Tóm tắt
Bài báo đánh giá một số giải pháp tái sử dụng xúc tác FCC thải của Nhà máy Lọc dầu Dung Quất, trong đó chú trọng các phương án làm vật liệu xây dựng để đảm bảo chất thải được xử lý triệt để và lâu dài. Kết quả thử nghiệm và khảo sát thực tế cho thấy các phương án khả thi về mặt kỹ thuật, công nghệ và quy mô công suất tại Việt Nam được sắp xếp theo thứ tự ưu tiên về lượng tiêu thụ tối đa xúc tác FCC thải như sau: nguyên liệu sản xuất xi măng (20 - 200 tấn/ngày), phụ gia hoạt tính pozzolan (> 15 tấn/ngày), gạch đất sét nung (15 tấn/ngày), gạch không nung (11 - 17 tấn/ngày).
1. Mở đầu
Hiện nay, Nhà máy Lọc dầu Dung Quất cũng như nhiều nhà máy lọc dầu trên thế giới đang nghiên cứu phương án xử lý các chất thải vừa đảm bảo an toàn môi trường vừa tiết kiệm chi phí. Một số phương án tái sử dụng xúc tác FCC thải đã được triển khai thương mại hóa trên thế giới như: Từ khóa: Xúc tác FCC thải, tách từ, tái sử dụng, vật liệu xây dựng, nhựa đường, gạch không nung, gạch đất sét nung.
- Tách từ để tái sử dụng một phần xúc tác FCC thải bằng công nghệ của MagnaCat và MCat Service được áp dụng tại Mỹ, Nhật Bản…;
- Tái sử dụng xúc tác FCC thải như nguyên liệu sản xuất xi măng được thực hiện thường xuyên tại các nhà máy như: Boral (Úc), Holcim (Mỹ), Oman đã đưa xúc tác FCC thải vào dây chuyền sản xuất xi măng như một nguồn nguyên liệu thay thế với tỷ lệ xúc tác trong nguyên liệu từ 0,5 - 5% khối lượng [1 - 3];
- Phối trộn xúc tác FCC thải để sản xuất bê tông nhựa đường đã được triển khai ở một số nhà máy chủ yếu ở châu Âu;
- Phối trộn để sản xuất gạch đất sét nung;
- Phương án trộn sống xúc tác FCC thải như một thành phần phụ gia khoáng cho xi măng và các sản phẩm dẫn xuất như: hồ, vữa, bê tông… Giải pháp này được đầu tư nghiên cứu ở các nước đang phát triển ở khu vực châu Á [4 - 7] với tỷ lệ thay thế xi măng bằng xúc tác FCC thải từ 5 - 15% khối lượng.
Ở Việt Nam, một thử nghiệm (do Công ty TNHH MTV Lọc hóa dầu Bình Sơn - BSR đầu tư, Đại học Bách khoa Hà Nội thực hiện tại trạm nghiền clinker của Công ty CP Xi măng Bỉm Sơn tại Quảng Ngãi) đã đánh giá khả năng phối trộn xúc tác FCC thải như phụ gia khoáng. Kết quả cho thấy sản phẩm xi măng thương mại tạo thành từ quá trình trộn và nghiền 5% xúc tác FCC thải (như một loại phụ gia khoáng) với clinker và thạch cao cũng có chất lượng tương đương với xi măng portland Bỉm Sơn mác PCB 40, đồng thời không gây rò rỉ kim loại và đáp ứng các tiêu chuẩn môi trường. Một dây chuyền quy mô nhỏ khác của Tổng công ty Lắp máy Việt Nam (Lilama) sản xuất gạch bê tông xi măng (gạch không nung) từ xúc tác FCC thải cho thấy khả năng phối trộn đến 35% xúc tác FCC trong hệ cấu tử. Ngoài ra, có một số nghiên cứu quy mô nhỏ tại Việt Nam như tái sử dụng xúc tác FCC thải để cracking dầu nhờn thải [8] hay nhựa thải [9], tuy nhiên chỉ dừng ở quy mô nhỏ chưa phát triển thành công nghệ. Bài báo đánh giá các phương án đã triển khai thực tế rên thế giới để đưa ra giải pháp xử lý xúc tác FCC thải cho Nhà máy Lọc dầu Dung Quất, trong đó tập trung vào các phương án về tái chế vật liệu xây dựng như sản xuất xi măng và dẫn xuất từ xi măng, gạch đất sét nung.
