Summary
Ca Voi Xanh gas field is located about 100km off the coast of the central region of Vietnam. This is the biggest gas field in Vietnam with its reserves of 150 billion m3 of natural gas. However, gas from Ca Voi Xanh field has high contents of impurities, namely H2S, CO2 and N2. Orientations for treatment and deep processing of Ca Voi Xanh gas are presented, including membrane separation of CO2 and/ or N2; and processing of Ca Voi Xanh gas without CO2 and/or N2 removal to produce (i) syngas for methanol feed via combined reforming technology and/or (ii) ammoniaforfertilizer via Haberprocess. Recovered CO2 canbeconsideredasapotentialcarbonsupplytomethanol and DMEproduction if a sustainable andreasonablesource of hydrogen is supplied.
Developmentofadvancedmaterialsandcatalystsfor efficient processing of Ca Voi Xanh gas is discussed. It is highly expected that zeolite-based membranewould offer a techno-economically good approach of CO2 and/or N2 removal from a mixture of CH4, CO2, and/or N2, and that nano-Ni-based catalyst brings a high conversion of methane (> 90%) towards lower temperature (550oC) in comparison with current industrial conditions for methane reforming.
Key words: Ca Voi Xanh, CO2, DME, membrane, methanol, N2, steam reforming.
1. Introduction on Ca Voi Xanh gas field
Vietnam is in the region of high-CO2-content gas fields. In 2011, the biggest gas field, named Ca Voi Xanh, was discovered about 100km off the coast of the central region of Vietnam with its reserves of 150 billion m3 of natural gas. It is scheduled to have first gas in 2023 and its gas will be used for power and petrochemical production. However, Ca Voi Xanh gas has high contents of impurities, namely H2S, CO2 and N2. Table 1 shows its hydrocarbon and non-hydrocarbon composition [1].
It can be seen that Ca Voi Xanh gas contains undesired components, including 0.21% of H2S, 9.88% of N2 and 30.26% of CO2. At the gas processing plant (GPP), H2S removal treatment is applied so that its remaining H2S content is less than 30ppm. CO2 and/or N2 removal should be considered upon its uses and available technologies for its treatment and deep processing.
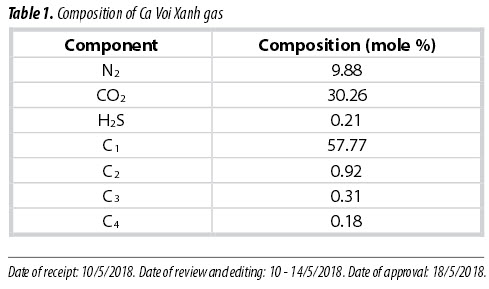
Ca Voi Xanh gas is planned to be used for power production in priority. About 10 - 20% of produced gas could be considered for petrochemical production. In 2017, the Vietnam Petroleum Institute (VPI) conducted a study to evaluate the ability to use Ca Voi Xanh gas as feedstock for petrochemicals. It was shown that the best option to use Ca Voi Xanh gas for petrochemical production is to produce olefins via methanol production. Olefins can then be used to produce other products, including polypropylene (PP), methyl methacrylate (MMA), and styrene monomer (SM). Figure 1 shows two options for petrochemical production from Ca Voi Xanh gas.
2. Orientations for treatment and deep processing of Ca Voi Xanh gas
CO2 and/or N2 removal from Ca Voi Xanh gas using membrane technology
For CO2 removal from Ca Voi Xanh gas, a membrane technology can be applied. Membrane separation offers the advantage of being highly impact, environmental friendly, scale-up flexible, and energy efficient relative to the more established gas separation processes such as adsorption and cryogenic distillation, and thus has been focused as subject of investigation for gas separation for years [3]. In the gas industry, some commercial
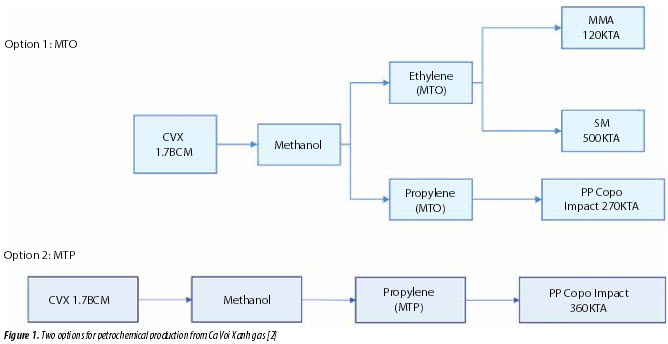
technologies are available for CO2 removal using polymer- based membranes. Table 2 shows selected suppliers of membrane natural gas separation systems [3]. Currently, commercial polymeric materials can bring a selectivity of about 10 - 20% for separation of CO2 from natural gas [3].
