Tóm tắt
Bài báo đánh giá nguyên nhân và giải pháp cho hiện tượng suy giảm hệ số sản phẩm (Productivity Index - PI) trong quá trình bơm ép nước đối với một giếng khai thác từ tầng móng ngoài khơi bờ biển Việt Nam do Viện Dầu khí Việt Nam (VPI) nghiên cứu. Hiện tượng sa lắng muối vô cơ tại khu vực cận đáy giếng và đáy giếng đã được đánh giá bằng phần mềm chuyên dụng ScaleChem 9.2 và các thiết bị thí nghiệm mô phỏng mô hình vỉa ở điều kiện áp suất cao, nhiệt độ cao. Sự phối trộn không tương thích giữa nước bơm ép và nước từ dung dịch khoan là nguyên nhân chính gây ra hiện tượng sa lắng (chủ yếu là CaSO4) và suy giảm hệ số sản phẩm. Dựa trên thành phần và hàm lượng cặn sa lắng, nghiên cứu đã đưa ra giải pháp để loại bỏ sa lắng và phục hồi hệ số sản phẩm, nâng cao hiệu quả khai thác.
Từ khóa: Sa lắng muối, bơm ép, dung dịch khoan.
1. Giới thiệu
Trong quá trình khoan và hoàn thiện giếng khai thác ở tầng móng có độ sâu lớn, thông thường sử dụng các dung dịch khoan có tỷ trọng lớn chứa hàm lượng CaCl2, CaBr2 cao. Một lượng rất lớn dung dịch khoan sẽ được bơm vào vỉa và có thể không được thu hồi lại. Lượng dung dịch khoan không thu hồi được này sẽ nằm lại tại khu vực cận đáy giếng của các giếng khai thác. Sau một thời gian khai thác khi áp suất vỉa bắt đầu sụt giảm nếu không có sự hỗ trợ của nước thành hệ, cần phải tiến hành bơm ép nước vào vỉa để duy trì áp suất.
Nước biển thường được sử dụng làm nước bơm ép để duy trì áp suất vỉa và nâng cao hiệu quả trong giai đoạn khai thác. Tuy nhiên, việc sử dụng bơm ép nước có thể hình thành sa lắng muối vô cơ tại khu vực cận đáy giếng và đáy giếng của giếng khai thác dẫn đến bít nhét các kênh dẫn và làm giảm hệ số sản phẩm. Có 2 nguyên nhân chính gây ra sa lắng [1]:
- Sa lắng do sự thay đổi áp suất, nhiệt độ từ trong vỉa đến đáy giếng khai thác;
- Sa lắng do tương tác không tương thích giữa nước bơm ép và nước vỉa (nước vỉa nội tại hoặc nước từ quá trình mất dung dịch khoan).
Sự sụt giảm hệ số sản phẩm trong quá trình bơm ép nước đã xảy ra tại mỏ SCL, bể Cửu Long, thềm lục địa Việt Nam. Giếng 1P-SCL là giếng khai thác chính của mỏ SCL và khai thác từ tầng móng. Dung dịch CaCl2 (hàm lượng Cl- 200.000mg/L) đã được sử dụng đưa vào dung dịch khoan với lượng mất dung dịch khoan không thể thu hồi khoảng thùng. Sau một thời gian khai thác, áp suất vỉa giảm dần, nước biển được bơm ép vào mỏ SCL. Độ ngập nước (watercut) của giếng 1P-SCL trong thời gian đầu khai thác khá thấp và đột ngột tăng mạnh (bắt đầu xảy ra hiện tượng nước xâm nhập) sau khoảng 2 năm kể từ thời điểm bắt đầu bơm ép nước. Đồng thời, giá trị PI cũng giảm mạnh 50% chỉ sau 6 tháng. Vấn đề sa lắng muối vô cơ tại khu vực đáy giếng đã được đặt ra và nghiên cứu để tìm giải pháp phục hồi hệ số sản phẩm.