2. Thực nghiệm
Trên cơ sở tài liệu về các phương pháp xử lý xúc tác FCC thải được áp dụng phổ biến trên thế giới, nhóm tác giả chọn lọc và tập trung nghiên cứu các phương pháp có tính khả thi cao về công nghệ, có khả năng ứng dụng nhanh tại Việt Nam. Các phương pháp này sẽ được thử nghiệm tại các phòng thí nghiệm chuyên ngành và các công ty vật liệu xây dựng để đưa ra số liệu tin cậy. Phương pháp thực nghiệm chủ yếu gồm: xác định thành phần hóa học bằng thiết bị phân tích huỳnh quang tia X (XRF) theo ASTM D7085, các tính chất hóa lý như phân bố kích thước hạt theo ASTM D4464, diện tích bề mặt theo ASTM D3663 và một số tính chất khác theo tiêu chuẩn vật liệu xây dựng của Việt Nam như TCVN 6882 về Phụ gia khoáng cho xi măng, TCVN 3118 về Bê tông nặng - phương pháp xác định cường độ nén và TCVN 3119 về Bê tông nặng - phương pháp xác định cường độ kéo khi uốn, TCVN 1451 về Gạch đặc đất sét nung. Sau khi xác định số liệu về thử nghiệm, nhóm tác giả đã khảo sát thực tế để tìm hiểu quy mô và khả năng xử lý xúc tác thải cho Nhà máy Lọc dầu Dung Quất của các đơn vị. Bài viết đưa ra bộ 3 tiêu chí dùng để đánh giá các phương án gồm:
- Đặc tính kỹ thuật: đánh giá sự phù hợp về đặc tính hóa lý của xúc tác FCC thải và các yêu cầu đặc trưng cơ bản của vật liệu tái sử dụng thông qua các thử nghiệm;
- Tính khả thi về công nghệ: xem xét phương án đã triển khai ở quy mô công nghiệp để đảm bảo khả thi về công nghệ thông qua tổng quan thế giới và tình hình thực tế Việt Nam;
- Quy mô công suất tiêu thụ: phương án khả thi cần đáp ứng tối thiểu 15 tấn/ngày dựa trên lượng thải của Nhà máy Lọc dầu Dung Quất.
Xúc tác FCC được thải ra sau khi đã qua thiết bị tái sinh thứ nhất và một phần nhỏ bụi xúc tác thải ra ngoài sau khi qua thiết bị lọc bụi tĩnh điện. Một số tính chất xúc tác FCC thải của Nhà máy Lọc dầu Dung Quất được trình bày trong Bảng 1.
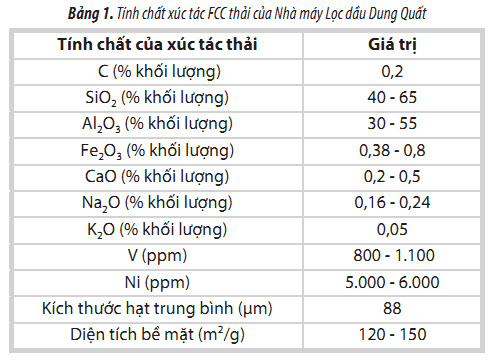
3. Kết quả và thảo luận
3.1. Đánh giá phương án làm nguyên liệu cho nhà máy xi măng
3.1.1. Đặc tính kỹ thuật
Thành phần hóa học của xi măng thường biến đổi trong khoảng rộng gồm: CaO (40 - 60% khối lượng), SiO2 35 - 40% khối lượng), Al2O3 (5 - 20% khối lượng) [10]. Thành phần của xúc tác FCC với SiO2 (40 - 60% khối lượng) và Al2O3 (35 - 55% khối lượng) phù hợp để đưa vào nhà máy xi măng. Ngoài ra, lò đốt xi măng còn được coi là thiết bị hữu hiệu để xử lý nhiều loại chất thải của các nhà máy lọc dầu hoặc các nhà máy khác nhằm giải quyết vấn đề môi trường. Tuy nhiên, các nhà máy xi măng cũng có yêu cầu riêng về thành phần tạp chất trong chất thải có thể ảnh hưởng đến khả năng kiểm soát ô nhiễm môi trường.