Although polymeric membranes have been commercialised for gas separation, they show a number of disadvantages, clean feed requirement, selectivity- permeability trade-off (upper bound), physical aging and plasticisation in exposure to harsh working conditions and acidic gas contaminants. On the other hand, for N2 removal, current technology based on cryogenic separation is energy consuming. Membrane technology for N2 removal is currently not available in the gas industry. The challenge is to develop membranes with the necessary performance related to permselectivity of N2 over CH4 with closely matched dynamic diameters of 0.36 and 0.38nm, respectively. A polymeric membrane has been tested for N2 removal, but its selectivity is relatively low (0.3). Ceramic membranes are being developed for higher efficiency in gas separation. A zeolite-based membrane can bring a selectivity of more than 200 for CO2 removal, and/or 10 - 20 for N2 removal from natural gas. Table 3 shows the strength and weaknesses of polymer membranes and inorganic membranes (mainly zeolite membranes) for gas separation.
To date, some inorganic membranes have shown excellent performance in CO2 separation as well as exhibited potentially good performance in N2 separation.
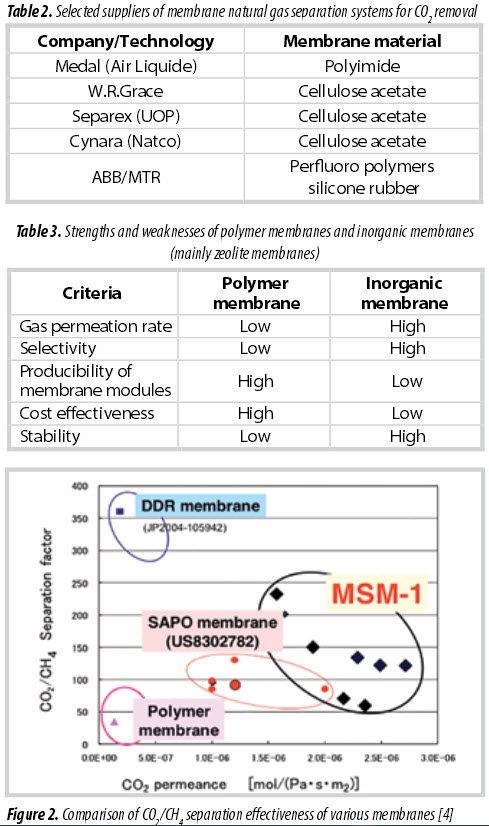
Chiyoda Corporationand Mitsubishi Chemical Corporation have collaborated to develop a zeolite-based membrane for CO2 removal from natural gas and named it MSM-1. Figure 2 shows a comparison of CO2/CH4 separation effectiveness of various membranes. The outstanding performance of zeolite-based membranes compared to polymeric ones can be seen.
However, the current cost for zeolite-based membrane production is quite expensive, and hence, preventing their commercialisation. A more realistic approach is to develop a hybrid membrane based on a mixture of polymer and zeolite. Although a lot of works still need to be done to bring hybrid membranes to the market, this is a potential way to have highly efficient membranes for gas treatment.