Trên cơ sở đó, Trung tâm Nghiên cứu Tìm kiếm Thăm dò và Khai thác Dầu khí (EPC), Viện Dầu khí Việt Nam đã sử dụng phần mềm ScaleChem 9.2 và thiết bị thí nghiệm mô phỏng mô hình vỉa ở điều kiện nhiệt độ cao, áp suất cao để nghiên cứu đánh giá thành phần cặn sa lắng và hàm lượng muối sa lắng, từ đó đưa ra các giải pháp hiệu quả để phục hồi hệ số sản phẩm, nâng cao hiệu quả khai thác.
2. Thành phần nước khai thác của giếng 1P-SCL
Giếng 1P-SCL được đưa vào khai thác với áp suất vỉa thời gian đầu khoảng 7.200psi và độ ngập nước rất thấp (dưới 3%). Sau 5 năm, áp suất vỉa giảm liên tục còn 5.600psi chứng tỏ áp suất vỉa hầu như không được hỗ trợ bởi tầng chứa nước trong vỉa. Mặt khác, phân tích thành phần nước khai thác của giếng 1P-SCL cho thấy thời gian đầu hàm lượng ion Cl- rất cao, sau đó giảm dần khi bắt đầu có hiện tượng nước xâm nhập. Giếng 1P-SCL được khai thác tại tầng móng nơi có độ sâu hơn 4.000m nên trong quá trình khoan và hoàn thiện giếng đã sử dụng dung dịch khoan tỷ trọng cao có thành phần chủ yếu là CaCl2, với hàm lượng Cl rất cao (200.000mg/L). Như vậy, có thể thấy khả năng nước khai thác của giếng 1P-SCL trong thời gian đầu chính là nước mất từ dung dịch khoan và không tồn tại nước vỉa nguyên sinh của giếng 1P-SCL. So sánh với kết quả phân tích hàm lượng tổng rắn hòa tan TDS của giếng 1P-SCL với nước vỉa tầng móng các vỉa khu vực lân cận cũng khẳng định điều này. Theo đó, nếu tầng móng thực sự tồn tại nước vỉa thì giá trị TDS thường không cao quá 40.000mg/L, tuy nhiên thời gian đầu nước khai thác của 1P-SCL lên đến trên 90.000mg/L.
Sau khi bơm ép nước được 2 năm, hàm lượng ion Cl- trong nước vỉa giảm dần (Hình 1), đồng thời độ ngập nước tăng đột biến. Như vậy, sau 2 năm bơm ép nước bắt đầu có hiện tượng xâm nhập tại giếng 1P-SCL. Sau thời điểm này, nước bơm ép sẽ phối trộn với lượng nước từ quá trình mất dung dịch khoan còn lại (khoảng 25.000 thùng) làm cho hàm lượng ion Cl- giảm dần cho đến khi không còn nước mất từ dung dịch khoan.
Đặc biệt ion Cl- thường được sử dụng như một chất đánh dấu tự nhiên trong việc xác định nguồn gốc nước khai thác [2]. Ở trạng
thái ion, khi đi vào vỉa, hàm lượng Cl- hầu như không bị thay đổi do tương tác đất đá và nước mà chỉ bị thay đổi khi có sự phối trộn với một nguồn nước có hàm lượng Cl khác biệt. Sử dụng hàm lượng ion Cl- trong thành phần nước khai thác có thể tính toán tỷ lệ phối trộn giữa nước bơm ép (nước biển có hàm lượng Cl- khoảng 19.000 - 20.000mg/L) và nước từ quá trình mất dung dịch khoan (có hàm lượng Cl- 200.000mg/L).
Theo dữ liệu phân tích thành phần nước vỉa, các mẫu nước của giếng 1P-SCL sau thời điểm nước xâm nhập, hàm lượng ion Cl- giảm nhanh và sau đó giữ ổn định ở khoảng 30.000mg/L trong thời gian tương đối dài khoảng 15 tháng, tương ứng với khoảng thời gian độ ngập nước ổn định và giữ ở mức cao. Tính toán cho thấy, tỷ lệ phối trộn của nước bơm ép với nước từ quá trình mất dung dịch trong khoảng thời gian này là khoảng 95:5. Tỷ lệ này là phù hợp với lượng nước từ quá trình mất dung dịch khoan còn lại trên tổng số nước khai thác trong thời gian này.