Kết quả Bảng 2 cho thấy, xúc tác FCC thỏa mãn các điều kiện để có thể xử lý trong lò nung của Nhà máy Xi măng Holcim (Công ty TNHH Xi măng Holcim Việt Nam). Xúc tác FCC thải có thể đưa vào các dây chuyền sản xuất xi măng do công nghệ lò đốt hiện nay rất phát triển và tỷ lệ đưa vào lò đốt xi măng rất thấp.
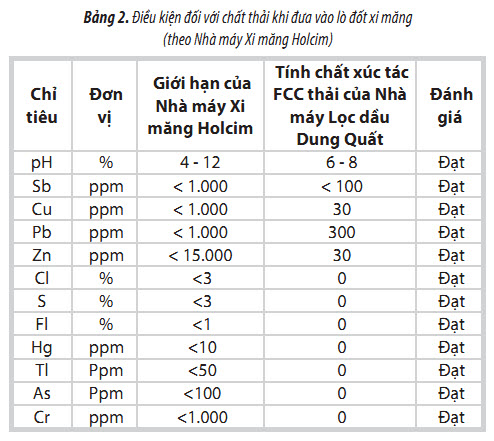
3.1.2. Tính khả thi về công nghệ
Trên thế giới, có 3 công ty lớn gồm: Boral (Australia), Holcim (Mỹ), Amita (Nhật Bản) đã thương mại phương pháp đưa xúc tác FCC thải vào sản xuất xi măng với lượng xúc tác phối trộn 0,5 - 5%, còn lại thành phần chủ yếu là đá vôi (~75%) và khoáng sét [3, 11]. Tại Việt Nam, phương án này hoàn toàn khả thi về công nghệ do đã có nhiều nhà máy xi măng như Holcim và một số nhà máy khác, trong đó sử dụng công nghệ hiện đại của nước ngoài. Tuy nhiên do vấn đề xử lý xúc tác FCC thải của nhà máy lọc dầu còn khá mới đối với các nhà máy xi măng nên các nhà máy này cũng cần có thời gian chuẩn bị để có thể tiêu thụ chất thải này của nhà máy lọc dầu.
3.1.3. Quy mô công suất
Với tần suất thải xúc tác FCC của Nhà máy Lọc dầu Dung Quất trên 15 tấn/ngày, tỷ lệ xúc tác bổ sung vào nguyên liệu trong dây chuyền xi măng khoảng 0,5 - 5% khối lượng thì công suất của các nhà máy xi măng phải đạt khoảng 90.000 - 900.000 tấn/năm. Đa số nhà máy xi măng tại Việt Nam hiện nay có công suất lớn, có khả năng tiêu thụ xúc tác FCC thải của Nhà máy Lọc dầu Dung Quất. Đặc biệt, 2 nhà máy sản xuất xi măng mới ở khu vực miền Trung là Đồng Lâm (Huế) và Thạch Mỹ (Quảng Nam) có công suất 1,2 triệu tấn/năm, nằm trong bán kính 200km từ Nhà máy Lọc dầu Dung Quất. Với tỷ lệ sử dụng xúc tác thải từ 0,5 - 5% khối lượng thì mỗi nhà máy xi măng này có thể tái chế được 20 - 200 tấn xúc tác thải/ngày, đạt tiêu chí về quy mô công suất.
3.2. Đánh giá phương án làm vật liệu hoạt tính pozzolan
3.2.1. Đặc tính kỹ thuật
Vật liệu có hoạt tính pozzolan là vật liệu bổ sung vào xi măng, giúp xúc tiến quá trình đông kết khi tạo các sản phẩm cuối như: hồ, vữa, bê tông (điển hình là bê tông tươi, bê tông đúc sẵn, gạch không nung…). Đây là phụ gia không thể thiếu trong quá trình sản xuất vật liệu xây dựng. Clinker sau khi nung được nghiền mịn và bổ sung phụ gia, chủ yếu gồm: thạch cao (nhằm tăng thời gian nung kết), phụ gia khoáng hoạt tính (nhằm tăng hoạt tính), chất độn như cát SiO2, đá vôi CaCO3 (nhằm hạ giá thành sản phẩm). Phụ gia khoáng hoạt tính thường là tro xỉ, pozzolan, bột đá vôi, thạch cao, nham thạch, đất sét… [10]. Xúc tác FCC thải được sử dụng làm phụ gia khoáng cho bê tông đáp ứng theo tiêu chuẩn TCVN 3735:1982 về phụ gia hoạt tính pozzolan.
