Hệ thống lò hơi phụ trợ 10B8001 đóng vai trò cấp và duy trì cân bằng mạng hơi nước cho Nhà máy Đạm Phú Mỹ. Số liệu vận hành cho thấy lò hơi hoạt động tại ngưỡng nhiệt độ và công suất nhiệt rất cao, tiêu thụ nhiều khí nhiên liệu, là thiết bị có mức độ tiêu hao năng lượng lớn hơn so với các thiết bị nhiệt khác trong Nhà máy Đạm Phú Mỹ.
Nhóm tác giả đã đánh giá thực trạng vận hành, tính toán hiệu suất sử dụng nhiệt, phân tích ảnh hưởng của điều kiện vận hành lò hơi đến mức độ tổn thất năng lượng, phân tích các tiềm năng tối ưu năng lượng và đề xuất các nhóm giải pháp hiệu chỉnh, tối ưu thông số vận hành cũng như cải hoán, nâng cấp hệ thống thiết bị; từ đó giúp giảm chi phí vận hành và nâng cao hiệu quả hoạt động của lò hơi nói riêng và Nhà máy Đạm Phú Mỹ nói chung.
Từ khóa: Lò hơi phụ trợ, hiệu suất sử dụng nhiệt, tổn thất năng lượng, tiết kiệm năng lượng.
1. Giới thiệu
Lò hơi 10B8001 của Nhà máy Đạm Phú Mỹ do MACCHI (Italia) chế tạo với công suất thiết kế 140 tấn/ giờ hơi quá nhiệt cao áp (nhiệt độ 380 ± 5oC, áp suất 39± 0,5barg). Hơi nước sản xuất từ lò hơi 10B8001 kết hợp cùng với hơi nước cao áp từ Phân xưởng Ammonia được cấp đến mạng hơi nước cao áp của Nhà máy Đạm Phú Mỹ, cấp cho các turbine hơi để chạy động cơ bơm, máy nén và là hơi công nghệ làm nguyên liệu cho Phân xưởng Ammonia thực hiện phản ứng reforming tạo khí tổng hợp nhằm sản xuất amoniac. Ngoài ra, lò hơi 10B8001 còn đóng vai trò điều tiết cân bằng mạng hơi trong quá trình khởi động, ngừng máy và vận hành bình thường của Nhà máy Đạm Phú Mỹ nhờ vào công suất thiết kế của lò và điều tiết cấp độ hơi từ cao đến thấp thông qua các trạm tiết lưu/giảm áp (let-down station) hơi nước. Khi vận hành bình thường (normal operation) và mạng hơi nước cân bằng, phụ tải lò hơi vận hành với công suất khoảng 70 tấn/giờ [1].
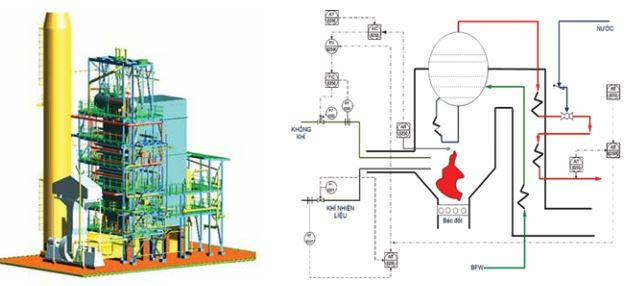 |
|
Hình 1. Mô hình bố trí 3D và sơ đồ điều khiển quá trình cháy của lò hơi 10B8001 (Nguồn: MACCHI, PVFCCo)
Lò hơi 10B8001 là dạng thiết bị kiểu ống nước (water tube boiler) tuần hoàn tự nhiên, được thiết kế với một bao hơi (steam drum) và một bao nước (water drum), đáy có giá đỡ, buồng đốt áp suất nhỏ với thành trong buồng đốt được tạo thành bằng các ống nước, rút nước hoàn toàn. Nhiên liệu sử dụng là khí thiên nhiên hoặc khí đồng hành (sau khi tách khí ngưng tụ - condensate) có thành phần tương tự như khí nguyên liệu đầu vào của Nhà máy Đạm Phú Mỹ. Lò hơi được trang bị hệ thống điều khiển vận hành tự động từ hệ thống DCS chung của Nhà máy và hệ thống tự động bảo vệ BMS (Burner Managing System) lập trình PLC để đảm bảo vận hành an toàn và linh hoạt. Béc đốt sử dụng công nghệ phát thải NOx thấp (low NOx), được bố trí trên thành lò và tạo ngọn lửa cháy theo hướng ngang.
