1.
2.2. Cân bằng vật chất và cân bằng năng lượng
Các phản ứng chính:
C + O2 → CO2 (a)
C + H2O → CO + H2 (b)
CO + H2O → CO2 + H2 (c)
Phản ứng (c) xảy ra rất nhanh, đạt cân bằng tức thời nên có thể coi như sản phẩm khí thu được chủ yếu sinh ra từ phản ứng (a) và (b).
Các giả thiết:
Môi trường khí hóa được sử dụng là hỗn hợp hơi nước và không khí với tỷ lệ H2O : không khí = 3:2.
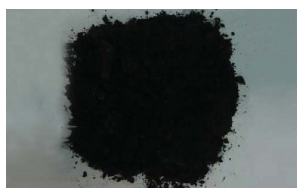 |
Hình 1. Than phụ phẩm thu được từ quá trình khí hóa viên nén sinh khối của Nhà máy Refgas [4] |
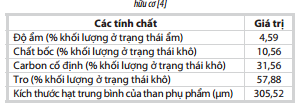 |
Bảng 2. Các tính chất của phụ phẩm than thu được từ quá trình khí hóa viên nén rác thải hữu cơ [4] |
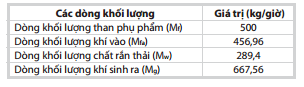 |
Bảng 3. Các dòng vật chất của quá trình khí hóa than phụ phẩm |
Không khí được sử dụng để đốt khoảng 25% lượng carbon trong than phụ phẩm để cấp nhiệt cho phản ứng khí hóa hơi nước với 75% carbon còn lại.
2.2.1. Cân bằng vật chất
Cân bằng dòng vật chất trong thiết bị khí hóa tầng sôi được tính theo công thức sau [1]:
(1)
Trong đó:
Mf: Lưu lượng nguyên liệu than phụ phẩm (kg/giờ);
Mfa: Lưu lượng khí vào (kg/giờ);
Mw: Lưu lượng chất thải rắn (kg/giờ);
Mg: Lưu lượng dòng khí sản phẩm (kg/giờ).
Từ giả thiết trên, các dòng vật chất của quá trình khí hóa than phụ phẩm được tính toán như trong Bảng 3.
2.2.2. Cân bằng năng lượng
Cân bằng năng lượng của quá trình khí hóa được tính theo công thức sau [6]:
(2)
Trong đó:
Echar: Năng lượng than phụ phẩm (kW);
Ea: Năng lượng khí đầu vào sử dụng cho quá trình tạo tầng sôi - khí hóa (kW);
Eg: Năng lượng khí được sinh ra (kW);
El: Năng lượng mất mát (kW).
Các dòng năng lượng của quá trình khí hóa than được tính toán theo các công thức dưới đây.
- Năng lượng than phụ phẩm:
(3)
LHVchar: Nhiệt trị thấp của than phụ phẩm kJ/kg.
- Năng lượng không khí vào sử dụng cho quá trình tạo tầng sôi - khí hóa
Giả sử không khí đi vào thiết bị phản ứng ở nhiệt độ chuẩn là 25oC, thì năng lượng không khí vào sử dụng cho quá trình tạo tầng sôi - khí hóa là Ea = 0.
- Năng lượng chứa trong khí tổng hợp được sinh ra bởi quá trình khí hóa than được xác định theo công thức
sau [1]:
(4)
Trong đó:
Eu: Năng lượng có ích hoặc năng lượng hóa học trong khí sinh ra;
Es: Năng lượng cảm biến trong khí sinh ra.
+ Năng lượng có ích trong khí sinh ra:
(5)
HV9: Nhiệt thấp của khí được sinh ra, kJ/m3
(6)
LHVCO và LHVH2: Nhiệt trị thấp của khí CO và nhiệt trị thấp của khí khí H2 (kJ/m3);
YCO và YH2: Thành phần theo thể tích của khí CO và H2.
+ Năng lượng cảm biến trong khí sinh ra:
(7)
Trong đó:
yi: Nồng độ thể tích của các cấu tử khí trong khí sản phẩm;
Mwi: Khối lượng phân tử của các khí thành phần trong khí sinh ra (kg/kmol);
hi: Entanpi của mỗi cấu tử khí sinh ra ở nhiệt độ ra (kJ/ mol).
- Năng lượng mất mát là năng lượng trong các chất thải rắn và năng lượng trao đổi với môi trường qua thành bình:
(8)
Trong đó:
Ewall : Năng lượng mất mát qua tường (kW);
Ew: Năng lượng chứa trong chất thải (kW).