3. Cơ chế sa lắng muối chính và nguyên nhân
Qua phân tích thành phần nước khai thác và nước từ quá trình mất dung dịch khoan như trên, có thể thấy hiện tượng sa lắng muối xảy ra tại đáy giếng khai thác 1P-SCL theo 2 nguyên nhân chính sau:
- Sự phối trộn không tương thích giữa nước bơm ép (nước biển) và nước từ quá trình mất dung dịch khoan:
Nước biển chứa hàm lượng ion SO4 rất cao (khoảng 2.500mg/L), khi gặp nước mất từ dung dịch khoan với bản chất là dung dịch CaCl2 với hàm lượng Ca cao, sẽ hình thành muối CaSO4, là một muối có độ tan rất thấp tại nhiệt độ cao và áp suất cao [3]:
Ca2+ + SO 2- → CaSO ↓
- Sự thay đổi đột ngột áp suất từ vỉa ra lòng giếng:
Khi dòng chất lỏng từ vỉa chảy vào đáy giếng, áp suất đột ngột giảm, dẫn đến sự tách khí CO2 từ trong nước ra pha khí, làm chuyển dịch cân bằng của phản ứng tương tác giữa ion Ca2+ và HCO - theo chiều hình thành muối CaCO3. Đồng thời khi CO2 trong nước thoát ra, sẽ làm tăng pH của nước và làm giảm độ tan của CaCO3 [3]. Hình 2 thể hiện cơ chế hình thành cặn sa lắng vô cơ tại đáy giếng.
Ca2+ + 2HCO3 - ↔ CaCO3 ↓ + CO2 + H2O
4. Mô phỏng quá trình hình thành cặn sa lắng bằng thực nghiệm
4.1. Chuẩn bị và tiến hành thực nghiệm mô phỏng
Sử dụng hệ thống thiết bị thí nghiệm áp suất cao, nhiệt độ cao tại Phòng thí nghiệm của Trung tâm Nghiên cứu Tìm kiếm Thăm dò và Khai thác Dầu khí (EPC) - VPI, nghiên cứu đã mô phỏng lại quá trình phối trộn giữa nước bơm ép và nước từ quá trình mất dung dịch khoan và quá trình giảm áp từ vỉa ra đáy giếng. Các điều kiện áp suất, nhiệt độ tại vỉa và đáy giếng được mô phỏng đúng như điều kiện thực tế. Tỷ lệ phối trộn giữa 2 nguồn nước là 95:5 như tính toán. Cặn sa lắng hình thành sau đó được thu hồi và tiến hành xác định hàm lượng cũng như hình thái tinh thể và thành phần hóa học qua phân tích SEM-EDS và nhiễu xạ tia X-XRD. Thành phần nước bơm ép và nước từ quá trình mất dung dịch khoan cũng như điều kiện thí nghiệm được mô tả trong Bảng 1.
4.2. Kết quả thực nghiệm mô phỏng
Kết quả chụp ảnh SEM cho thấy có 2 loại tinh thể rõ rệt, một loại dài có cấu trúc hình kim, đặc trưng của tinh thể CaSO4 và một loại khá mịn, kích thước nhỏ đặc trưng của CaCO3 hình thành trong điều kiện áp suất cao.
Phân tích thành phần nguyên tố cho thấy các tinh thể dài bao gồm 3 nguyên tố chính là Ca, S và O, trong khi các tinh thể nhỏ và mịn hơn gồm 3 nguyên tố chính là Ca, C và O. Phân tích nhiễu xạ tia X cho thấy các peak đặc trưng của 2 loại tinh thể Gypsum
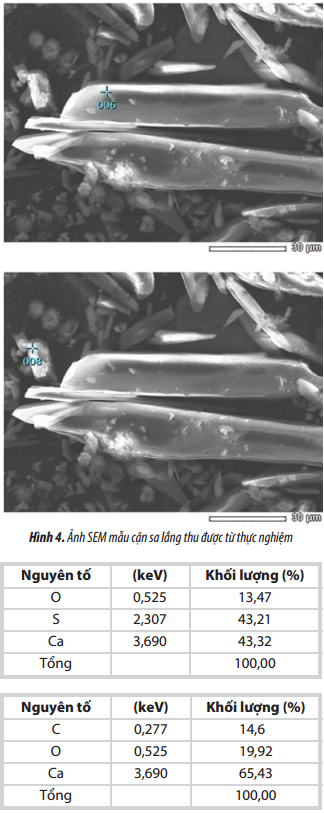
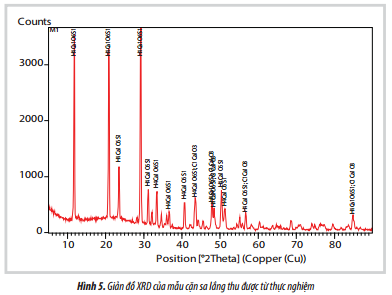
(CaSO4) và Calcite (CaCO3) với tỷ lệ thu được lần lượt là 96% và 4% tương ứng.