Kết quả so sánh tính chất của xúc tác FCC thải với phụ gia hoạt tính theo TCVN 3735:1982 (Bảng 3) cho thấy có thể sử dụng xúc tác FCC thải làm bột khoáng pozzolan. Tuy nhiên, để định lượng xúc tác thải có thể đưa vào sản phẩm cuối là vữa hay bê tông cần có các thí nghiệm phối trộn theo cấp phù hợp với các mác xi măng/bê tông chuẩn.
Để xác định tỷ lệ xúc tác FCC thải có thể pha trộn để thay thế xi măng trong các sản phẩm dẫn xuất từ xi măng như bê tông, hay gạch block (còn gọi là gạch bê tông/gạch không nung), các cấp phối thử nghiệm bê tông mác 25MPa và 45MPa đã được thiết kế để thay thế xi măng bằng xúc tác FCC thải với tỷ lệ từ 5 - 25% khối lượng. Tính chất sản phẩm bê tông về độ bền nén được đánh giá sau 3 ngày, 7 ngày, 28 ngày. Sau 28 ngày, độ bền của mẫu bê tông ổn định không đổi, do đó có thể coi là độ bền cuối của mẫu. Hình 2 cho thấy cường độ uốn và nén của mẫu bê tông tái chế sau 28 ngày có khoảng tối ưu, với bê tông ác cao 45Mpa và mác thấp 25MPa thì tỷ lệ tối ưu tương ứng là 10% khối lượng và 15% khối lượng xúc tác FCC thải thay cho xi măng trong cấp phối, tỷ lệ này tương đồng với một số nghiên cứu khác trên thế giới [4 - 7]. Khi đó, độ bền nén của bê tông chứa xúc tác thải tăng từ 4 - 12% so với mẫu đối chứng.
Như vậy có thể kết luận với tỷ lệ tối ưu 10 - 15% khối lượng thay thế xi măng, tương ứng với tỷ lệ trong tổng thành phần phối trộn của mẫu bê tông là khoảng 1,2 - 1,4% khối lượng, thì xúc tác FCC có thể được sử dụng như phụ gia hoạt tính pozzolan, nhằm tạo ra các sản phẩm dẫn xuất từ xi măng như các loại bê tông, gạch block (gạch không nung) với độ bền cải thiện.


3.2.2. Tính khả thi về công nghệ
Kết quả các nghiên cứu trên thế giới khá đồng nhất, cho thấy tiềm năng lớn khi sử dụng xúc tác FCC thải như phụ gia hoạt tính pha trộn xi măng, làm tăng độ bền của hồ hay vữa [12 - 14] hoặc có thể thay thế xi măng trong cấp phối bê tông theo tỷ lệ 5 - 15% [4 - 7, 15]. Xi măng tái chế đảm bảo tính chất theo tiêu chuẩn ASTM C150 và tiêu chuẩn môi trường, có thể gia tăng 20% độ bền nén so với mẫu không có chứa xúc tác FCC [6, 16].
Các dây chuyền chế biến pozzolan từ đá hoặc các vật liệu pozzolan tự nhiên khác tại Việt Nam có thể sử dụng xúc tác FCC thải do xúc tác này đáp ứng các tính chất của vật liệu pozzolan thông thường và do đó sẽ không có sự giới hạn về công nghệ. Thực tế khảo sát cho thấy tại khu vực lân cận Nhà máy Lọc dầu Dung Quất có Công ty Sản xuất Vật liệu Pozzolan IDICO hay Nhà máy Xi măng Vạn Tường, sản xuất phụ gia từ các vật liệu pozzolan tự nhiên (như đá pozzolan) bằng cách nghiền nhỏ, sấy khô và phối trộn với các phụ gia khác. Ngoài ra, Công ty CP Cơ khí Lắp máy Lilama (EMC) tại Quảng Ngãi đã đưa xúc tác FCC vào dây chuyền sản xuất gạch block (hay gạch bê tông với công suất 5 tấn xúc tác/ngày). Công ty Bê tông ly tâm Thủ Đức có thỏa thuận đồng ý tiêu thụ xúc tác FCC thải để đưa vào dây chuyền sản xuất bê tông đúc sẵn do xúc tác giúp cải thiện độ bền của sản phẩm. Do đó, phương án này khả thi về mặt công nghệ để có thể triển khai quy mô lớn tại Việt Nam cho các nhà máy sản xuất vật liệu pozzolan, bê tông và gạch k ông nung.