+ Năng lượng chứa trong chất thải được xác định bởi công thức sau:
(9)
Trong đó:
Ecw: Năng lượng từ carbon không bị đốt cháy (kW);
Eash: Sự mất mát năng lượng bởi nhiệt cảm biến trong các chất thải (kW).
+ Năng lượng từ carbon không bị đốt cháy:
(10)
Trong đó:
LHVcw: Nhiệt trị thấp của carbon (kJ/kg);
hcw: Entapy của carbon ở 850oC (kJ/kg).
+ Năng lượng mất mát từ tro:
(11)
Tash: Nhiệt độ đầu ra của tro (1.123K).
Từ các công thức tính toán các dòng năng lượng, sự cân bằng năng lượng của quá trình khí hóa than phụ phẩm được thể hiện trong Bảng 4.
2.3. Thiết kế thiết bị khí hóa
Để phản ứng khí hóa đạt hiệu quả cao thì nguyên liệu đi vào thiết bị khí hóa cần phải có đủ thời gian để phản ứng xảy ra hoàn toàn. Do đó, thời gian lưu là yếu tố quan trọng trong việc xác định chiều cao đệm. Có thể sử dụng phương pháp thời gian lưu cho quá trình khí hóa than phụ phẩm vì giả thiết rằng quá trình chuyển hóa than phụ phẩm thành khí là quá trình chậm nhất trong các quá trình phản ứng diễn ra trong thiết bị khí hóa sinh khối [7].
Với số liệu thu được từ các nghiên cứu động học quá trình khí hóa than phụ phẩm có thể dễ dàng tính toán được thời gian lưu, từ đó xác định được độ cao đệm và chiều cao thiết bị khí hóa. Mô hình cơ bản của thiết bị tầng sôi được thể hiện trong Hình 2.
Tổng chiều cao của thiết bị khí hóa = Chiều cao đệm (Hbed) + Chiều cao khoảng trống bên trên (Hf )
- Chiều cao đệm Hbed là tỷ lệ giữa thể tích đệm Vbed và diện tích đệm Ao [7]:
(12)
Thể tích đệmVbed (m3) được tính như sau:
(13)
Trong đó:
F[C]: Tốc độ nguyên liệu than phụ phẩm đi vào trong thiết bị khí hóa (kg/giây);
p s: Tỷ trọng của vật liệu đệm (kg/m3)
є: Độ xốp của đệm;
X : Độ chuyển hóa của than phụ phẩm (X = 0,8);
Ө: Thời gian lưu của than phụ phẩm trong tầng sôi hoặc thời gian phản ứng (giây)
Giá trị của độ xốp phụ thuộc vào hình dạng và kích thước của vật liệu đệm. Vật liệu CARBOECONOPROP có tỷ trọng 1.560kg/m3 và đường kính dp = 100 m được lựa chọn làm vật liệu đệm cho thiết bị tầng sôi khí hóa than phụ phẩm [8].
Với đường kính trung bình của hạt vật liệu được lựa chọn dp = 100 m thì thường có giá trị trong khoảng 0,5 - 0,6 [9]. Do đó, nhóm tác giả chọn = 0,55.
|
Bảng 4. Các dòng năng lượng của quá trình khí hóa than phụ phẩm |
- Diện tích mặt cắt ngang bên trong của thiết bị khí hóa tầng sôi Ao (m2) là tỷ lệ giữa tốc độ dòng thể tích Vo (m3/giây) của dòng khí sản phẩm với vận tốc tầng sôi Uo(m/giây) ở cùng nhiệt độ và áp suất vận hành.
(14)
Vo là lưu lượng khí đi qua tấm phân phối khí, có thể sử dụng khối lượng của môi trường khí hóa Mfa (kg/giây) để tính toán Vo.
(15)
Trong đó, ρg là tỷ trọng của môi trường ở nhiệt độ và áp suất vận hành của thiết bị khí hóa (kg/m3).
|
Hình 2. Chiều cao của thiết bị tầng sôi
[9]: Hbed là chiều cao đệm, Hf là chiều cao khoảng không bên trên đệm,
TDH là chiều cao tới hạn thu hồi chất rắn, Dt là đường kính trong của
thiết bị |
|
Hình 3. Phân loại hạt theo Geldart [9] |
Giá trị vận tốc khí bề mặt hay vận tốc tầng sôi phụ thuộc vào phân loại các hạt sử dụng làm vật liệu đệm cho thiết bị tầng sôi. Từ việc xác định được phân loại hạt (Hình 2) vật liệu đệm, có thể dựa vào các dữ liệu thực tế để lựa chọn giá trị Uo cho phù hợp.