Methanol and/or dimethylether (DME) production from high-CO2-content natural gas Ca Voi Xanh gas can be processed without CO2 removal using a steam reforming process to produce syngas (a mixture of CO and H2) that can be later converted into methanol and/or DME. Currently, DME is produced via dehydration of methanol as feedstock [5]. Several licensors are available for DME production, including Haldor Topsoe, Linde/Lurgi, and Toyo Engineering, etc. Another under development technology is one-stage DME production via catalytic conversion of syngas or CO2. Accordingly, the catalyst should have both methanol synthesis and methanol dehydration activities. As a result, an amount of water is formed during DME synthesis, and hence, an efficient water removal technology should be applied.
The CO2 content in Ca Voi Xanh gas brings two sides during processing. In fact, CO2 is needed for methanol synthesis, but at the same time, it also results in more coke formation during the reforming reaction. In 2014, Haldor Topsoe introduced a noble metal based catalyst for steam reforming of high-CO2-content natural gas. Application of this catalyst can reduce the steam amount needed to prevent a high coke formation during the reaction. Its pilot test was performed with time on stream of 490 hours.
Severalstudieshavebeenbeingcarriedouttodevelop new catalysts that can be applied for steam reforming of natural gas at a considerably lower temperature, just about 550oC. Chihaia et al. showed that steam reforming of methane could be achieved with the methane conversion of 82% over Ni/CeO2-Al2O3 catalyst at 550oC [6]. Currently, VPI is developing a nano-Ni-based catalyst
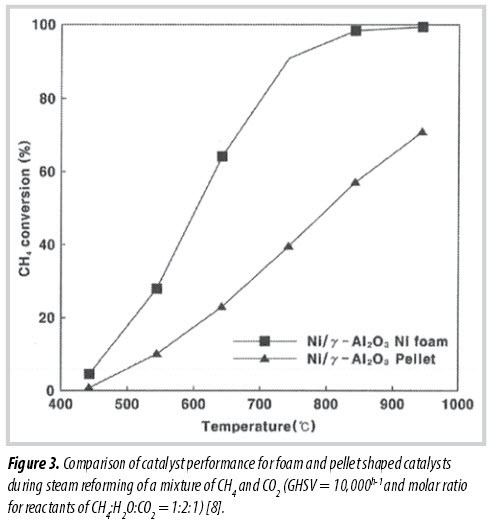
that brings a high conversion of methane (> 90%) under lower temperature (550oC) in comparison with current industrial conditions for methane reforming.
On the other hand, an integration of structured materials into catalysts for methane steam reforming has also been conducted to enhance the quality of mass and heat transfers inside the reactor, leading to a reduced reactor size or lower reaction temperature. Moon et al. showed that application of foam material into Ni-based catalyst for steam reforming of a mixture of CH4 and CO2 could bring a higher conversion of methane than that of conventional catalyst pellet under the same reaction conditions [7]. Figure 3 shows a comparison of catalyst performance for foam and pellet shaped catalysts during steam reforming of a mixture of CH4 and CO2. Therefore, application of advanced catalysts could bring high potential to improve energy efficiency during the steam reforming of high-CO2-content natural gas.
Co-production of methanol and NH3 from natural gas containing CO2 and N2
Another approach to use Ca Voi Xanh gas for petrochemical production is to produce methanol and NH3. In this case, neither CO2 nor N2 removal is required. N2 is reacted with part of H2 in the syngas to produce NH3, and a mixture of CO, CO2 and remaining H2 is a feedstock for methanol production. However, further study needs to be conducted to evaluate the facileness of NH3 formation under this condition.
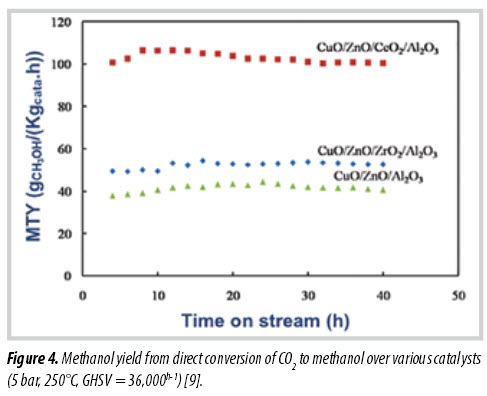
Recovered CO2 for methanol and/or dimethylether (DME) production
In the case that CO2 is removed from Ca Voi Xanh gas, CO2 could be considered as a potential carbon supply for methanol and DME production via CO2 hydrogenation into methanol, and then, followed by methanol dehydration for DME. A one-stage technology is under development for direct DME production from CO2.