Bảng 1. Thông số thiết kế chính của lò hơi 10B8001 (Nguồn: Nhà máy Đạm Phú Mỹ, PVFCCo)
Quạt cấp không khí cho lò (không khí đốt cháy nhiên liệu) là quạt đẩy cưỡng bức (FD - Forced Draft) được dẫn động bằng turbine hơi vận hành thường xuyên sử dụng hơi nước cao áp và dẫn động bằng motor điện ở trạng thái dự phòng (stand by) [2, 3]. Thông số thiết kế chính của hệ thống lò hơi 10B8001 được trình bày trong Bảng 1.
Nhìn chung, để nâng cao hiệu quả sử dụng nhiệt, trong thiết kế ban đầu hệ thống lò hơi tại Nhà máy Đạm Phú Mỹ có trang bị thiết bị Economizer (bộ thu hồi nhiệt nhằm thu hồi nhiệt hữu ích trong dòng khói lò để gia nhiệt nước cấp lò hơi trước khi đi đến ống khói) và bộ phân tích O2 tự động kết nối với điều khiển DCS để kiểm soát hàm lượng O2 dư trong khói thải. Do đặc thù tính chất của khí nhiên liệu nên lò hơi 10B8001 không trang bị thiết bị tiền gia nhiệt không khí vào lò (Air Preheater - APH) hoặc thiết bị tiền gia nhiệt khí nhiên liệu.
2. Các yếu tố chính ảnh hưởng đến hiệu suất nhiệt của lò hơi
Hiệu suất nhiệt lò hơi (boiler heat efficiency) được định nghĩa là “% (nhiệt) năng lượng đầu vào được sử dụng hiệu quả để tạo ra hơi nước” [4].
Thông thường, giá trị hiệu suất nhiệt và các dạng tổn thất năng lượng trong hệ thống lò hơi có thể liên quan đến quá trình đốt cháy, truyền nhiệt, các tổn thất có thể tránh khỏi, tiêu thụ điện phụ trợ cao, chất lượng nước cấp BFW và xả đáy [5, 6]. Nhóm yếu tố ảnh hưởng chính đến hiệu suất nhiệt của lò hơi 10B8001 được xem xét gồm:
- Hàm lượng O2 dư trong khói thải: Khi hàm lượng O2 dư trong khói thải cao sẽ dẫn đến lưu lượng không khí dư cao gây mất nhiệt theo khói thải và tiêu hao năng lượng cho quạt không khí. Năng lượng tổn thất của lò hơi 10B8001 chủ yếu do yếu tố này và việc tối ưu hóa khá dễ dàng và ít tốn kém;
- Nhiệt độ khói thải của lò: Khi nhiệt độ khói lò cao kết quả là tổn thất năng lượng (mất nhiệt) theo khói thải. Với điều kiện thiết kế an toàn về ăn mòn thiết bị của lò và phải lắp đặt thêm bộ thu hồi nhiệt nếu muốn tận dụng nhiệt dư từ khói lò để gia nhiệt không khí. Vì vậy xét về chi phí đầu tư là khá nhiều;
- Dòng xả đáy Blowdown: Khi lượng xả đáy tăng dẫn đến tổn thất về năng lượng (nước xả đáy nhiệt độ cao), tổn thất về chất (tổn thất nước cấp lò hơi) và tổn thất hóa chất. Năng lượng, nước cấp lò hơi và hóa chất tổn thất của lò có thể khống chế dễ dàng bằng vận hành tối ưu và không tốn kém.
Trong bài báo này, nhóm tác giả chủ yếu đánh giá yếu tố không khí dư (hàm lượng O2 dư trong khói thải của lò hơi 10B8001) là yếu tố có tiềm năng cao để tối ưu, phương thức thực hiện và chi phí đầu tư ước tính ở mức vừa phải. Các yếu tố liên quan đến lượng không khí dư cần xét đến gồm quạt không khí và bộ phân tích hàm lượng O2 dư trong khói thải (Excess oxygen online analyzer).
3. Đánh giá thực trạng vận hành và mức độ thất thoát năng lượng của lò hơi 10B8001 liên quan đến hàm lượng O2 dư trong khói thải
3.1. Nguyên nhân gây tổn thất năng lượng đối với lò hơi 10B8001
Lượng không khí dư (thể hiện qua hàm lượng O2 dư trong dòng khói thải) là một trong những yếu tố chính gây tổn thất năng lượng, làm giảm hiệu suất sử dụng nhiệt của lò hơi.