Với việc lựa chọn vật liệu CARBOECONOPROP có tỷ trọng 1.560kg/m3 và đường kính dp = 100μm, thì các hạt vật liệu này thuộc phân nhóm các hạt Geldart A. Vận tốc khí bề mặt Uo đối với phân nhóm hạt này thường có giá trị từ 0,3 - 2m/giây [9]. Do đó, chọn Uo = 0,92m/giây.
- Thời gian lưu θ được tính theo công thức sau:
(16)
Trong đó:
Co: Lượng carbon ban đầu trong phân tử sinh khối (kg);
X: Sự chuyển hóa carbon yêu cầu (-);
r: Tốc độ phản ứng khí hóa hơi nước (s-1).
Tốc độ của phản ứng khí hóa được tính toán dựa trên mô hình động học thu được từ tài liệu [4]
(17)
Với độ chuyển hóa X = 80% và Hn = 0,6at sẽ tính toán được các giá trị của k và n, từ đó xác định được tốc độ phản ứng và thời gian lưu.
- Chiều cao khoảng không bên trên đệm Hf
Các hạt than phụ phẩm mịn không bị chuyển hóa từ lớp sôi bị cuốn theo là nguyên nhân chính làm giảm lượng carbon. Khoảng trống bên trên đệm cho phép các hạt bị cuốn theo rơi trở lại. Chiều cao khoảng trống phải thích hợp để cung cấp thời gian lưu cho quá trình chuyển hóa than phụ phẩm (có thể được xác định từ thực nghiệm hoặc thông qua mô hình động học). Tuy nhiên, chiều cao khoảng trống không nên vượt quá chiều cao tới hạn để thu hồi chất rắn (transport disengaging height - TDH) bởi không có quá trình khử sâu hơn trong sự cuốn theo [7].
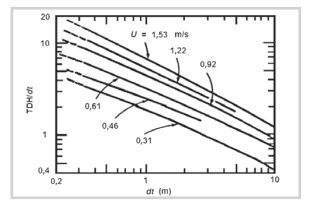 |
Hình 4. Mối liên hệ giữa đường kính trong
của thiết bị khí hóa tầng sôi, vận tốc khí bề mặt và chiều cao tới hạn
thu hồi chất rắn TDH [9] |
TDH phụ thuộc vào đường kính trong của thiết bị khí hóa và vận tốc khí bề mặt hay vận tốc tầng sôi Uo. Phương pháp đơn giản để xác định giá trị TDH là dựa vào các giá trị thu được từ thực nghiệm được thể hiện trong Hình 4 [9].
2.4. Thiết kế tấm phân phối khí
Thiết bị phân phối khí có thể được thiết kế trực tiếp theo lý thuyết vòi phun, nếu độ giảm áp vòi phun chỉ là một phần nhỏ so với độ giảm áp tổng thì tấm phân phối khí có thể được thiết kế theo các bước sau [9]:
- Bước 1: Xác định độ giảm áp cần thiết qua thiết bị phân phối khí Δpd, theo công thức sau:
(18)
Δpb Độ giảm áp qua đệm
Theo hệ SI, Δpb được tính theo công thức sau:
(19)
- Bước 2: Tính chuẩn số Reynolds, Ret = dtuoρg/μ, đối với lưu lượng tổng áp dụng cho thiết bị phân phối khí và chọn giá trị thích hợp cho hệ số phun, Cd,or.
- Bước 3: Xác định vận tốc khí qua vòi phun.
(20)
Tỷ lệ uo/uor thể hiện phần diện tích mở trong tấm phân phối khí. Giá trị này thường nhỏ hơn 10%.
- Bước 4: Xác định Nor, số lượng lỗ phun khí trên diện tích thiết bị phân phối khí, đường kính lỗ phun khí dor được tìm thông qua công thức sau:
(21)
|
Bảng 5. Giá trị hệ số phun theo chuẩn số Reynolds |
2.5. Thiết kế cyclone
Cyclone được tính toán theo phương pháp chọn như trong nghiên cứu [10].
- Đường kính D(m) của cyclone được xác định theo công thức:
(22)
Trong đó:
V: Lưu lượng khí đi vào cyclone (m3/giây);
wq: Tốc độ quy ước (m/giây).
- Tốc độ quy ước được xác định theo công thức:
(23)
Trong đó:
Δp: Trở lực của cyclone (N/m2);
pk : Khối lượng riêng của khí (kg/m3);
ζ: Hệ số trở lực phụ thuộc vào kiểu cyclone.