In 2012, VPI conducted a study to develop new catalyst and apply membrane reactor for methanol production from CO2 to improve its methanol yield. Figure 4 shows methanol yield from direct conversion of CO2 over various catalysts. As a result, Cu-Zn-Ce-Al based catalyst and NaA based membrane reactor have been found to increase the methanol yield more than 1.5 - 1.7 times compared to the conventional catalyst and reactor for methanol synthesis [9]. A highlight was pointed out that this process only brings profits if a sustainable and reasonable source of hydrogen is supplied. Electrolysation of water using renewable energy could bring a good supply of hydrogen. This direction is highly potential for Vietnam because of its advantages in solar power production [10].
3. Conclusions
Ca Voi Xanh gas contains high contents of impurities, namely H2S, CO2 and N2. Orientations for treatment and deep processing of Ca Voi Xanh gas include (1) CO2 and/ or N2 removal using membrane technology; and (2) bi- reforming of Ca Voi Xanh gas to produce NH3 and/or syngas that can then be used as feedstock for methanol production. Recovered CO2 can be considered as a potentialcarbonsupplyformethanoland DMEproduction if a sustainable and reasonable source of hydrogen is supplied. Development of new materials and catalysts brings opportunities for efficient processing of Ca Voi Xanh gas. It has been found that zeolite-based membrane creates a good separation of CO2 and/or N2 from a mixture of CH4, CO2, and/or N2, and that nano-Ni-based catalyst brings a high conversion of methane (> 90%) under lower temperature (550oC) in comparison with current industrial conditions for methane reforming.
References
1. ExxonMobil, PVN, PVEP. PSC Blocks 117-119, Outline Development Plan (ODP) Summary. 2016.
2. VPI. Study on the ability to integrate Ca Voi Xanh gas into Dung Quat Refinery for fuel use, hydrogen production, and petrochemical production. 2018.
3. Richard W.Baker, Kaaeid Lokhandwala. Natural gas processing with membranes: An overview. Industrial Engineering Chemistry Research. 2008; 47(7): p. 2109 - 2121.
4. Chiyoda Corporation, Mitsubishi Chemical Corporation. Novel CO2 separation technology using MSM-1 zeolite membrane. JOGMEC Techno Forum. 27 November, 2014.
5. Enrico Catizzone, Giuseppe Bonura, Massimo Migliori, Francesco Frusteri, Girolamo Giordano. CO2 recyclingtodimethylether: State-of-the-artandperspectives. Molecules. 2018; 23(1).
6. Monica Dan, Maria Mihet, Alexandru R.Biris, Petru Marginean, Valer Almasan, George Borodi, Fumiya Watanabe, Alexandru S.Biris, Mihaela D.Lazar. Supported nickel catalysts for low temperature methane steam reforming: Comparison between metal additives and support modification. Reaction Kinetics, Mechanisms and Catalysis. 2012; 105(1): p. 173 - 193.
7. Daeil Park, Dong Ju Moon, Taegyu Kim. Steam-CO2 reforming ofmethaneon Ni/-Al2O3-deposited metallicfoam catalyst for GTL-FPSO process. Fuel Processing Technology. 2013; 112: p. 28 - 34.
8. Kee Young Koo, Hyun Ji Eom, Un Ho Jung, Wang Lai Yoon. Ni nanosheet-coated monolith catalyst with high performance for hydrogen production via natural gas steam reforming. 2016; 525: p. 103 - 109.
9. VPI. Study on the ability to apply membrane reactor and new catalyst to enhance the methanol yield during CO2 hydrogenation. 2014.
10. GreenID. Analysis of future generation capacity scenarios for Vietnam. 2017.