Tổng chất rắn thu được trong quá trình thực nghiệm là 2.089mg/L. Kết quả thực nghiệm cho thấy, trong giai đoạn sau thời điểm nước xâm nhập, quá trình phối trộn không tương thích giữa nước bơm ép và nước từ quá trình mất dung dịch khoan và giảm áp tại đáy giếng đã hình thành một lượng đáng kể chất rắn với thành phần chủ yếu là CaSO4 và một lượng nhỏ CaCO3.
5. Mô phỏng quá trình hình thành cặn sa lắng bằng phần mềm
Nguyên tắc tính toán của phần mềm mô phỏng sa lắng
Xu hướng tạo cặn (Scale Tendency) được định nghĩa là tỷ lệ tích số hoạt độ ion (ion activity product) trong phương trình cân bằng với tích số hòa tan của từng chất riêng biệt. Tỷ lệ này có liên quan đến chỉ số bão hòa. Gọi tích số hoạt độ ion là Q, xu hướng tạo cặn là ST, công thức xác định ST như sau:
ST = Q/K
Trong đó, tích số hoạt độ ion Q được tính như sau:
Q = γi × mi
γ : Hệ số hoạt độ của ion i;
mi: Nồng độ mol của ion i; Ksp: Tích số hòa tan.
Khi ST > 1, xu hướng nhiệt động của chất rắn được hình thành, ngược lại khi ST < 1, không có khả năng hình thành chất rắn trong dung dịch.
Như vậy, độ hòa tan của một chất rắn hay khả năng hình thành cặn phụ thuộc rất lớn vào giá trị tích số hòa tan Ksp. Đây là một đại lượng nhiệt động, là hàm phụ thuộc vào giá trị nhiệt độ và áp suất Sự phụ thuộc vào nhiệt độ được biểu thị như sau:
Ln[K(T)] = A + B/T + Cln(T) + DT + E/T2
Trong đó:
T: Nhiệt độ dung dịch; A, B, C, D: Các hằng số.
Sự phụ thuộc vào áp suất được biểu thị như sau:
[(δlnK)/(δP)] = [(ΔZP – ΔV)/RT)]
Trong đó:
ΔZ: Độ thay đổi tính chịu nén phân tử của phản ứng;
ΔV: Độ thay đổi thể tích của phản ứng; R: Hệ số hiệu dụng.
Nghiên cứu sử dụng phần mềm Mô hình mô phỏng cặn sa lắng ScaleChem 9.2. Mô hình này có thể tính toán giá trị ST của các khoáng vật tại các nhiệt độ và áp suất khác nhau, sau đó đưa ra hàm lượng sa lắng tương ứng. Phần mềm ScaleChem 9.2 có thể tính toán đối với hơn 80 khoáng vật khác nhau như: CaCO3, CaSO , BaSO , SrSO , NaCl, FeS... Mô hình mô phỏng cặn sa lắng sử dụng số liệu đầu vào gồm:
- Thành phần hóa học phân tích nước gồm các chỉ tiêu như: Na , K , Mg , Ca , Ba ,Sr2+, Fe2+, Cl-, SO2-, HCO -, pH, TDS;
- Thành phần hydrocarbon của khí và dầu;
- Khoảng thay đổi nhiệt độ (T), áp suất
của dung dịch [5].
(P), lưu lượng khí, dầu, nước.