Thường lấy tốc độ quy ước: wq = 2,2 - 2,5m/giây. Chọn wq = 2,35m/giây.
Với đường kính cyclone tính toán được, lựa chọn dạng cyclone để tính toán, thiết kế các thông số khác cho cyclone.
3. Kết quả và thảo luận
- Các thông số cơ bản của thiết bị tầng sôi cho phản ứng khí hóa than phụ phẩm được thể hiện ở Bảng 6.
Các thông số cơ bản của thiết bị tầng sôi khí hóa dòng than phụ phẩm có lưu lượng dòng vào là 500kg/giờ gồm: chiều cao đệm ~ 0,35m, tổng chiều cao thiết bị 5,2m; đường kính thiết bị 1,22m.
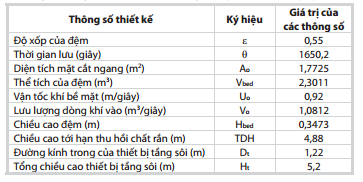 |
Bảng 6. Các thông số thiết kế cơ bản của thiết bị tầng sôi cho quá trình khí hóa than phụ phẩm |
|
Bảng 7. So sánh kết quả tính toán các
thông số cơ bản của thiết bị tầng sôi cho phản ứng khí hóa thanphụ phẩm
bằng phương pháp đề xuất trong nghiên cứu với các nghiên cứu trước |
Nhóm tác giả đã sử dụng phương pháp được đề xuất trong nghiên cứu để tính toán, so sánh các thông số cơ bản cho thiết bị tầng sôi khí hóa than phụ phẩm với lưu lượng dòng đầu vào của một số nghiên cứu trước đó (Bảng 7).
Bảng 7 cho thấy các thông số cơ bản của thiết bị tầng sôi cho phản ứng khí hóa than phụ phẩm thu được từ các nghiên cứu trước và các kết quả thu được khi sử dụng phương pháp đề xuất trong nghiên cứu ở lưu lượng dòng đầu vào bằng nhau khá tương đồng (gồm các số liệu về kích thước thiết bị và năng lượng thu được khi khí hóa than phụ phẩm). Tuy nhiên, phương pháp này không tính toán được chiều cao của thiết bị khi đường kính của thiết bị đó nhỏ hơn 0,2m (chiều cao thiết bị tính toán dựa theo đồ thị Hình 3). Do đó, không thể sử dụng phương pháp này để tính toán cho các thiết bị tầng sôi có lưu lượng dòng vào quá nhỏ (Bảng 7).
|
Bảng 8. Các thông số thiết kế của tấm phân phối khí |
|
Bảng 9. Số lượng và kích thước lỗ phun khí
|
|
Bảng 10. Lựa chọn các thông số thiết kế của cyclone theo đường kính trong |
Đối với các thiết bị khí hóa ở quy mô pilot hay quy mô thực tế có đường kính thiết bị lớn hơn 0,2m thì có thể sử dụng phương pháp này để tính toán, thiết kế các thông số cơ bản cho thiết bị [12]. Hiện nay, đã có nhiều nghiên cứu về quá trình khí hóa trên thiết bị tầng sôi với nguyên liệu là sinh khối ở cả quy mô phòng thí nghiệm và quy mô pilot [1].
- Tấm phân phối khí của thiết bị khí hóa được thiết kế với các thông số trong Bảng 8.
Với:
, số lượng và kích thước lỗ phun khí được đưa ra trong Bảng 9.
Các lỗ phun khí nếu quá nhỏ có thể gây ra trở lực, nếu quá lớn có thể gây ra sự phân phối khí không đồng đều. Trong trường hợp này, nhóm tác giả chọn dor = 0,001m và Nor = 20.400/m2 (hay dor = 1mm và Nor ~ 2/cm2).
- Thiết kế kiểu cyclone ЦH-15 được nhóm tác giả lựa chọn cho thiết bị tầng sôi,
xác định theo đường kính trong như Bảng 10.
4. Kết luận
Thông qua thời gian lưu, nhóm tác giả đã thiết lập được phương pháp mới để tính toán, thiết kế các thông số cơ bản của thiết bị tầng sôi cho quá trình khí hóa than phụ phẩm thu được từ quá trình khí hóa viên nén hữu cơ của Nhà máy Refgas, Vương quốc Anh. Đối với các thiết bị khí hóa ở quy mô pilot hay quy mô thực tế (có đường kính thiết bị > 0,2m) có thể sử dụng phương pháp này để tính toán, thiết kế các thông số cơ bản của thiết bị một cách dễ dàng và nhanh hơn so với các phương pháp trước đây trong khi độ chính xác của các thông số là tương đương.