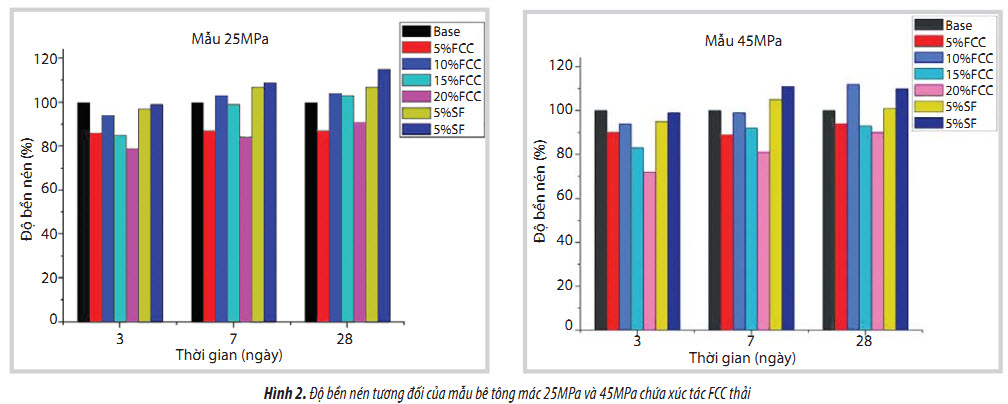
3.2.3. Quy mô công suất
Ở phương án này, nếu đưa trực tiếp xúc tác thải vào sản phẩm cuối (bê tông, gạch không nung...) với vai trò thay thế một phần xi măng thì xúc tác FCC chỉ có thể đưa vào với tỷ lệ 1,4% khối lượng như kết quả thực nghiệm trên. Các tính toán sơ bộ cho thấy lượng xúc tác FCC thải tối đa mà các nhà máy vật liệu xây dựng có thể xử lý được thể hiện trong Bảng 4.
Kết quả khảo sát thực tế tại khu vực lân cận Nhà máy Lọc dầu Dung Quất cho thấy có 3 cơ sở có thể đáp ứng yêu ầu xử lý toàn bộ xúc tác FCC thải (trên 15 tấn/ngày). Do đó, BSR cần làm việc với đơn vị có công suất lớn nhất này để đàm phán về dịch vụ xử lý.
- Khả năng làm vật liệu pozzolan: Công ty Sản xuất Vật liệu Pozzolan IDICO hay Nhà máy Xi măng Vạn Tường (sản phẩm là phụ gia cho xi măng và bê tông đầm lăn từ mỏ pozzolan núi Đầu Voi tại huyện Sơn Tịnh, tỉnh Quảng Ngãi) có khả năng tiêu thụ trên 15 tấn xúc tác FCC thải/ngày.
- Khả năng làm phụ gia phối trộn bê tông: Công ty CP Bê tông Hòa Cầm có khả năng tiêu thụ 22,5 tấn xúc tác FCC thải/ngày. Một số nhà máy khác có khả năng tiêu thụ xúc tác thải thấp do công suất nhỏ.
- Khả năng làm gạch không nung: Dây chuyền sản xuất gạch không nung của Công ty CP Đầu tư Hồng Hoàng Hồng (Đà Nẵng) có khả năng tiêu thụ 17 tấn xúc tác FCC thải/ngày. Ngoài ra, tại khu vực lân cận có một số nhà máy sản xuất gạch không nung với công suất nhỏ.
3.3. Đánh giá phương án tái sử dụng làm gạch đất sét nung
3.3.1. Đặc tính kỹ thuật
Thành phần chủ yếu của gạch đất sét nung gồm đất sét, ngoài ra có các phụ gia trợ cháy và phụ gia cơ lý khác. Đất sét và xúc tác FCC thải có thành phần hóa học khá tương đồng: hàm lượng SiO2 tương ứng là 60% khối lượng và 40 - 60% khối lượng, hàm lượng Al2O3 tương ứng là 22% khối lượng và 35 - 55% khối lượng. Đánh giá chất lượng sản phẩm gạch đất sét nung sau khi pha trộn xúc tác FCC cho thấy ảnh hưởng tích cực của xúc tác FCC lên độ bền của gạch. Kết quả thực nghiệm cho thấy tỷ lệ xúc tác thải có thể thay thế trong gạch lên đến 20% vẫn đáp ứng độ bền nén của gạch, tuy nhiên chỉ ở 5% gạch mới có độ hút nước < 16% đạt tiêu chuẩn TCVN 1451:1998 về Gạch đặc đất sét nung (Bảng 5). Có thể kết luận về đặc tính kỹ thuật, xúc tác FCC thải phù hợp để sản xuất gạch đất sét nung.