Hình 2. Mối liên hệ giữa hàm lượng O2 trong khói thải với lượng nhiên liệu tiêu tốn và hiệu suất lò (Nguồn: Nhà máy Đạm Phú Mỹ, GSFC - Ấn Độ, Cosmo Oil - Nhật Bản)
Hình 3. Hệ thống phân tích và điều khiển hàm lượng O2 trong khói lò (Nguồn: Tập đoàn Yokogawa, 2017)
Trong vận hành thực tế, một lượng dư không khí nhất định được duy trì trong buồng đốt để đảm bảo nhiên liệu cháy hết. Tuy nhiên, nếu hàm lượng O2 dư trong khói thải quá cao đồng nghĩa với việc lượng không khí vào lò lớn hơn nhiều so với lượng yêu cầu sẽ dẫn đến tiêu tốn nhiệt để nâng nhiệt độ không khí lên mức đảm bảo đáp ứng quá trình cháy, ngoài ra lượng nhiệt thất thoát từ khói lò hơi cũng lớn hơn [7]. Mối quan hệ giữa các yếu tố quan trọng của lò hơi được thể hiện trong Hình 2.
Theo khuyến cáo của UNIDO (Tổ chức hỗ trợ công nghiệp Liên hợp quốc) và Công ty Dầu Cosmo (Nhật Bản), trong điều kiện vận hành bình thường thì hàm lượng O2 dư trong khói thải nên dao động quanh giá trị 2% thể tích (khí khô) hay tương đương với 10% không khí dư là điểm vận hành tối ưu nhất về năng lượng [8] và an toàn cho thiết bị. Ngoài ra khi vận hành phụ tải càng thấp thì không khí dư càng tăng nhằm đảm bảo an toàn cho thiết bị và hệ số này tùy thuộc vào loại lò, nhiên liệu và giá trị cài đặt trong bộ điều khiển phụ tải (Hình 2). Đối với lò hơi 10B8001, hàm lượng O2 dư trong khói thải dao động trong khoảng giá trị 3,52 - 4,56% thể tích (khí khô). Con số này cao hơn so với mức tối ưu khuyến cáo là do lưu lượng không khí đốt lò lớn dẫn đến tiêu hao nhiệt vô ích tăng lên. Qua đó, tiêu hao nhiên liệu (khí thiên nhiên) tăng và năng lượng tiêu thụ cho quạt cũng sẽ lớn hơn so với thiết kế, tổn thất năng lượng theo khói thải, năng lượng để nâng nhiệt cho không khí khi vào lò và hơi nước cấp cho turbine hơi của quạt khói.
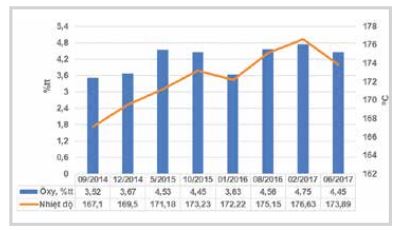 |
|
Hình 4. Số liệu vận hành thực tế hàm lượng O2 dư trong khói thải của lò hơi 10B8001 (giai đoạn 2014 - 2017) (Nguồn: Nhà máy Đạm Phú Mỹ)
Bảng 2. Kết quả tính toán hiệu suất nhiệt lò hơi 10B8001
(*) Giả định theo tài liệu thiết kế lò hơi
Để kiểm soát hàm lượng O2 dư trong khói thải lò hơi, giải pháp thực hiện là xây dựng quy trình kiểm soát lượng không khí đốt lò và xác định hiệu quả của quá trình kiểm soát này bằng cách lắp đặt bộ phân tích khói lò hoặc bộ phân tích - điều khiển tự động hàm lượng O2 theo lưu lượng khí nguyên liệu đầu vào [7]. Một ví dụ thể hiện nguyên lý hoạt động của bộ phân tích, kiểm soát tự động hàm lượng O2 được thể hiện trong Hình 3. Trong đó, tín hiệu từ bộ phân tích khói lò sẽ được truyền đến bộ điều khiển phức hợp kiểm soát lưu lượng không khí bằng cách điều chỉnh độ mở van khống chế lưu lượng không khí đi vào buồng đốt lò hơi.
3.2. Thực trạng vận hành
Số liệu vận hành trung bình của lò hơi 10B8001 tại Nhà máy Đạm Phú Mỹ từ năm 2014 đến tháng 6/2017 cho thấy, khi vận hành bình thường, các thông số của lò hơi khá ổn định và hàm lượng O2 dưtrong khói lò dao động từ 3,52% đến 4,56% thể tích (khí khô), cao hơn nhiều so với giá trị thiết kế lò hơi.