Với dòng nguyên liệu than phụ phẩm là 500kg/giờ, năng lượng hữu ích thu được từ quá trình khí hóa nguyên liệu lên tới 3.359,52kW (74,83%). Nguồn năng lượng này có thể được sử dụng để phát điện với quy mô nhỏ. Nếu nâng cao công suất thiết bị thì năng lượng thu được có thể được sử dụng ở quy mô công nghiệp.
Tài liệu tham khảo
1.J.J.Ramírez, J.D.Martínez, S.L.Petro. Basic design of a fluidized bed gasifier for rice husk on a pilot scale. Latin American Applied Research. 2007; 37(4): p. 299 - 306.
2.. Harish Jagat Pant, V.K.Sharma, M.Vidya Kamudu, S.G.Prakash, S.Krishanamoorthy, G.Anandam, P.Seshubabu Rao, N.V.S.Ramani, Gursharan Singh, R.R.Sonde. Investigation of flow behaviour of coal particles in a pilot- scale fluidized bed gasifier (FBG) using radiotracer technique. Applied Radiation and Isotopes. 2009; 67(9): p. 1609 - 1615.
3. Fudong Ju, Hanping Chen, Haiping Yang, Xianhua Wang, Shihong Zhang, Dechang Liu. Experimental study of a commercial circulated fluidized bed coal gasifier. Fuel Processing Technology. 2010; 91(8): p. 818 - 822.
4. Le Dinh Chien. Gasification of biomass: An investigation of key challenges to advance acceptance of the technology. PhD thesis, University of Bath, United
Kingdom. 2012.
5. Refgas. www.refgas-uk.com.
6. S.Septien, F.J.Escudero Sanz, S.Salvador, S.Valin. Steam gasification of char from wood chips fast pyrolysis: Development of a semi-empirical model for a fluidized bed reactor application. Biomass and Bioenergy. 2015; 77: p. 64 - 74.
7. Prabir Basu. Biomass gasification and pyrolysis: Practical design and theory. 2010.
8. CARBO Ceramics Inc. www.carboceramics.com.
9. D.Kunii, O.Levenspiel. Fluidization engineering (2nd edition). Butterworth-Heinemann. 1991.
10. Trần Xoa, Nguyễn Trọng Khuông, Hồ Lê Viên. Sổ tay quá trình và thiết bị công nghệ hóa chất (Tập 1). Nhà xuất bản Khoa học và Kỹ thuật.
11. Byungho Song, Xueyan Zhu, Woongsig Moon, WonYang. Steam gasification of low rank coal chars in a thermobalance reactor and a fluidized bed reactor. 13th International Conference on Fluidization - New Paradigm in Fluidization Engineering, Gyeong-ju, Korea. 16 - 21 May, 2010.
12. Colomba Di Blasi. Combustion and gasification rates of lignocellulosic chars. Progress in Energy and Combustion Science. 2009; 35(2): p. 121 - 140.
A new approach to design a commercial-scale bubbling fluidised- bed gasifier to gasify char derived from a gasification plant
Nguyen Van Luc (1), Le Dinh Chien (2)
1. Technical Instrument and Consultant Technology JSC
2. University of Mining and Geology
Summary
To maximise energy recovery, a methodology for designing a bubbling fluidised-bed gasifier to gasify the char was established based on a combination of experimental kinetic data of gasification reactions on the char particles and the residence-time-design method to determine the bed height. The principal parameters of the fuidised-bed gas- ifier for char gasification reaction drawn from previous researches and the results collected when using the method proposed in the current research at the same input flowrate are quite similar. However, this method is not suitable to calculate and design fluidised-bed gasifier with diameter of less than 0.2m. For pilot-scale or full-scale fluidised-bed gasifier (with diameter of over 0.2m), this method can design the principal parameters of the equipment more easily and quicker than previous methods with a similar level of accuracy. For a flowrate of 500kg char per hour, a bubbling fluidised-bed gasifier with height of 5.2m and diameter of 1.22m was chosen, with a power output of 3,359.52kW (~ 74.83% ) at an operating condition of 850oC and atmospheric pressure. The obtained energy value can be used to generate electricity to increase the overall efficiency of a biomass gasification process.
Key words: Design, char, gasification, fluidised-bed, biomass, Refgas.