3.3.2. Tính khả thi về công nghệ
Công nghệ đưa xúc tác FCC thải vào sản xuất gạch đất sét nung đã được triển khai quy mô lớn ở châu Âu (Hà Lan) và châu Á. Báo cáo khảo sát tại châu Âu [3] cho thấy có rất nhiều nghiên cứu tái sử dụng xúc tác FCC thải để sản xuất gạch nung (red brick), đặc biệt Hà Lan đã sản xuất thử nghiệm với tỷ lệ thay thế xúc tác FCC thải 5%. Kết quả cho thấy chất lượng gạch tái chế đáp ứng tiêu chí kỹ thuật và môi trường. V, Ni và Sb là 3 kim loại còn lại trong gạch thành phẩm nhưng không ảnh hưởng đến môi trường [3]. Ngoài ra, Chou và cộng sự [17] đã nghiên cứu sử dụng phương pháp ép khuôn và triển khai ở quy mô lớn, công suất 2.000 viên/mẻ cho kết quả tốt với hàm lượng xúc tác sử dụng là từ 13,5% khối lượng và 27,2% khối lượng. Như vậy, tính khả thi về công nghệ của phương án này đã được khẳng định trong thực tế.
3.3.3. Quy mô công suất
Công nghệ sản xuất gạch đất sét nung đã quen thuộc và có quá trình phát triển lâu dài, do đó việc đưa thêm xúc tác vào quy trình sản xuất không phức tạp so với các công nghệ khác. Trong lúc gạch đất sét nung còn chiếm phần lớn thị trường gạch xây thì phương án đưa vào gạch nung này hứa hẹn khả năng ứng dụng tức thì cho nhà máy lọc dầu. Các nhà máy gạch đất sét nung trong khu vực dưới 200km từ Nhà máy Lọc dầu Dung Quất (tại Quảng Ngãi, Quảng Nam, Đà Nẵng và Bình Định) gồm có khoảng 7 nhà máy, tuy nhiên đa số là nhà máy nhỏ. Nếu lượng xúc tác thải có thể được sử dụng để thay thế vào nguyên liệu ban đầu với hàm lượng 5% thì chỉ có Nhà máy gạch Phú Điền với công suất tiêu thụ lớn nhất khu vực (250 - 300 tấn nguyên liệu/ngày) xử lý được lượng xúc tác thải 15 tấn/ ngày. Và nếu xét tổng 7 nhà máy gạch tại khu vực lân cận Nhà máy Lọc dầu Dung Quất, có thể ước tính khả năng tiêu thụ làm gạch đất sét nung tổng cộng không quá 30 tấn/ngày.
4. Kết luận
Các phương án tái sử dụng xúc tác FCC thải khả thi về mặt công nghệ và có khả năng tiêu thụ lượng xúc tác đáp ứng về công suất (Bảng 6). Trong đó, khả năng tiêu thụ xúc tác FCC thải lớn nhất là sử dụng làm nguyên liệu đầu vào cho các nhà máy sản xuất xi măng, tiếp theo là phụ gia hoạt tính pozzolan để sản xuất ra các loại phụ gia hay phối trộn sản xuất bê tông và gạch không nung, có thể sử dụng thay đất sét để sản xuất gạch nung.
Xét về lợi ích xã hội và môi trường thì phương án làm vật liệu xây dựng giúp làm giảm khai thác nguồn nguyên liệu tự nhiên, từ đó giảm lãng phí tài nguyên, đồng thời xúc tác sẽ được đưa vào các sản phẩm cuối như gạch, bê tông, hạn chế chất thải ra môi trường.
Tài liệu tham khảo
1. M.Marafi, A.Stanislaus, E.Furimsky. New catalysts from spent catalysts. Handbook of Spent Hydroprocessing Catalysts. Elsevier. 2010: p. 231 - 257.
2. Hoàng Văn Phong. 20 chủng loại xi măng và công nghệ sản xuất. Nhà xuất bản Khoa học Kỹ thuật. 2006.
3. R.Schmitt. FCC catalyst finds three safe reuse outlets in Europe. Oil & Gas Journal. 1991.
4. Hsiu Liang Chen, Yun Sheng Tseng, Kung Chung Hsu. Spent FCC catalyst as a pozzolanic material for high- performance mortars. Cement and Concrete Composites. 2004; 26(6): p. 657 - 664.