Như vậy, trong điều kiện vận hành bình thường của lò hơi với mức phụ tải ổn định, nhóm tác giả xác định yếu tố có thể làm tăng tổn thất năng lượng của lò hơi có liên quan đến thông số hàm lượng O2 trong dòng khói thải chưa được tối ưu (cao hơn giá trị thiết kế tương ứng với mức phụ tải hoạt động).
3.3. Tính toán hiệu suất nhiệt và mức độ tổn thất năng lượng của lò hơi 10B8001
Để đánh giá chính xác hiệu quả sử dụng nhiệt và phân tích các yếu tố gây tổn thất năng lượng tại lò hơi 10B8001, nhóm tác giả kết hợp tính toán hiệu suất nhiệt của lò hơi bằng phương pháp ASME PTC4 và tính toán mức độ tổn thất năng lượng của lò hơi bằng mô hình tính toán chuyên dụng ở điều kiện thiết kế (phụ tải tối đa 140 tấn/giờ) và điều kiện vận hành bình thường của lò hơi (khoảng 70 tấn/giờ).
3.3.1. Tính toán hiệu suất nhiệt lò hơi 10B8001
Phương pháp ASME PTC4 do Hiệp hội Kỹ sư Cơ khí Mỹ (ASME) đề xuất để tính toán hiệu suất nhiệt của lò hơi với độ chính xác cao và được sử dụng phổ biến trên toàn thế giới, có xem xét yếu tố mất nhiệt và được sử dụng để theo dõi, kiểm tra tình trạng vận hành lò [9].
Hiệu suất nhiệt lò hơi tính được bằng công thức:
(1)
Trong đó:
e: Hiệu suất nhiệt lò hơi (%);
ekkk: Tỷ lệ nhiệt do không khí mang vào (%);
eẩm: Tỷ lệ nhiệt do lượng ẩm trong không khí mang vào (%);
enl: Tỷ lệ nhiệt do bản thân dòng nhiên liệu mang vào(%);
ekk: Tỷ lệ nhiệt mất mát theo khói thải khô (%);
eH O: Tỷ lệ nhiệt mất mát do nước trong nhiên liệu (%);
eH2 : Tỷ lệ nhiệt mất mát do đốt cháy hydro trong nhiên liệu (%);
eam: Tỷ lệ nhiệt mất mát do hơi nước trong không khí (%); ebức xạ: Tỷ lệ nhiệt mất mát do bức xạ (%);
euncou: Tỷ lệ nhiệt mất mát không tính được (%).
Kết quả tính toán hiệu suất nhiệt lò hơi 10B8001 dựa vào số liệu vận hành thực tế được trình bày trong Bảng 2.
Kết quả tính toán cho thấy hiệu suất nhiệt của lò hơi 10B8001 ở mức 81,37% (tính theo nhiệt trị cao - HHV) và 90,18% (tính theo nhiệt trị thấp - LHV). Mức này tương đối cao khi tính theo phương pháp ASME PTC4. Tuy nhiên, mức này cũng thấp hơn hiệu suất của một số nhà máy khác trên thế giới (với cùng loại và phương pháp tính) và vẫn còn khả năng tối ưu hiệu suất nhiệt của lò hơi 10B8001. Ngoài ra, phụ thuộc vào thiết kế và chế độ vận hành của lò hơi đặc biệt ở phụ tải thấp, cần xem xét tính toán chi tiết các thông số của lò hơi ở phụ tải vận hành bình thường và các yếu tố liên quan để tối ưu vận hành lò hơi, tiết kiệm năng lượng.
3.3.2. Tính toán mức độ tổn thất năng lượng của lò hơi 10B8001
- Xây dựng mô hình tính toán và kiểm chứng độ tin cậy của mô hình
Mô hình tính toán mức độ tổn thất năng lượng của lò hơi 10B8001 và quá trình kiểm chứng tính phù hợp của mô hình với số liệu thiết kế và số liệu thực tế vận hành được thực hiện như sau:
+ Sử dụng công cụ tính toán chuyên dụng do nhóm tác giả xây dựng;
+ Xây dựng mô hình lò hơi 10B8001 theo kịch bản thiết kế dựa vào tài liệu dữ liệu thiết bị của nhà cung cấp (Vendor mechanical data sheet) để nhập dữ liệu đầu vào (input data) các thông số thiết bị trao đổi nhiệt, béc đốt,
bao hơi (steam drum)… và chạy kiểm chứng lại mô hình so với các thông số công nghệ trong dữ liệu thiết bị của nhà cung cấp với sai số < 5% trước khi đưa vào tính toán ở điều kiện số liệu vận hành thực tế [10].