Kết quả tính toán cặn sa lắng tại đáy giếng 1P-SCL bằng phần mềm ScaleChem
Sử dụng thành phần hóa học của nước bơm ép, nước mất từ dung dịch khoan và các khoảng thay đổi điều kiện nhiệt độ, áp suất từ vỉa ra đáy giếng như trình bày trong mục làm số liệu đầu vào để chạy mô hình mô phỏng. Theo đó, quá trình phối trộn không tương thích giữa nước bơm ép và nước mất từ dung dịch khoan tại tỷ lệ 95% nước bơm ép cho thấy có sự hình thành 2 khoáng vật là CaSO4 và CaCO3 với giá trị ST (Hình 6).
Như vậy, tổng lượng cặn sa lắng tại đáy giếng theo mô hình thu được là 2.373mg/L. Giá trị này khá tương đồng với kết quả thực nghiệm là 2.089mg/L, chứng tỏ phần mềm ScaleChem 9.2 được sử dụng trong nghiên cứu đã mô phỏng chính xác quá trình hình thành cặn sa lắng tại môi trường nhiệt độ cao, áp suất cao. Kết quả mô phỏng bằng phần mềm cũng cho thấy lượng cặn sa lắng CaSO4 chiếm phần lớn và là nguyên nhân chính làm suy giảm hệ số sản phẩm trong quá trình phối trộn không tương thích giữa nước bơm ép và nước mất từ dung dịch khoan.
6. Giải pháp xử lý
Bằng thực nghiệm cũng như mô hình mô phỏng, nghiên cứu dự đoán có một lượng đáng kể cặn sa lắng với thành phần chủ yếu là CaSO4 hình thành tại đáy giếng của giếng khai thác 1P-SCL. Chính lượng cặn sa lắng này đã gây bít nhét các kênh dẫn tại khu vực cận đáy giếng, qua đó làm tăng hệ số Skin và giảm hệ số sản phẩm. Để khôi phục được hệ số sản phẩm, cần phải xử lý phần cặn này. Thông thường, cặn sa lắng vô cơ có thể được xử lý bằng phương pháp cơ học và hóa học. Tuy nhiên, phương pháp cơ học chỉ phù hợp với sự hình thành cặn sa lắng tại các thiết bị khai thác trên bề mặt. Còn đối với khu vực đáy giếng và cận đáy giếng như giếng khai thác 1P-SCL, để loại bỏ cặn sa lắng, phục hồi độ thấm và kênh dẫn thì thường sử dụng phương pháp hóa học.
CaSO4 là muối vô cơ không tan trong acid, vì thế không thể sử dụng phương pháp xử lý acid để loại bỏ. Hiện nay, có 2 phương pháp hóa học chủ yếu để loại bỏ CaSO4 là phương pháp chuyển hóa (converting) và phương pháp hòa tan (chelating).
Phương pháp chuyển hóa
Xử lý CaSO4 với các hóa chất như dung dịch (NH4)2CO3 và NaOH nhằm chuyển muối CaSO4 thành các muối hòa tan trong acid. Sau đó sử dụng phương pháp xử lý acid thông thường để loại bỏ, phản ứng chính của quá trình này như sau:
CaSO + (NH ) CO → (NH ) SO + CaCO
Muối CaCO3 hình thành sau đó có thể được hòa tan bởi HCl:
CaCO + 2HCl → H O + CO ↑ + CaCl
Phương pháp hòa tan
Xử lý CaSO4 với các hóa chất dạng phức càng cua như EDTA (Ethylenediaminetetraacetic acid) hoặc DTPA (Diethylenetriaminepentaacetic acid), có thể hòa tan hoàn toàn CaSO4 mà không cần phải chuyển hóa sang dạng CaCO3. Phản ứng chính của quá trình này như sau [6]:
CaSO + Na EDTA → CaNa EDTA + Na SO
Nhìn chung, đối với các giếng khai thác tại khu vực có nhiệt độ cao, áp suất cao như 1P-SCL, việc sử dụng phương pháp hòa tan với hóa chất có gốc EDTA là phù hợp nhất. Ưu điểm của phương pháp này là hòa tan hiệu quả, ngăn ngừa tái kết tủa, bền tại nhiệt độ cao (lên đến 250oC), không gây ăn mòn thiết bị, không độc hại cho môi trường và sức khỏe con người.