5. J.Monzó, J.Payá, M.V.Borrachero, E.Mora, S.Velázquez. Fluid catalytic cracking residue (FC3R) as a new pozzolanic material: Thermal analysis monitoring of FC3R/ Portland cement reactions. 7th CANMET/ACI International Conference on Fly Ash, Silica Fume, Slag and Natural Pozzolans in Concrete, India. 22 - 27 July, 2001.
6. B.Pacewska, I.Wilińska, J.Kubissa. Use of spent catalyst from catalytic cracking in fluidized bed as a new concrete additive. Thermochimica Acta. 1998; 322(2): p. 175 - 181.
7. B.Pacewska, M.Bukowsk, I.Wilińska, M.Swat. Modification of the properties of concrete by a new pozzolan - a waste catalyst from the catalytic process in a fluidized bed. Cement and Concrete Research. 2002; 32(1): p. 145 - 152.
8. L.Alonso, J.M.Palacios, E.García, R.Moliner. Characterization of Mn and Cu oxides as regenerable sorbents for hot coal gas desulfurization. Fuel Processing Technology. 2000; 62(1): p. 31 - 44.
9. Hans Zeiringer. Preparation of abrasive material from spent catalysts. US Patent 4142871 A. 1979.
10. Đỗ Quang Minh, Trần Bá Việt. Công nghệ sản xuất xi măng poóc lăng và các chất kết dính vô cơ. Nhà xuất bản Đại học Quốc gia Thành phố Hồ Chí Minh. 2007.
11. Brian McGrath. Reuse of spent oil catalyst in the manufacture of cement. IQA-CCAA Construction Material Industry Conference. 19 - 22 September, 2012.
12. J.Payá, J.Monzó, M.V.Borrachero, S.Velázquez. Evaluation of the pozzolanic activity of fluid catalytic cracking catalyst residue (FC3R). Thermogravimetric analysis studies on FC3R-Portland cement pastes. Cement and Concrete Research. 2003; 33(4): p. 603 - 609.
13. S.K.Antiohos, E.Chouliara, S.Tsimas. Re-use of spent catalyst from oil-cracking refineries as supplementary cementing material. China Particuology. 2006; 4(2): p. 73 - 76.
14. N.T.Castellanos, J.T.Agredo. Using spent fluid catalytic cracking (FCC) catalyst as pozzolanic addition - A review. 2010; 30(2): p. 35 - 42.
15. N.Su, Z.-H.Chen, H.-Y.Fang. Reuse of spent catalyst as fine aggregate in cement mortar. Cement and Concrete Composites, 2001; 23(1): p. 111 - 118.
16. J.Monzó, J.Payá, M.V.Borrachero, S.Velázquez, L.Soriano, J.Rigueira. Reusing of spent FCC catalyst as a very reactive pozzolanic material: Formulation of high performance concretes. International RILEM Conference on the Use of Recycled Materials in Buildings and Structures, Spain. 8 - 11 November, 2004.
17. Mei-in Melissa Chou, Luming Chen, Sheng Fu Joseph Chou. Spent equilibrium catalyst for manufacturing fired bricks: A commercial production demonstration. International Journal of Environmental Sustainability. 2013; 8(3): p. 19 - 35.
Potential pathways for utilisation of spent FCC catalyst from Dung Quat refinery
Dao Thi Thanh Xuan - Vietnam Petroleum Institute, Nguyen Sura - Vietnam Petroleum Institute
Nguyen Hien Phong - Vietnam Petroleum Institute, Bùi Ngoc Pha - Ho Chi Minh City University of Technology
Email: xuandtt@pvpro.com.vn
Summary
The paper evaluates some pathways to recycle spent FCC catalyst at Dung Quat Refinery, with focus on some options to thoroughly utilise the spent FCC catalyst in a sustainable way, especially as building material. The results of testing in the laboratory and field survey show that the feasible pathways are ranked by spent catalyst recycling capacity as follows: raw material for cement production (20 - 200tons/day), pozzolanic material for cement additive production (> 15tons/day), clay for red brick production (15tons/day), and cement for concrete block production (11 - 17tons/day).
Key ordsw: Spent FCC catalyst, magnetic separation, recycle, building material, asphalt, concrete block, red brick.