Trong quá trình xây dựng mô hình tính toán (Hình 5), nhóm tác giả sử dụng các giả thuyết sau:
+ Chiều dày các ống trao đổi nhiệt không thay đổi so với thiết kế và không có ăn mòn nghiêm trọng cũng như sự cố quá nhiệt;
+ Không có biến dạng tại các ống trao đổi nhiệt (cong, võng hoặc bị oxy hóa);
+ Trở nhiệt (heat resistance) bên trong và bên ngoài ống trao đổi nhiệt theo đúng thiết kế;
+ Lò hơi, buồng đốt và các thiết bị phụ trợ được bảo trì bảo dưỡng theo đúng yêu cầu của nhà cung cấp;
+ Béc đốt và chiều cao ngọn lửa vận hành ổn định theo đúng số liệu thiết kế tại các mức phụ tải khác nhau của lò hơi;
+ Hệ thống đồng hồ đo, van điều khiển, hệ thống BMS vận hành ổn định ở các mức phụ tải của lò hơi.
Sau khi xây dựng mô hình tiến hành chạy ở các điều kiện phụ tải khác nhau, kết quả thu được từ mô hình tính toán so với giá trị thiết kế ở phụ tải 50% (70 tấn hơi nước/ giờ) thể hiện trong Bảng 3.
Với sai số giữa mô hình tính toán và số liệu thiết kế rất thấp (< 5%), mô hình đã thiết lập có độ tin cậy cao và hoàn toàn có thể được sử dụng để tính toán, đánh giá tình trạng thực tế vận hành của lò hơi 10B8001.
- Kết quả tính toán mức độ tổn thất năng lượng của lò hơi 10B8001
Hình 5. Mô hình tính toán dựa trên số liệu thiết kế (Trường hợp 1 - Mô hình dùng để kiểm chứng)
Bảng 3. Kết quả so sánh, kiểm chứng mô hình tính toán lò hơi 10B8001
Hình 6. Trường hợp 2 - Sử dụng số liệu thực tế
Hình 7. Trường hợp 3 - Sử dụng phương án tối ưu hàm lượng O2 dư (giá trị 2,5 thể tích)
Nhóm tác giả xây dựng 3 mô hình tính toán để đánh giá mức độ tổn thất năng lượng của lò hơi 10B8001 ở công suất thiết kế 100% phụ tải (140 tấn/giờ) và kiểm tra ở trường hợp thiết kế 50% phụ tải (70 tấn/giờ). Kết quả tính toán trong trường hợp lò hơi vận hành tại phụ tải khoảng 70 tấn/giờ bao gồm:
- Trường hợp thiết kế: hàm lượng O2 dư 2,972% thể tích (theo giá trị thiết kế) (Hình 5);
- Trường hợp thực tế: hàm lượng O2 dư 3,188% thể tích (phụ tải thực tế) (Hình 6);
- Trường hợp tối ưu: hàm lượng O2 dư 2,50% thể tích (phương án tối ưu hàm lượng O2 dư) (Hình 7).
Đặc tính của lò hơi và thông số liên quan đến các dòng công nghệ của hệ thống lò hơi trong 3 trường hợp trên thể hiện trong Bảng 4.
Giá trị lượng không khí dư (hàm lượng O2 dư) thực tế cao hơn nhiều so với số liệu thiết kế, dẫn đến tổn thất nhiệt qua khói lò tăng. Việc này sẽ làm tăng lượng khí đốt cấp cho lò hơi. Đồng thời, khi lưu lượng không khí tăng lên, đòi hỏi công suất của quạt thổi FD cũng tăng làm tiêu hao thêm hơi cao áp cấp cho turbine hơi dẫn động. Mức độ tổn thất năng lượng của hệ thống lò hơi 10B8001 thể hiện trong Bảng 5.
Qua kết quả ở Bảng 4 cũng xác định rằng có sự sai số khá lớn của bộ phân tích O2 tự động 10AIC8250.
Hiệu quả sử dụng năng lượng của lò hơi 10B8001 chưa cao (chưa đạt thiết kế) do lượng không khí dư khi vận hành thực tế cao hơn so với thiết kế. Hàng năm tổn thất năng lượng do vấn đề này ước tính khoảng 9.858MW (tính theo LHV).