7. Kết luận
- Nguyên nhân hình thành cặn sa lắng là do sự phối trộn không tương thích giữa nước từ quá trình mất dung dịch khoan có hàm lượng CaCl2 cao và nước bơm ép được lấy từ nước biển;
- Sự suy giảm hệ số sản phẩm của giếng khai thác 1P-SCL là do hình thành cặn sa lắng với thành phần chính là CaSO4 tại khu vực cận đáy giếng và đáy giếng;
- Sử dụng hệ thống thí nghiệm áp suất cao, nhiệt độ cao cũng như phần mềm mô phỏng đã xác định chính xác thành phần, hàm lượng cặn sa lắng tại khu vực cận đáy giếng/đáy giếng. Các số liệu thu được từ thực nghiệm phù hợp với tính toán lý thuyết;
- Hóa phẩm gốc EDTA là phù hợp nhất để loại bỏ cặn sa lắng chủ yếu là CaSO4 tại vùng đáy giếng/cận đáy giếng của giếng 1P-SCL;
- Trong quá trình khoan và hoàn thiện giếng cần thận trọng khi sử dụng dung dịch khoan có hàm lượng Ca2+ cao, cũng như cần có các nghiên cứu sự không tương thích của nước bơm ép trong vỉa trước khi tiến hành bơm ép nước vào vỉa để duy trì áp suất vỉa.
Tài liệu tham khảo
1. Guihong Pei, Chunyang Wang, Lili Liu. Experimental study on the cause of inorganic scale formation in the water injection pipeline of Tarim oilfield. Journal of Chemistry. 2014.
2. Francisco J.Alcalá, Emilio Custodio. Using the Cl/Br ratio as a tracer to identify the origin of salinity in aquifers in Spain and Portugal. Journal of Hydrology. 2008; 359(1-2): p. 189 - 207.
3. Amer Badr Bin Merdhah, Abu Azam Mohd Yassin. Study of scale formation in oil reservoir during water injection - A review. Marine Science & Technology Seminar, Kuala Lumpur, Malaysia. 22 - 23 February, 2007.
4. Amer Badr Bin Merdhah, Abu Azam Mohd Yassin. Scale formation in oil reservoir during water injection at high-salinity formation water. Journal of Applied Sciences. 2007; 7(21): p. 3198 - 3207.
5. Chunfang Fan, Amy Kan, Ping Zhang, Haiping Lu, Sarah Work. Scale prediction and inhibition for oil and gas production at high temperature/high pressure. Society of Petroleum Engineers Journal. 2012; 17(2): p. 379 - 392.
6. J.Moghadasi, H.Müller-Steinhagen, M.Jamialahmadi, A.Sharif. Scale deposition in porous media and their removal by EDTA injection. Engineering Conferences International Symposium Series: Proceedings of 7th International Conference on Heat Exchanger Fouling and Cleaning - Challenges and Opportunities, Tomar, Portugal. 1 - 6 July, 2007.
7. M.Amiri, J.Moghadasi. Prediction the amount of barium sulfate scale formation in siri oilfield using OLI ScaleChem software. Asian Journal of Scientific Research. 2010; 3(4): p. 230 - 239.
Investigating the cause and proposing solution for the decrease of Productivity Index during water injection in production well using high Calcium brine as drilling mud
Summary
Hoang Long, Kieu Anh Trung, Truong Van Dung Nguyen Minh Quy, Le Thi Thu Huong
Pham Thi Thuy, Vu Huu Huy
Vietnam Petroleum Institute
Hoang Long - Hoan Vu Join Operating Company E-mail: longh@vpi.pvn.vn
The paper presents a study conducted by the Vietnam Petroleum Institute (VPI) to investigate the cause of Productiv- ity Index decrease during water injection in a production well that produces oil from a basement reservoir, south east off-shore Viet Nam. The formation of inorganic scale in downhole and near-wellbore of the production well was evaluated using the Scalechem 9.2 software and laboratory equipment modelling a high pressure, high temperature system. The incompatible mixing of injection water and drilling mud losses was found as the main cause of scaling (mainly CaSO4) and the drop of Productivity Index. Based on the scale composition and scale amount, an effective solution has been proposed to remove the scale and restore the Productivity Index, thereby increasing the oil production rate.
Key words: Inorganic scale, water injection, drilling mud.