4. Giải pháp tối ưu năng lượng và đánh giá hiệu quả kinh tế
4.1. Giải pháp tối ưu hóa năng lượng
Trên cơ sở tính toán và đánh giá hiệu suất sử dụng nhiệt của lò hơi và phân tích mức độ tổn thất năng lượng của hệ thống lò hơi 10B8001, tham khảo kinh nghiệm của các nhà máy khác trên thế giới trong việc tối ưu hóa lò hơi, nhóm tác giả đề xuất hướng nghiên cứu các giải pháp để điều chỉnh hàm lượng O2 dư trong khói lò hơi 10B8001 xuống mức 2,50% thể tích. Giải pháp thực hiện như sau:
- Kiểm tra tình trạng hoạt động của bộ kiểm soát O2 dư hiện hữu và xem xét việc cải tiến, lắp đặt bộ phân tích mới;
Bảng 4. Kết quả tính toán, đánh giá các trường hợp thiết kế và vận hành thực tế của lò hơi 10B8001
Bảng 5. Mức độ tổn thất năng lượng của lò hơi 10B8001 khi vận hành với hàm lượng O2 dư cao
- Nghiên cứu, đánh giá chế độ vận hành lò hơi phụ trợ, đường đặc tuyến O2 với phụ tải và bộ điều khiển phức hợp phụ tải lò ở điều kiện thiết kế, từ đó giảm lượng không khí dư ở phụ tải vận hành bình thường trước khi nâng cấp Nhà máy Đạm Phú Mỹ (khoảng 70 tấn/giờ hơi nước) và sau khi nâng cấp (khoảng 74 tấn/giờ hơi nước) với hàm lượng O2 dư trong khói lò theo thiết kế là 2,972% thể tích (trước nâng cấp) về càng gần với giá trị tối ưu 2,0% thể tích (tính theo khí khô) càng hiệu quả, tuy nhiên vẫn đảm bảo lò hơi vận hành an toàn, ổn định.
Giải pháp thay thế bộ phân tích O2 trực tuyến hiện hữu.
Kết quả khảo sát tại hiện trường và thảo luận với các nhân viên vận hành lò hơi cho thấy, bộ phân tích hàm lượng O2 khói lò trực tuyến làm việc không ổn định mặc dù được cân chỉnh định kỳ. Do đó, nhóm tác giả đề xuất thực hiện việc lắp đặt bổ sung bộ phân tích khống chế O2 trực tuyến mới (10AITxxxx).
Quy trình lắp đặt và vận hành bộ phân tích khống chế O2 trực tuyến mới như sau:
- Bộ phân tích hàm lượng O2, trực tuyến mới sẽ được lắp đặt cạnh bộ phân tích hàm lượng O2 hiện hữu 10AIT8250;
- Trong giai đoạn bảo dưỡng tổng thể hoặc thời điểm ngừng lò hơi cần tiến hành đấu nối 10AITxxxx mới vào ống khói lò hơi và kết nối về DCS (10AIC8250) bằng đường tín hiệu của 10AIT8250;
- Tiến hành cân chỉnh, kiểm tra tín hiệu từ 10AITxxxx mới vào DCS;
- Khởi động và vận hành lò hơi bằng 10AITxxxx mới;
- Quá trình cân chỉnh lắp đặt sẽ do lực lượng nhà máy thực hiện theo hướng dẫn của nhà cung cấp/chế tạo AIT.
4.2. Hiệu chỉnh, tối ưu hàm lượng O2 dư trong dòng không khí đốt lò
Đối với phương án này, Nhà máy Đạm Phú Mỹ cần xây dựng kế hoạch rõ ràng và có sự giám sát chặt chẽ của các bộ phận liên quan, ngoài ra, có thể tự thực hiện với đội ngũ nhân sự hiện tại hoặc thuê đơn vị tư vấn bên ngoài chuyên thực hiện về hiệu chỉnh lò hơi.
Quy trình đề xuất để thực hiện công tác giảm hàm lượng O2 dư trong dòng không khí đốt lò hơi 10B8001 như sau:
- Khởi động và vận hành lò hơi ổn định theo hướng dẫn vận hành lò hơi phụ trợ do nhà thầu cung cấp. Vì lò hơi có dải hoạt động khá rộng (từ 40 - 100% MCR) do đó cần phải điều chỉnh hàm lượng O2 dư phù hợp theo khuyến cáo của nhà chế tạo lò hơi bằng cách chuyển chế độ vậnhành bộ 10FIC8250 từ chế độ điều khiển nối tiếp (cascade control) sang chế độ điều khiển bằng tay (manual control) và khống chế lưu lượng không khí dư theo phụ tải;
- Từ hệ thống điều khiển DCS đặt lại chương trình đường đặc tuyến của O2 bằng cách thay đổi giá trị của O2 tại phụ tải 50% (70 tấn/giờ) bằng giá trị 2,5 thông qua bộ 10AHC8250 và 10AY8250. Quan sát giá trị thể hiện trên DCS và các bộ điều khiển sau khi thay đổi. Chú ý trong quá trình thực hiện phải tuân thủ chặt chẽ theo các tài liệu hướng dẫn vận hành lò hơi và đảm bảo vấn đề an toàn, cụ thể phải giữ áp suất hơi đầu ra và các điều kiện vận hành lò hơi ổn định, nếu không việc thực hiện nên tạm thời dừng lại và chỉ tiếp tục sau khi các điều kiện vận hành lò hơi ổn định;
Hình 8. Các phần tử trong hệ thống điều khiển phân tán (DCS) lò hơi 10B8001 (Nguồn: Nhà máy Đạm Phú Mỹ)
- Điều chỉnh 10FIC8250 ở chế độ “Manual control” sao cho giá trị hàm lượng O2 dư tại phụ tải hiện hữu gần với giá trị của đường đặc tuyến mới;
- Chuyển 10FIC8250 từ chế độ“Manual control” sang “Cascade control”;
- Quan sát các thông số và kiểm tra phụ tải với hàm lượng O2 mới;
- Hoàn tất quá trình thực hiện.
Thực hiện đánh giá sau mỗi đợt giảm và ghi nhận các sự cố bất thường nếu có. Trường hợp lò hơi vẫn duy trì trạng thái ổn định sau mỗi đợt giảm, tiếp tục vận hành lò trong một khoảng thời gian nhất định với những thông số đã hiệu chỉnh để có những đánh giá chính xác nhất.
4.3. Đánh giá hiệu quả kinh tế - kỹ thuật của phương án tối ưu
Hiệu quả kinh tế - kỹ thuật các nhóm giải pháp tối ưu mang lại được tính toán dựa trên nhiệt trị và giá của khí nhiên liệu: khí nhiên liệu tiết kiệm được được tính theo triệu Btu/năm hoặc GJ/năm, giá khí nhiên liệu cấp cho Nhà máy Đạm Phú Mỹ được lấy theo tài liệu của Ban Khí - Tập đoàn Dầu khí Việt Nam (PVN) tháng 4/2015 là 4,62 USD/triệu Btu [11]. Ngoài ra, các thông số đầu vào thực tế của Nhà máy phục vụ cho việc tính toán được thể hiện trong Bảng 6.
Chi tiết hiệu quả kinh tế - kỹ thuật mang lại của phương án tối ưu hàm lượng O2 dư trong khói thải lò hơi so với trường hợp vận hành thực tế và trường hợp vận hành theo thiết kế được thể hiện trong Bảng 7.
Trong trường hợp tối ưu, lò hơi vận hành tại hàm lượng O2 dư 2,5% thể tích tương ứng với công suất hiện tại (70.000kg/giờ hơi cao áp) thì hiệu suất sử dụng nhiệt của lò hơi tăng lên mức 83,60%, tổng năng lượng tiết kiệm được khoảng 9.858MW/năm (tính theo LHV). Đồng thời, suất tiêu hao nhiên liệu tính trên 1kg hơi sản xuất giảm từ mức 0,0702Nm3/kg xuống mức 0,0698Nm3/kg. Chi phí đầu tư ban đầu gồm chi phí mua sắm - lắp đặt thêm thiết bị 10AITxxxx mới ước tính là 100.000USD. Chi phí hàng năm thu được 115.000USD/năm, thời gian hoàn vốn của phương án khoảng 10 tháng.
Bảng 6. Thông số đầu vào (thực tế) phục vụ tính toán
Bảng 7. Hiệu quả kinh tế - kỹ thuật mang lại của phương án hiệu chỉnh hàm lượng O2 dư phù hợp
Ghi chú:
(1) Tiêu thụ khí đốt cần thiết để sản xuất 1kg hơi nước; (2) Năng lượng tiết kiệm chuyển đổi cho trường hợp vận hành sản xuất 70.000kg/giờ hơi nước
(3) Chi phí đầu tư bao gồm đầu tư mới thiết bị 10AITxxxx mới
5. Kết luận
Với thực tế vận hành hiện tại, việc nghiên cứu, đánh giá và đề xuất các giải pháp tiết kiệm năng lượng, nâng cao hiệu suất sử dụng nhiệt hệ thống lò hơi 10B8001 Nhà máy Đạm Phú Mỹ là rất cần thiết. Hiệu quả của việc tối ưu lò hơi góp phần giảm chi phí vận hành bảo dưỡng, nâng cao hiệu quả hoạt động của Nhà máy. Giải pháp đề xuất để tối ưu vận hành lò hơi gồm:
- Kiểm tra và thực hiện đánh giá tình trạng hoạt động của bộ phân tích O2 trực tuyến và đề xuất đầu tư - lắp đặt mới hệ thống 10AITxxxx thay cho hệ thống 10AIC8250 hiện hữu;
- Hiệu chỉnh hàm lượng O2 dư trong dòng khói lò hơi từ mức hiện tại 3,190% thể tích (khí khô) xuống mức 2,5% thể tích tương ứng với điều kiện vận hành của lò bằng việc lắp đặt bổ sung hệ thống điều khiển và kiểm soát chặt chẽ hơn hàm lượng O2 dư trong khói thải và thực hiện công tác vận hành lò trong điều kiện hàm lượng O2 tối ưu. Giải pháp này tăng hiệu suất sử dụng nhiệt của lò hơi lên mức 83,60%. Đồng thời, suất tiêu hao nhiên liệu tính trên 1kg hơi sản xuất giảm từ 0,0702Nm3/kg xuống 0,0698Nm3/kg. Chi phí đầu tư ban đầu gồm chi phí mua sắm - lắp đặt thêm thiết bị 10AITxxxx mới, ước tính là 100.000USD, chi phí hàng năm thu được 115.000USD/năm và thời gian hoàn vốn của phương án khoảng 10 tháng.
Tài liệu tham khảo
1. PVFCCo. Operating manual: Ammnia production & power steam generation. 2003.
2. PVFCCo. Quy trình vận hành lò hơi phụ trợ 10-B- 8001. 2003.
3. MACCHI. Boiler 10B8001 Vendor data book. 2003.
4. Alan P.Rossiter, Beth P.Jones. Energy management and efficiency for the process industries. American Institute of Chemical Engineers. 2015.
5. Patrik Thollander, Jenny Palm. Improving energy efficiency in industrial energy systems. Springer-Verlag London. 2013.
6. UNEP. Thiết bị nhiệt: Lò hơi và thiết bị gia nhiệt. Hướng dẫn sử dụng năng lượng hiệu quả trong các ngành công nghiệp châu Á. 2008.
7. Hoàng Ngọc Đồng, Lê Hoài Anh. Một số giải pháp tiết kiệm năng lượng trong lò hơi công nghiệp. Tạp chí Khoa học và Công nghệ, Đại học Đà Nẵng. 2010; 2(37); trang 47 - 56.
8. COSMO Oil Co., Ltd. Energyconservationinrefineries of COSMO Oil. 2006.
9. ASME PTC 4 - 2013. Fired steam generators. 2013.
10. Jorge Ancheyta. Modeling and simulation of catalytic reactors for petroleum refining. Wiley. 2011.
11. Ban Khí - Tập đoàn Dầu khí Việt Nam. Đánh giá về các nguồn khí - cơ chế giá khí cho việc phát triển các dự án hóa dầu từ khí. 2015.
ASSESSMENT OF THERMAL EFFICIENCY AND PROPOSED SOLUTIONS FOR IMPROVING ENERGY SAVING OF AUXILIARY BOILER SYSTEM 10B8001 IN PHU MY FERTILIZER PLANT
Le Hong Nguyen (1), Le Thanh Phuong (1) Dang Thi Tuyet Mai (1), Nguyen Minh Hieu (2)
1.Vietnam Petroleum Institute.
2.Phu My Fertilizer Plant
Email: nguyenlh.pvpro@vpi.pvn.vn
Summary
The auxiliary boiler system 10B8001 is designed to supply and maintain the steam balance for Phu My Fertilizer Plant. Based on actual operating data, the boiler operates at very high temperature and heat capacity, consumes a lot of fuel gas and there is a higher level of energy loss than other thermal equipment in Phu My Fertilizer Plant.
The authors review the current status of the boiler’s operation, calculate the thermal efficiency, analyse the relationship of boiler operating conditions to energy loss, and propose optimal solutions related to calibration, optimisation of operating parameters as well as the improvement and upgrading of equipment systems. These optimal solutions will reduce the operating costs and improve the performance of the boiler in particular and Phu My Fertilizer Plant in general.
Key words: Auxiliary boiler, thermal efficiency, energy loss, energy saving.
Xem chi tiết